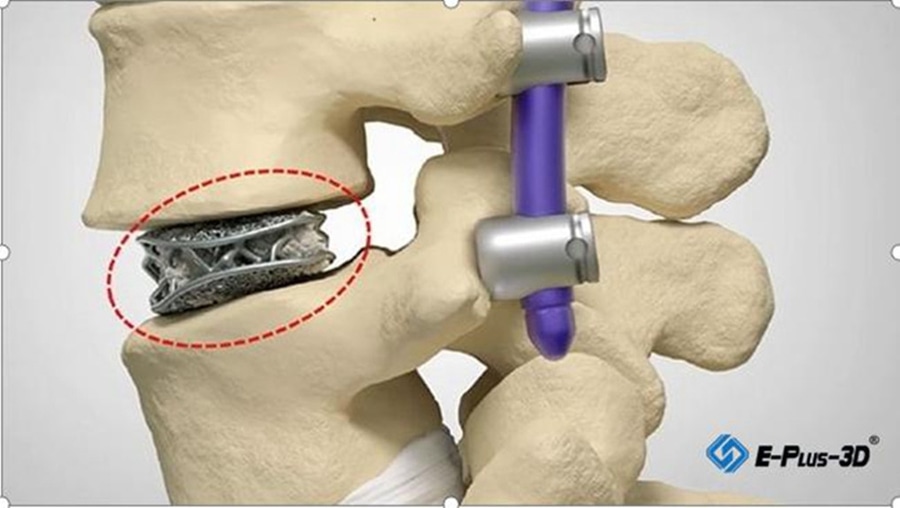
Ver traducción automática
Esta es una traducción automática. Para ver el texto original en inglés haga clic aquí
#Novedades de la industria
Fabricación de implantes de columna vertebral con la impresora 3D de metal EP-M250
Las impresoras 3D de metal de Eplus3D ofrecen soluciones para los implantes de columna vertebral
Personalización del procesamiento mediante fabricación aditiva
A medida que la tecnología de fabricación aditiva sigue avanzando, también lo hace su aplicación y accesibilidad. El prototipado rápido y el utillaje están a la vanguardia de la impresión 3D, pero el objetivo siempre ha sido poder imprimir directamente para la producción o directamente para la fabricación. El mundo médico no es una excepción. Aunque las primeras aplicaciones de la impresión 3D en el campo de la medicina fueron la creación de prototipos y guías de visualización, esta tecnología ha llegado finalmente a la fase de implantes personalizados mediante impresoras 3D de última generación.
Eplus3D se mantiene fiel a su visión de ofrecer una solución 3D personalizada para todos. Con su última línea de impresoras 3D de metal, Eplus3D está llamando la atención de socios médicos que están aprovechando increíblemente esta tecnología. Uno de los socios pioneros en la creación y uso de implantes médicos es MANTIZ.
MANTIZ es una empresa de dispositivos médicos que utiliza ingeniería y tecnología superiores para conseguir una vida activa y sin dolor para todos los pacientes con trastornos de la columna vertebral. MANTIZ ha obtenido la certificación de la KFDA (aprobación de dispositivos médicos) y figura en la lista de HIRA (Revisión y Evaluación del Seguro Médico) en Corea del Sur. MANTIZ comenzó a desarrollar implantes de jaula impresos en 3D en 2018 con la aprobación y financiación del gobierno. En mayo de 2019, lanzaron un sistema de jaula PANTHER impreso en 3D para la cirugía PLIF (Poster Lumbar Interbody fusion) / TLIF / OLIF / ALIF. Este proceso utiliza implantes de jaula impresos en 3D sin subcontratar el proceso de fabricación a un tercero. Esto ahorra tiempo y dinero a los clientes y reduce la posibilidad de errores de producción. MANTIZ utiliza la impresora 3D metálica EP-M250 de Eplus3D para fabricar jaulas impresas en titanio 3D para su uso en la cirugía de implantes. Todo el proceso de conformación del implante se realiza internamente en MANTIZ. La jaula se diseña según las especificaciones. El tamaño, el material, la forma y la porosidad son esenciales para la eficacia del implante. El diseño completo de la jaula se carga en el software de la impresora, donde está listo para la impresión. El gran lecho de impresión de la EP-M250 puede utilizarse para imprimir más de 50 implantes individuales en una sola estructura. Tras el trasplante, el hueso y el tejido circundante comienzan a fusionarse con el implante, creando una estructura fuerte en la columna vertebral del paciente. Hongwon Yoon (CTO de MANTIZ), el inventor del sistema de jaulas de impresión 3D PANTHER de MANTIZ, dijo: "Hemos completado el desarrollo de un implante de jaula de titanio impreso en 3D más mejorado utilizando la impresora metálica 3D EP-M250. Los resultados de las pruebas mecánicas demuestran la seguridad y funcionalidad del implante. Impresión 3D La proporción media de poros cerrados del componente sólido de titanio es del 3%, lo que favorece la unión de la proteína para la fusión ósea con las células madre mesenquimales"
