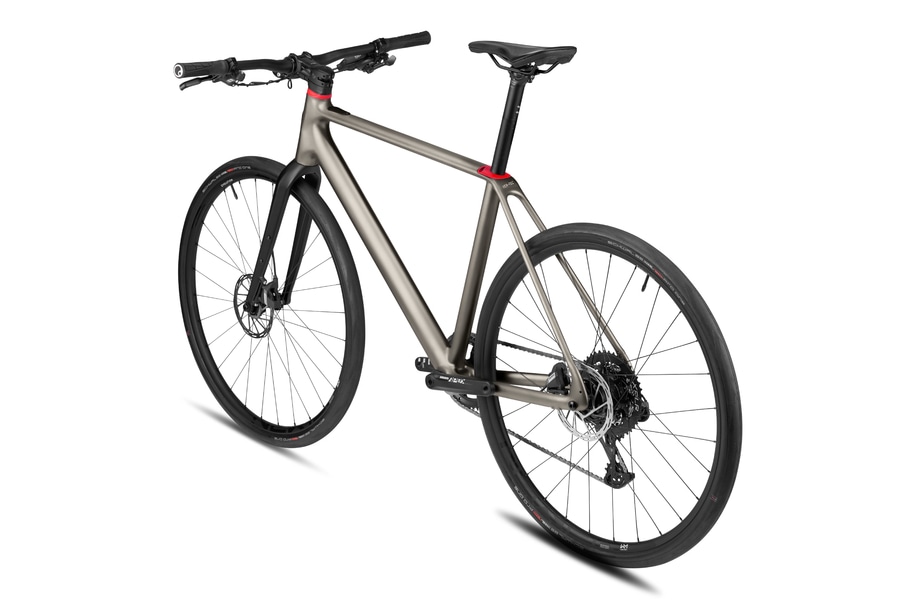
Ver traducción automática
Esta es una traducción automática. Para ver el texto original en inglés haga clic aquí
#Novedades de la industria
Fabricación aditiva de metales: innovación más rápida para la industria de la bicicleta
Noticias de empresa
RESUMEN
Construcción del primer cuadro de bicicleta de titanio de aspecto monocasco con integración total de la batería en todo el mundo fabricado con tacos de titanio impresos en 3D.
La integración de tecnologías innovadoras de Asia a Europa Central, manteniendo al mismo tiempo la eficiencia de costes, ha sido un reto importante en el proceso de desarrollo.
Tras una larga trayectoria, el fabricante de bicicletas Möve desarrolló el principio de utilizar la fabricación aditiva (AM) para producir los conectores entre los tubos del cuadro de una bicicleta. Después de evaluar posibles socios para tener éxito en este avance tecnológico, Möve identificó la necesidad de una excelente colaboración y experiencia que ofreciera la rentabilidad, el diseño y el rendimiento en línea con un único fabricante.
El equipo de Eplus3D se centró en optimizar la estructura de costes para la producción de conectores y garantizar la viabilidad de escalar el proyecto a la producción en serie. Al aplicar este enfoque y apoyar a Möve en la fabricación de tubos de titanio nunca antes realizados para el cuadro, el proyecto se aceleró oportunamente en un mínimo de cuatro meses, lo que dio lugar a la creación de un cuadro de e-bike nuevo y distintivo que conservaba el diseño monocasco original previsto.
Este proyecto ilustra el potencial de la industria de la bicicleta gracias al uso de la impresión metálica en 3D y a una valiosa combinación de trabajo de ingeniería de todas las partes. El reconocimiento de los retos es fundamental para las industrias de la movilidad, ya que las impulsa a replantearse y rediseñar el modo en que se fabrican las piezas, ofreciendo un producto duradero y de alta calidad que mejore la experiencia del usuario final.
INTRODUCCIÓN A MÖVE
Möve, una empresa con una larga presencia en Turingia, Alemania, ha estado combinando ingeniería avanzada con una calidad de fabricación excepcional desde 1897. Actualmente, la fabricación tiene su sede en Katharinenberg, Turingia. La empresa da prioridad a la etiqueta "Made in Germany", garantizando que sus productos se fabrican con los más altos estándares desde el principio, hasta el producto acabado. Möve diseña, ingenia y desarrolla soluciones innovadoras por y para las personas, para producir la e-bike perfecta, adaptable a las necesidades de las personas. El reconocimiento del principio de los cuatro ojos garantiza la excelente calidad Möve de acuerdo con los estándares de ingeniería.
