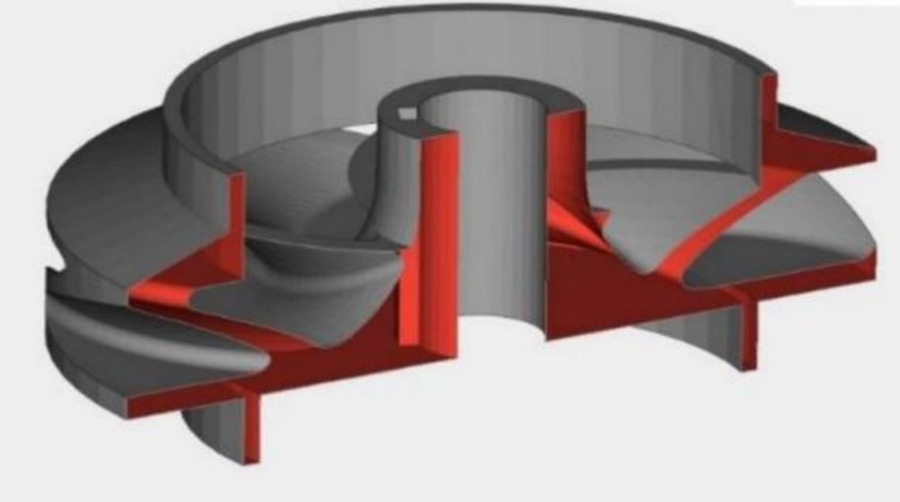
Ver traducción automática
Esta es una traducción automática. Para ver el texto original en inglés haga clic aquí
#Libros blancos
Investigación de la fabricación de un impulsor cerrado de acero inoxidable 316L utilizando la máquina de fusión de lecho de polvo láser Eplus3D
Noticias de empresa
Yousef Alhorr1, Qusai Alkhalaf 2*
1PhD, Presidente de la Organización del Golfo para la Investigación y el Desarrollo (GORD), QSTP, Doha, Qatar
2PhD, Jefe de operaciones del centro de fabricación aditiva. Organización del Golfo para la Investigación y el Desarrollo (GORD-3D), QSTP, Doha, Qatar
Resumen: La fabricación de impulsores cerrados mediante la tecnología de Fusión de Lecho de Polvo Láser conlleva complejidades inherentes, exigiendo una atención meticulosa al diseño de la estructura de soporte, la determinación del ángulo de construcción y la densidad de energía descendente para garantizar el éxito de la producción. Este estudio explora el uso de acero inoxidable 316L en la fabricación de impulsores cerrados mediante LPBF. El objetivo es investigar el impacto de los parámetros del proceso y los ángulos de construcción en la calidad de fabricación de los impulsores. Además de estudiar el efecto de la densidad de energía en los valores de rugosidad superficial y dureza del impulsor. La investigación examina ángulos de construcción de 0˚, 30˚ y 90˚ para un impulsor cerrado, revelando que un ángulo de construcción de 30˚ produce piezas impresas con éxito. Además, para conseguir impulsores cerrados sin defectos, es imprescindible mantener la densidad de energía de la superficie inferior entre el 80% y el 100% de la densidad de energía de la superficie interior. La dureza máxima y la rugosidad superficial mínima se registraron a 233 HV y 12,79 µm, respectivamente, cuando la densidad de energía fue de 41,66 J/mm³ y 55,55 J/mm³, respectivamente. La novedad de este estudio radica en la fabricación de impulsores cerrados utilizando acero inoxidable 316L mediante fusión de lecho de polvo por láser.
Palabras clave: fabricación aditiva; fusión de lecho de polvo láser (LPBF); impulsor cerrado; fusión selectiva por láser (SLM)
1. Introducción
El impulsor constituye un elemento indispensable en los sistemas de bombeo, ya que desempeña un papel fundamental a la hora de determinar la capacidad hidráulica y la eficiencia del caudal en la turbomaquinaria [1]. Se distinguen cuatro clases geométricas: impulsores abiertos, cerrados, semiabiertos y de tornillo. El impulsor cerrado (IC) es especialmente difícil de fabricar debido a sus complejas características internas. Los métodos tradicionales consisten en ensamblar los impulsores cerrados en segmentos, como la carcasa, el cubo y los álabes, empleando técnicas de unión como la soldadura, la soldadura fuerte o el remachado. Sin embargo, estos métodos introducen defectos y distorsiones y resultan inadecuados para aplicaciones exigentes de alto rendimiento. En consecuencia, se hace imperativa la adopción de CI de una sola pieza, ya que las técnicas de fabricación como la fundición a presión, el fresado integral y el mecanizado por descarga de electrones (EDM) son especializadas pero requieren mucho tiempo, mano de obra cualificada y configuraciones especializadas, lo que eleva los costes generales de fabricación [2].