Consulte las imágenes que aparecen a continuación para ver todo el proceso, desde el diseño hasta la impresión, pasando por la incrustación. El mundo de la impresión 3D está en constante evolución, y a medida que la tecnología avanza, también lo hace su aplicación directa. La personalización al alcance de la mano, más asequible que nunca. Las industrias automovilística, aeroespacial y médica ya imprimen en 3D directamente en la producción, lo cual es sólo una parte de las capacidades de la tecnología. Póngase en contacto directamente con Eplus3D (info@eplus3d.com) para obtener más información sobre cómo incorporar la fabricación aditiva a su flujo de trabajo diario.
Proceso de diseño e impresión en 3D:
Diseño integrado con software 3D profesional
Preparación de las piezas en el software de impresión 3D
Uso de la EP-M250 de Eplus3D para la impresión 3D
Proceso de impresión 3D en metal en la cámara
Jaulas impresas en 3D
Procesamiento posterior que incluye el tratamiento térmico, la eliminación de los soportes, el tratamiento de la superficie, la desinfección, etc.
Sólo después de una serie de pruebas mecánicas, la jaula impresa en 3D puede aplicarse en la cirugía
A través del proceso de "diseño-impresión 3D-post-proceso-prueba", el PANTHER puede estar listo para la cirugía. Actualmente, el PANTHER ya se ha aplicado en el tratamiento de pacientes.
Ventajas de la jaula de titanio impresa en 3D:
El PANTHER ha sido formulado para optimizar el crecimiento óseo durante los procedimientos de la columna vertebral, con un rango de tamaño de poro medio de 630-730μm en la superficie de contacto de las placas terminales de la columna vertebral y una porosidad media de la sección de malla en el rango de 70% -80%.
El potencial es medio
Acerca de Eplus3D
Eplus3D fue fundada en 2014, el equipo técnico principal tiene más de 25 años de acumulación de tecnología AM, se ha dedicado a la investigación y desarrollo de sistemas de fabricación aditiva de grado industrial y tecnologías de aplicación, con MPBF™ (Metal Powder Bed Fusion) , PPBF™ (Polymer Powder Bed Fusion) y tecnología de impresión 3D de litografía estéreo, proporciona soluciones de aplicación profesional para los campos de la industria aeroespacial, automotriz, herramientas, salud, dental, bienes de consumo, fabricación de precisión, etc.
Eplus3D cuenta con dos instalaciones en Pekín y Hangzhou, con una inversión anual en investigación científica de más del 20% de los ingresos con amplias patentes de invención, patentes de modelos de utilidad, derechos de autor de software y patentes de apariencia. Ha conseguido grandes logros en el diseño, el equipo, el proceso, el software, los materiales y el posprocesamiento para la fabricación aditiva, con equipos que se han exportado a más de 40 países y regiones como Europa, América, Japón, Corea del Sur y el Sudeste Asiático, etc.