EL RETO
Möve reconoció las limitaciones de la industria, como la mayoría del trabajo manual en la construcción de cuadros convencionales, los altos costes de las herramientas para cuadros de bicicletas y (e-)bikes de alto nivel de estandarización, la estimación incorrecta del volumen anual de cuadros de bicicletas que resulta en una reducción de las ventas, y el desperdicio de cuadros de fibra compuesta.
El objetivo de ser tan rentable como un cuadro de bicicleta fabricado en Asia, con una tecnología innovadora que devuelve puestos de trabajo de fabricación a Europa central, combinado con un objetivo de rendimiento de un cuadro de carbono, fueron sin duda los principales retos a los que hacer frente. Durante la fase de desarrollo, el suministro de tubos de titanio de forma ovalada y baja tolerancia parecía ser un problema importante, tanto desde el punto de vista financiero como de tiempo. Para recibir los tubos hidroformados, habría que desarrollar y producir las herramientas necesarias, lo que tenía la posibilidad de acabar con el proyecto antes de que despegara definitivamente.
LA SOLUCIÓN
Tras identificar los retos iniciales, se creó el primer diseño de conectores de fabricación aditiva entre los tubos. Al tiempo que se reducía al mínimo la cantidad de material, Möve encontró en Eplus3D el mejor socio, ya que ofrecía los parámetros de impresión más avanzados, conocimientos técnicos y asistencia en el diseño, lo que se tradujo en un precio razonable por pieza. Llegados a este punto, el ingeniero Tobias Spröte vio todo el potencial y los beneficios transformadores de la AM metálica como el siguiente paso para construir el primer cuadro de bicicleta de titanio impreso en 3D del mundo. Como resultado, y tras un trabajo de ingeniería combinado de todas las partes, Möve llegó a la conclusión de que la tecnología de impresión 3D Metal Powder Bed Fusion (MPBF™), combinada con el uso de material Ti6Al4V de alta resistencia, era la única capaz de satisfacer sus requisitos de diseño, rendimiento y coste establecidos para producir los tacos de la bicicleta.
Eplus3D ayudó a Möve a abastecerse de tubos de titanio de alta calidad, que también se fabricaron totalmente por adición con la impresora de metal de gran tamaño EP-M650 de Eplus3D utilizando material Ti6Al4V. Estos tubos se sustituirán en la producción en serie por tubos de titanio hidroformados, pero han acelerado la realización del proyecto en 6 meses. Además, se han podido reducir unos costes de utillaje muy caros e inflexibles.
Entre los numerosos proveedores, Eplus3D destacó por su compromiso de ir más allá de la mera producción y adoptar un enfoque reflexivo ante los retos que surgen en la fase de posproducción. El equipo de ingeniería de Möve trabajó con Eplus3D para desarrollar las soluciones innovadoras, reconociendo la necesidad de retirar y reciclar eficazmente la estructura de soporte.
En colaboración con Möve, se abordaron estas cuestiones para mejorar su producción en serie. Al centrarse en la reducción de las estructuras de soporte, se optimizaron los parámetros clave para equilibrar la velocidad de impresión con las propiedades deseadas del producto. Este enfoque estratégico no sólo optimizó el proceso de postproducción, sino que también se alineó con los objetivos de calidad y eficiencia de Möve. Además, Möve ha creado una cadena de procesos muy estudiada para fabricar toda la bicicleta en sus instalaciones. Esto incluye el postprocesado de los componentes de fabricación aditiva, como el tratamiento de superficies y el mecanizado, así como el montaje de la bicicleta mediante una tecnología de encolado patentada. Esto ayuda al usuario a reciclar su bicicleta y repararla de forma mucho más económica en comparación con otras bicicletas fabricadas con fibra de carbono.