Para hacer frente a estos retos, la fabricación aditiva (AM) se perfila como una solución transformadora para la CI de una sola pieza, ya que ofrece la posibilidad de mitigar las incertidumbres de los plazos de entrega y mejorar la flexibilidad del diseño [3,4]. La Fusión Láser de Lecho de Polvo (LPBF), una destacada tecnología de AM, funde selectivamente el polvo capa por capa mediante un láser, permitiendo así la producción de piezas de formas intrincadas con una alta resolución de aproximadamente 50 micrómetros [6-9]. La LPBF ha demostrado un éxito considerable en la impresión de piezas complejas a partir de una serie de materiales metálicos, como aceros, aleaciones de níquel, aleaciones de titanio y aleaciones de Inconel [10-11].
Aunque pueden utilizarse tecnologías alternativas como el método de deposición fundida (FDM) para la impresión de hélices, su idoneidad se limita generalmente a aplicaciones menos intrincadas [12]. Por el contrario, el LPBF con impresión metálica es indispensable para conseguir funcionalidades de alto rendimiento [13]. Numerosos estudios subrayan el éxito de la aplicación de LPBF en la impresión de impulsores abiertos, abarcando investigaciones sobre las propiedades de los materiales, predicciones de la historia térmica y optimización de los parámetros del proceso [14-16]. Cabe destacar que el LPBF permite la fabricación de impulsores a partir de materiales reciclados, lo que acentúa su potencial para las prácticas de fabricación sostenibles [17]. A pesar de estos avances, los retos persistentes giran en torno a la consecución de impresiones 3D precisas y sin defectos. La deformación geométrica, ejemplificada por manchas oscuras y uniones metalúrgicas subóptimas entre capas, contribuye a problemas polifacéticos, como fallos geométricos, imprecisiones dimensionales, estructuras incompletas e impedimentos en el proceso de impresión [27]. Además, los defectos de los restos, que surgen de la presión de retroceso del vapor metálico durante la impresión, provocan que el polvo no fundido o el metal fundido se desprendan e influyan en el estado de fusión de las capas sucesivas, comprometiendo en última instancia la resistencia a la tracción y el rendimiento a fatiga de la pieza impresa [28- 29].
El acero inoxidable está ampliamente considerado como una excelente opción para la impresión por fusión en lecho de polvo láser. Un impulsor cerrado de acero inoxidable tiene numerosas aplicaciones, como en los sistemas de aguas residuales. Las principales preocupaciones a la hora de imprimir acero inoxidable son la gestión de la densidad de energía y la optimización del ángulo del material de soporte. Esta métrica engloba el aporte de energía por unidad de volumen durante el proceso de fusión de capas. En concreto, la densidad de energía se define como:
En la ecuación, P (W) representa la potencia del láser, v denota la velocidad de barrido (mm/s), h (μm) denota la distancia de eclosión, z (μm) indica el grosor de la capa, Los niveles bajos de energía conducen a la porosidad por falta de fusión, lo que indica una energía insuficiente para la fusión completa del polvo y da lugar a porosidades irregulares generalizadas en toda la pieza [31]. Los valores de densidad de alta energía provocan sobrefusión, a menudo denominada porosidad de ojo de cerradura [32-34]. En este estado, las pistas fundidas se fragmentan, provocando una solidificación no uniforme y defectos finales en la pieza. La región estacionaria garantiza la fusión completa de las pistas y la unión de las capas dentro de los límites de densidad de energía. La complejidad de la impresión de las pistas es clave en la fusión de lecho de polvo por láser, siendo los metales más comunes el Inconel 625 y el Inconel 718.
