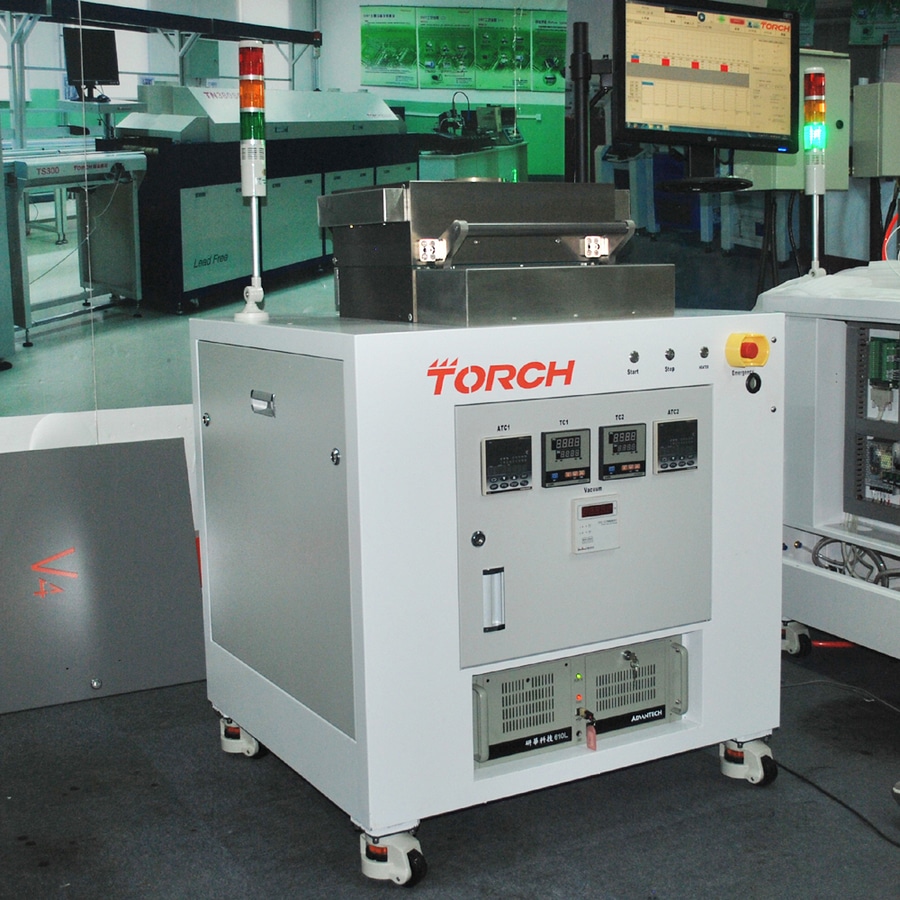
Ver traducción automática
Esta es una traducción automática. Para ver el texto original en inglés haga clic aquí
#Novedades de la industria
Breve introducción a la tecnología de soldadura por reflujo de láser
horno de reflujo al vacío
El uso de muestras para la prueba de reflujo ya es un método maduro para determinar si el reflujo del láser es adecuado para el producto y los parámetros del proceso que deben controlarse para lograr la calidad deseada de la unión soldada. Una cosa es estudiar cómo funciona el láser en teoría, pero otra cosa es aplicarlo en la práctica. Si se determina que el reflujo de la pasta de soldadura en un producto es un método viable por láser, entonces es posible trabajar con los proveedores de pasta de soldadura y sistemas de equipo láser para crear una buena combinación de materiales y equipo del producto.
CO2 laser es un láser de onda continua fuerte disponible actualmente. Un láser de dióxido de carbono puede producir luz infrarroja con una longitud de onda de unos 10.600 nm y una potencia del 20%. Los láseres de dióxido de carbono se utilizan principalmente para el corte y la soldadura de metales. El láser de dióxido de carbono está hecho de granate de aluminio de itrio dopado con metal de neodimio, usualmente llamado láser Nd:YAG. El láser Nd:YAG puede producir alta energía, con una longitud de onda de 1.064nm en el espectro infrarrojo. Al igual que los láseres de dióxido de carbono, se utilizan principalmente para cortar y soldar metales, y también para marcar metales y otros materiales. Los láseres de diodo de alta potencia (HDL) se basan principalmente en tiras de semiconductores de GaAs. Pueden proporcionar longitudes de onda que van de 790 a 980 nm y una potencia de salida de 50 vatios cada una. En los últimos años, los avances en la tecnología de enfriamiento de diodos, destinados a mantener la temperatura de los diodos, han aumentado significativamente la potencia, la vida útil y la eficiencia de los diodos.
Some los usuarios eligen utilizar el calentamiento por láser porque es una buena opción entre muchos métodos; mientras que otros encuentran que, debido a los muy limitados métodos de calentamiento disponibles, el láser será la solución al problema de calentamiento que enfrentan. La razón directa de la utilización del calentamiento por láser es el deseo de realizar un calentamiento local sin contacto. Aunque las motivaciones son diferentes, el propósito es el mismo: el reflujo se limita a un determinado lugar y no afecta a otras zonas, y debe completarse en poco tiempo, a fin de evitar eficazmente la conducción de más calor en otras partes del producto.
La pasta de soldadura se aplica a todas las almohadillas antes de colocar el cable. El calentamiento por láser se completa en una línea inmediatamente después del proceso de la pasta de soldadura, y el calor añadido sólo forma la unión de la soldadura. La soldadura está en estado fundido durante no más de 3 segundos. El calor transferido a la superficie del sustrato de vidrio durante el calentamiento es muy pequeño, lo que puede evitar la expansión térmica y el estallido. El aspecto de la unión soldada cumple con los requisitos de consistencia. Como en el proceso anterior, la pasta de soldadura se mancha en cada pin, y cada pin se calienta sólo con láser. Debido a la conducción del calor, el tiempo de calentamiento del primer pin es mayor que el del cuarto pin. La temperatura de calentamiento local es suficiente, y el calor total es seguro para las piezas de plástico.
Este artículo es de Internet. Si hay alguna infracción, por favor contácteme para eliminarlo.
Beijing TORCH Co,. Ltd se especializa en la investigación y producción de máquinas de soldadura láser al vacío de alta potencia. En la actualidad, se ha utilizado con éxito en muchas empresas de láser de alta potencia en China para sustituir los hornos de reflujo de vacío importados de Alemania. Si tiene alguna pregunta sobre la soldadura al vacío de láser de alta potencia, por favor contacte con nuestro personal técnico. www.torchsmt.com Consulta técnica: 15901426460