Como explica Enis Jost, director general adjunto de Eplus3D Alemania: "La estructura de costes viene determinada principalmente por el tiempo de funcionamiento del sistema, la madurez de los parámetros de procesamiento utilizados y la velocidad de impresión asociada a los mismos. Dado que se utilizan muy pocos gramos de material para crear las orejetas y con la mayor productividad del sistema que proporcionan las máquinas de Eplus3D, el coste de la materia prima tiene menos efecto en este caso. Sin embargo, el coste del polvo de titanio AM está bajando, lo que ayuda a crear un caso de negocio aún mejor. Al mismo tiempo, los procesos de Eplus3D son cada vez más productivos"
LOS RESULTADOS
La aplicación de la tecnología de impresión Metal 3D, en combinación con los conocimientos de ingeniería 3D, ha permitido obtener notables beneficios, como ahorro de costes, mayor calidad de los productos, mejora de la eficiencia y sostenibilidad.
REDUCCIÓN DE COSTES
Este proyecto es especialmente beneficioso para una producción en serie económicamente viable, ya que reduce los costes iniciales asociados a los cuadros estandarizados de gran volumen para bicicletas y e-bikes. Con conjuntos de parámetros de mayor espesor de capa y múltiples opciones de configuración de la máquina, Eplus3D proporciona una solución optimizada que puede satisfacer perfectamente las necesidades del cliente y, por lo tanto, puede reducir los costes de fabricación de piezas, almacenamiento e incluso permitir la fabricación personalizada de bicicletas bajo demanda.
AVANCES EN MATERIALES
Analizando con precisión e implementando el uso correcto de materiales como la aleación de titanio (Ti6Al4V), Möve pudo mantener altos estándares de rendimiento durante la producción, garantizando la estabilidad, funcionalidad y durabilidad del resultado final. El material tiene la mejor relación de rendimiento y, por lo tanto, es la mejor opción para este tipo de aplicación.
MAYOR FLEXIBILIDAD DE DISEÑO
El uso de la tecnología Metal AM junto con la experiencia en ingeniería de ambas partes permitió la creación de geometrías complejas, facilitando el diseño monocasco del cuadro de la e-bike de Möve Avian. Esto se ha logrado sin comprometer la integración de la batería, que permanece discretamente oculta dentro del tubo de titanio inferior, mejorando así tanto el diseño como la funcionalidad de la e-bike. El proceso de AM también ha facilitado diseños iterativos más rápidos, reduciendo el tiempo total de desarrollo y garantizando la creación de una bicicleta específica para el ciclista cuando sea necesario.
Estos resultados han sido posibles gracias al proceso Ti6Al4V, actualmente disponible y altamente productivo, que es al menos dos veces más rápido que el de nuestros competidores en el mercado. En consecuencia, Eplus3D es capaz de ofrecer una estructura de costes significativamente más atractiva a los clientes que buscan nuestro apoyo para mejorar sus capacidades de prototipado, por un lado, pero aún mucho más al dar el paso a la producción en serie con esta tecnología.
NOTABLES CARACTERÍSTICAS DEL MÖVE AVIAN BASADAS EN LA TECNOLOGÍA DE IMPRESIÓN 3D SOBRE METAL
FABRICADO EN ALEMANIA
Cada paso de la producción, el diseño y la ingeniería lleva la marca de excelencia "Made in Germany". La deslocalización de la cadena de suministro, utilizando los principios de near-shoring, abre nuevas posibilidades para que la industria de la bicicleta tenga un control más estricto sobre sus proveedores. Junto con el alto nivel de automatización, permite a los fabricantes producir localmente, con un gran volumen de producción y, por tanto, de forma rentable.
SUPERFICIE DE TITANIO DIFERENCIADA
Gracias a la tecnología de granallado, la superficie de titanio se alisa y adquiere un aspecto uniforme y mate. Convirtiéndose en el sello distintivo de la nueva Möve Avian.
OPTIMIZACIÓN DEL PESO
Reducción del peso de la bicicleta gracias a la ligereza de los cuadros de titanio, mediante la reducción de las estructuras de soporte después de la producción. Esto se ha combinado con una batería integrada de 250 Wh, lo que ha dado como resultado un peso de 11,8 kg.
APLICACIÓN DE LA TECNOLOGÍA FLEXFIT
El equipo de Möves diseñó y optimizó las cámaras adhesivas para pegar los tacos y los tubos, así como sus canales de inyección, para lograr un llenado superior al 98% en las cámaras adhesivas.