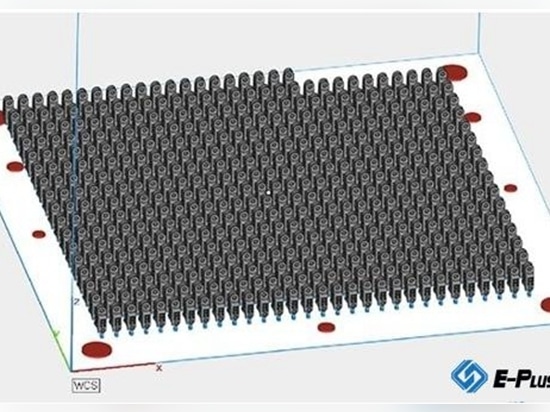
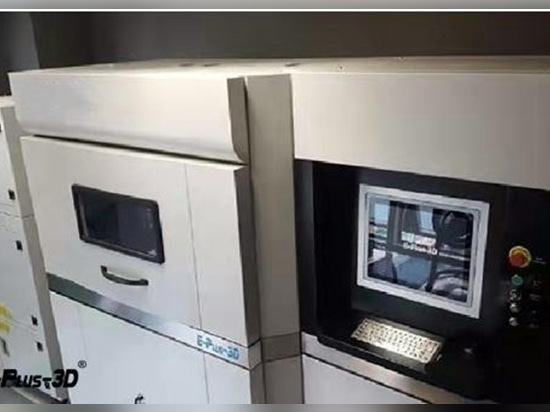

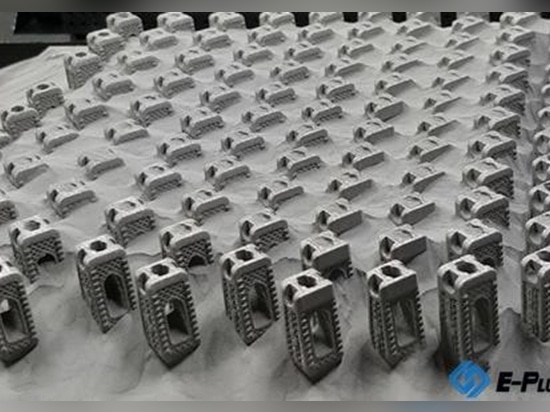
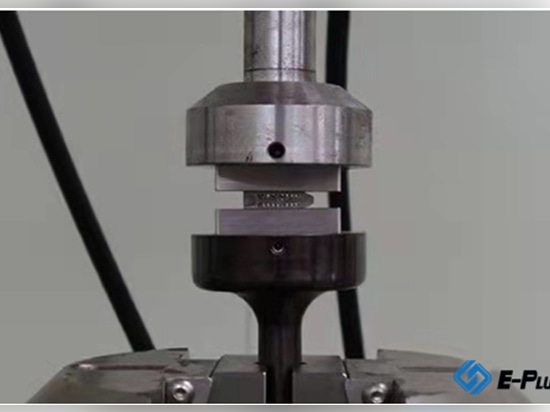
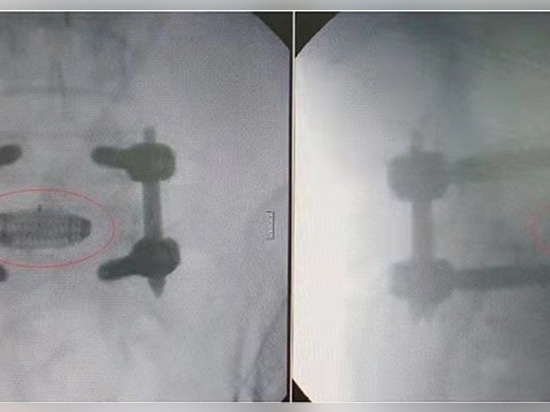
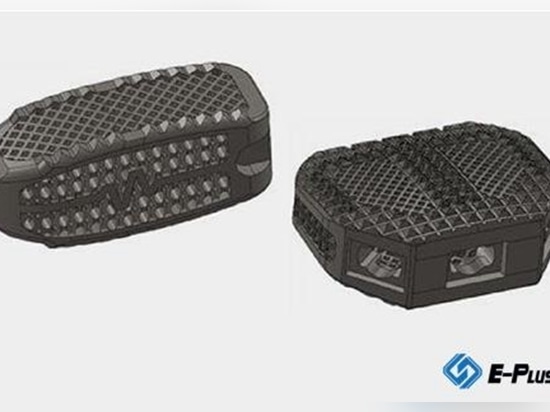