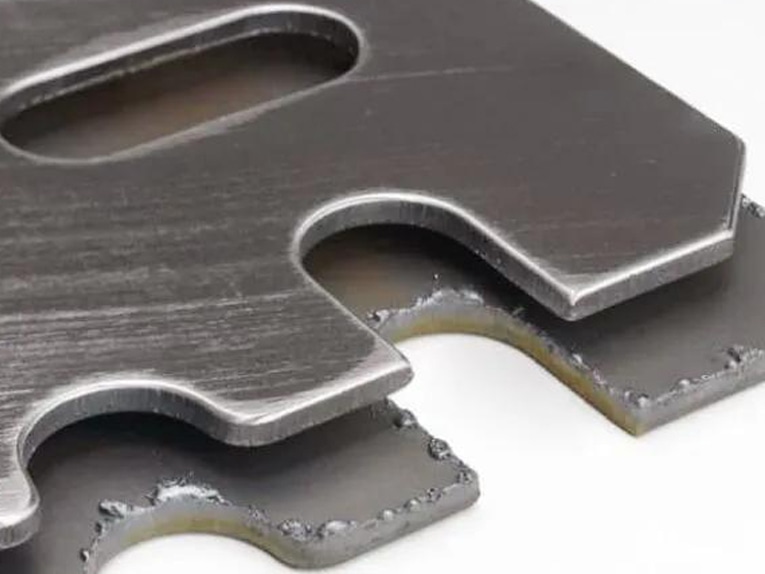
Ver traducción automática
Esta es una traducción automática. Para ver el texto original en inglés haga clic aquí
#Novedades de la industria
¿Cómo resolver el problema de las rebabas en los bordes en el corte de metales por láser de fibra óptica?
¿Cómo resolver el problema de las rebabas en los bordes en el corte de metales por láser de fibra óptica?
La tecnología de corte por láser de fibra es famosa por su alta precisión y eficacia en el procesamiento de metales, pero conseguir bordes de corte impecables es sin duda uno de los principales retos para garantizar la calidad superior y la integridad funcional del producto final. Las rebabas en los bordes, un problema común al que se enfrentan muchos fabricantes, no sólo erosionan la estética de un producto, sino que también pueden afectar a su precisión dimensional e incluso a su funcionalidad básica, que está directamente relacionada con la satisfacción del cliente y la competitividad en el mercado.
Por lo tanto, si desea saber cómo evitar el problema de las rebabas en los bordes en el uso del corte por láser de fibra metálica, lea este artículo. Este artículo le proporciona las causas fundamentales de las rebabas en los bordes y una serie de soluciones científicas y prácticas.
Comprensión de las rebabas en el corte por láser de fibra óptica
En primer lugar, vamos a entender lo que es la rebaba. Las rebabas son pequeñas partículas metálicas elevadas que se forman a lo largo del borde de corte de una pieza durante una operación de corte por láser. Varían en tamaño y forma, desde filamentos diminutos hasta protuberancias rugosas de mayor tamaño. Aunque su formación es en cierto modo inevitable, un exceso de rebabas puede indicar un problema con el proceso de corte, los ajustes de la máquina o las propiedades del material. En este punto, el usuario puede confiar en considerar si el problema es de la propia máquina o si se está comportando de forma inadecuada durante la operación, por ejemplo.
Causas fundamentales de las rebabas en los bordes
Excluyendo el problema de la propia máquina, al utilizar la máquina de corte por láser de fibra en el proceso de funcionamiento diario, ¿cuáles son las operaciones inadecuadas que dan lugar a rebabas? La siguiente es una lista de 5 puntos:
Velocidad de corte y ajustes de potencia incorrectos: Una potencia de láser o velocidad de corte incorrectas pueden provocar una fusión incompleta del material, dando lugar a rebabas.
Presión y caudal de gas: Una presión y un caudal insuficientes o excesivos del gas auxiliar (normalmente nitrógeno u oxígeno) pueden afectar a la calidad del corte y provocar la formación de rebabas.
Ajuste del enfoque: Un enfoque incorrecto del rayo láser sobre la superficie del material puede provocar un calentamiento y una fusión desiguales, lo que puede dar lugar a rebabas.
Propiedades del material: El tipo, grosor y estado de la superficie del metal pueden tener un impacto significativo en el proceso de corte y en la formación de rebabas.
Calibrado y mantenimiento de la máquina: Las máquinas mal calibradas o las piezas desgastadas, como lentes y boquillas, pueden reducir la calidad del corte.
Soluciones para reducir y eliminar las rebabas en los bordes
Una vez conocidas las causas de las rebabas, ¿qué se puede hacer para evitarlas? Este artículo ofrece las siguientes soluciones:
1. Optimizar los parámetros de corte
Ajustar la potencia y la velocidad del láser: Calibre cuidadosamente la potencia del láser y la velocidad de corte para que coincidan con las propiedades y el grosor del material. Los materiales más gruesos pueden requerir mayor potencia y velocidades más lentas, mientras que los materiales más finos pueden requerir menor potencia y velocidades más rápidas.
Ajuste la configuración del gas: Experimente con diferentes presiones y caudales de gas para encontrar el mejor ajuste que favorezca un corte limpio. El oxígeno puede aumentar la velocidad de corte, pero puede aumentar las rebabas en algunos materiales; normalmente se prefiere el nitrógeno para reducir las rebabas.
2. Mejorar el posicionamiento del enfoque
Garantice un enfoque preciso: Compruebe y ajuste periódicamente el enfoque del rayo láser para asegurarse de que está alineado con precisión con la superficie del material. Esto garantiza un calentamiento y una fusión uniformes, lo que reduce en gran medida la formación de rebabas.
3. Factores relacionados con el material
Preparación del material: Asegúrese de que la pieza de trabajo esté limpia, plana y libre de impurezas o defectos superficiales que puedan afectar a la calidad del corte.
Selección del material: Considere la idoneidad del material para el corte por láser y seleccione un grado de material que produzca un corte más limpio con rebabas mínimas.
4. Calibración y mantenimiento mejorados de la máquina
Calibración periódica: Realice una calibración periódica de la máquina para asegurarse de que todos los componentes funcionan correctamente y están alineados con precisión.
Mantenimiento preventivo: Implemente un sólido programa de mantenimiento que incluya la limpieza de las lentes, la sustitución de las boquillas desgastadas y la comprobación del estado general de los sistemas mecánico y eléctrico de la máquina.
5. Utilización de tecnología avanzada
Programación CNC: Se utiliza software de programación CNC avanzado para proporcionar un control preciso de los parámetros de corte y la optimización de la trayectoria, reduciendo la probabilidad de formación de rebabas.
Control de calidad automatizado: Integración de un sistema de control de calidad automatizado para comprobar los bordes de corte en busca de rebabas y otros defectos, de modo que puedan tomarse medidas correctivas de inmediato.