Hasta donde saben los autores, existe una notable ausencia de investigaciones sobre la aplicación del acero inoxidable 316L en la impresión por fusión de lecho de polvo con láser de impulsores cerrados. Por lo tanto, esta investigación pretende llenar este vacío mediante la producción de un impulsor cerrado a través de la fusión de polvo por láser. Nuestro principal objetivo es analizar el impacto de variables como el material de soporte, el ángulo de construcción y la densidad de energía de la piel descendente en el proceso de fabricación del impulsor cerrado. Además, pretendemos investigar el efecto de la densidad de energía sobre la rugosidad y la dureza de la superficie.
2. Método y trabajo experimental
El método y el trabajo experimental aplicados aquí para estudiar el ángulo de la estructura de soporte y las propiedades mecánicas finales del rodete se ilustran en la figura 1. El método se divide en tres fases. La primera fase consiste en seleccionar el ángulo adecuado de la estructura de soporte entre 0°, 30° y 90°. Una vez determinado el ángulo optimizado, se examina la textura de la microestructura mediante escaneado SEM para la fase 2. La fase III se centra en examinar el efecto de la densidad de energía sobre la rugosidad y la dureza.
2.1 Diseño del impulsor
Se diseñaron dos tamaños diferentes de impulsores cerrados: uno con un diámetro de 145 mm y otro con un diámetro de 100 mm. El impulsor está dividido en tres secciones principales a lo largo de su dirección de construcción: la base, la sección media y la sección de aletas. Estas secciones tienen estructuras complejas, incluidas varias geometrías de aletas finas inclinadas, lo que convierte la fabricación en un proceso difícil. Dado que la sección transversal cambia a lo largo de la altura del impulsor, el área explorada por el láser varía de una capa a otra. La estructura del impulsor se muestra en la figura 2.
2.2 Ángulo de construcción y estructura de soporte de los impulsores cerrados
Para determinar el ángulo de construcción óptimo para un rodete cerrado dentro de la cámara de construcción de la máquina LPBF, se seleccionaron tres ángulos comunes (90˚, 30˚ y 0˚) para evaluar su impacto en el proceso de fabricación. La selección de los soportes depende de la forma del impulsor, eligiéndose soportes en forma de bloque, como se representa en la figura 3. Numerosos estudios han demostrado que el empleo de soportes macizos o en bloque da lugar a una mejora de las características mecánicas de las muestras y a un acabado superior de la superficie, especialmente en el caso de las superficies salientes. Estos soportes facilitan una disipación eficaz del calor, optimizando así los resultados. La figura 4 ilustra la vista del soporte en bloque, con soportes en árbol añadidos para facilitar su retirada. El software utilizado para la preparación de los soportes fue MaterialsMagic, y para el diseño se utilizó SolidWorks.
2.3 Procesamiento de LPBF
Los rodetes se fabricaron utilizando una máquina LPBF EP-M260 de Eplus3D, empleando material de acero inoxidable 316L. La Eplus3D M260 está situada en el Centro 3D de la Organización del Golfo para la Investigación y el Desarrollo (GORD 3D). La vista real de la máquina Eplus3D se muestra en la figura 5. Los impulsores se diseñaron con diámetros de 145 mm y 100 mm. La impresión de un impulsor de 145 mm de diámetro con un ángulo de construcción de 90˚ tarda aproximadamente 103 horas y requiere 4.393 capas con un grosor de 30 µm. La impresión de un impulsor de 145 mm de diámetro con un ángulo de construcción de 30˚ requiere 53 horas y 3.124 capas. Un impulsor de 100 mm de diámetro impreso con un ángulo de construcción de 0˚ requiere unas 38 horas, con 1.833 capas.
La selección de parámetros para imprimir impulsores cerrados es crucial, y la densidad de energía es una consideración especialmente importante. El revestimiento inferior se encuentra en las tres primeras capas por encima del material de soporte, lo que puede dañar la pieza durante el proceso de impresión. Por lo tanto, es esencial seleccionar perfectamente la densidad de energía de la piel inferior, ya que sirve de puente entre el material de soporte y el núcleo del impulsor. Por otro lado, la densidad de energía de la piel interior corresponde al núcleo del impulsor. Según la bibliografía, lo ideal es que la densidad de energía en la piel inferior oscile entre el 50% y el 80% de la densidad de energía en la piel interior. En el presente estudio, se consideran dos casos para la densidad de energía de la piel inferior: uno en el que la densidad de energía de la piel inferior es igual a la densidad de energía de la piel interior, y otro en el que la densidad de energía de la piel inferior se fija en el 20% de la densidad de energía de la piel interior. En la figura 6 se muestra la vista actual del proceso de impresión. En la Tabla 2 se detallan los parámetros del proceso con estas variaciones de densidad de energía para cada fase.