LA FABRICACIÓN ADITIVA ES EL FUTURO DE LA INDUSTRIA DE LA BICICLETA
La entrada de Möve en el campo de la AM no sólo representa un cambio significativo en la forma de construir cuadros de bicicleta, sino que también muestra al resto de la industria el potencial y los estándares de alta calidad que se pueden alcanzar con esta tecnología. Möve está estableciendo nuevos estándares en este campo, allanando el camino para futuras innovaciones y estableciéndose como líderes en esta área.
Esta transformación es claramente visible a través de los esfuerzos de colaboración y la experiencia aportada tanto por Möve como por Eplus3D. Juntos, estamos ampliando los límites de lo que es posible en el diseño y posterior fabricación de cuadros de bicicleta, mostrando un compromiso para remodelar el panorama de la industria". Como explica Enis Jost, Director General Adjunto de Eplus3D Alemania: "El potencial de la AM en la industria de la bicicleta podrá explorarse plenamente cuando los fabricantes tradicionales empiecen a diseñar para la personalización de procesos y usuarios, de forma similar a otros dispositivos conectados emocionalmente, como coches y motos. Entre los materiales posibles se encuentran los de alto rendimiento, como Scalmalloy® o titanio, pero también aleaciones de fundición típicas como AlSi10Mg o incluso acero inoxidable" Este proceso puede ser especialmente beneficioso para los componentes de bicicletas - palancas, abrazaderas, equipo de cambio y pedales -, que actualmente suelen fabricar hasta 10.000 piezas al año.
Para desbloquear el mercado potencial de MPBF™, "el equipo de ingeniería de Eplus3D está abierto a apoyar a cualquier empresa de movilidad para alcanzar sus objetivos de rendimiento y coste con Metal AM mediante el desarrollo de un proceso de fabricación que también sigue el principio de near-shoring, apoya la gran necesidad de productos personalizados o de producción propia", explica Enis Jost. Además, para cada cliente se realiza un cálculo de costes estándar y una revisión básica del diseño. Gracias a la arquitectura totalmente abierta del sistema, el cliente puede sin duda desarrollar su propia propiedad intelectual (PI) basándose en el proceso suministrado con la máquina instalada, con lo que aumenta aún más su experiencia en el campo y mejora el proceso.
ACERCA DE EPLUS3D
Desde la fundación de la primera máquina PBF en China en 1993, Eplus3D se dedica a la investigación y el desarrollo de sistemas de fabricación aditiva de grado industrial y tecnologías de aplicación que utilizan con MPBF™ (Metal Powder Bed Fusion) y PPBF™ (Polymer Powder Bed Fusion) tecnología de impresión 3D. Eplus3D ofrece soluciones de aplicación profesionales para los sectores aeroespacial y de aviación, energía, petróleo y gas, automoción, herramientas, sanidad, bienes de consumo y fabricación de precisión.
Eplus3D cuenta con cuatro instalaciones en Pekín, Hangzhou, Stuttgart y Houston, con una inversión anual en investigación científica de más del 20% de los ingresos con patentes de invención completas, patentes de modelos de utilidad, derechos de autor de software, así como patentes de apariencia. Ha conseguido grandes logros en el desarrollo de diseños, procesos, software, materiales y posprocesamiento para la fabricación aditiva y ha implantado con éxito soluciones de AM en las instalaciones de clientes de más de 40 países y regiones como Europa, América, Oriente Medio, Asia Oriental y el Sudeste Asiático.
Sede de APAC
Eplus3D Tech Co., Ltd.
Hangzhou, China
P: +86-571-83819589
No. 118 Yanshankong Road, Wenyan, Xiaoshan, Hangzhou, Zhejiang, China, 311258
Región EMEA
Eplus3D Tech GmbH
Ludwigsburg, Alemania
P: +49-7141-3888118
Pflugfelder Str. 23, 71636 Ludwigsburg, Alemania
Región de América
EPLUS 3D TECH INC
Houston, EE.UU
P: +1 (281) 302-6160
12425 W Airport Blvd, unidad 201, Sugar Land, TX, 77478