2.4 Prueba de dureza
Los ensayos de microdureza Vickers se realizaron siguiendo la norma ASTM E92-17 utilizando una máquina de ensayos de microdureza Vickers. Un penetrador de punta de diamante piramidal aplicó una fuerza específica (300 gf, 2,94 N) a la superficie de la muestra durante 10 segundos por penetración. Se realizaron tres indentaciones en cada muestra, excluyendo cualquier indentación dentro de los poros. El valor de dureza Vickers (HV) se determinó midiendo las diagonales de cada indentación con punta de diamante, promediadas mediante el software de la máquina. la media de estas mediciones se consideró la dureza de la muestra.
2.5 Preparación de la superficie y caracterización microestructural
Se fabricó una muestra de 5 mm de espesor con el impulsor. Las muestras se sometieron a abrasión utilizando discos abrasivos de carburo de silicio de distintos niveles de tosquedad (grano 200, 600, 800 y 1200). Estas muestras procesadas se examinaron con un microscopio óptico para estudiar las características microestructurales, incluido el polvo no fundido y los defectos. Posteriormente, se analizaron con un SEM de sobremesa Phenom ProX para investigar la subestructura y la morfología.
3. Resultados y discusión
3.1 Influencia del ángulo de construcción en la construcción del rodete
Las estructuras de soporte desempeñan un papel vital a la hora de disipar el calor del baño de fusión, reducir las tensiones térmicas y contrarrestar la fuerza de la pala de recubrimiento, que ejerce una presión dinámica contra el borde de ataque de la capa. La conducción del calor varía en función de la densidad relativa; es significativamente menor en las capas de polvo con densidades de empaquetamiento más bajas que en la estructura de soporte sólido. Las diferentes estructuras de soporte disipan el calor a distintos niveles; sin embargo, una mayor disipación del calor, como ocurre con los soportes en bloque, dificulta la eliminación. Los soportes sólidos/de bloque facilitan unas propiedades mecánicas y un acabado superficial superiores en las superficies que sobresalen, aunque con mayores costes de material, tiempo de impresión y postprocesado. Además de disipar el calor, las estructuras de soporte sostienen las piezas y contrarrestan las fuerzas de tracción durante el enfriamiento rápido, mitigando los riesgos de alabeo y delaminación. Un soporte insuficiente para las superficies orientadas hacia abajo provoca problemas de forma y precisión dimensional. De ahí que la selección de los parámetros de las capas de soporte y de las capas descendentes sea crucial para mitigar las tensiones internas y la delaminación. Es crucial determinar un "ángulo de construcción fiable", es decir, el ángulo mínimo que garantiza la producción de piezas sin formación de escoria ni desprendimientos.
Como se describe en la sección de métodos, se examinó el rodete en tres ángulos de construcción durante la construcción: 90°, 30° y 0°. En el caso de CI-A, se produjo un fallo significativo del rodete, atribuido a la debilidad de las estructuras de soporte elegidas antes del proceso, como se muestra en la figura 7. La combinación de soporte de bloque y soporte de árbol resultó inadecuada para soportar el peso del impulsor, lo que provocó la deformación de la estructura de soporte, especialmente notable en un ángulo de construcción de 90˚. La deformación observada puede atribuirse al importante peso ejercido por la pieza construida y el recubridor durante el proceso de impresión. El recuperador, en particular, desempeña un papel fundamental en el proceso de estratificación al esparcir el polvo por el lecho de construcción. Sin embargo, esta acción repetitiva, especialmente durante la aplicación de las capas siguientes, puede ejercer una fuerza excesiva y provocar daños, especialmente en los ángulos de 90°, donde los bordes de la pieza impresa son intrínsecamente más débiles.
En los casos de CI-B y CI-C, se observó una construcción satisfactoria del impulsor con menos defectos. La producción de un impulsor más pequeño y grande con un ángulo de construcción de 30˚ reduce notablemente los defectos y daños durante el proceso de fabricación, mostrando resultados superiores en comparación con los casos en los que el ángulo de construcción se fija en 90˚ . Este fenómeno se muestra claramente en la figura 8. No se produjeron daños debido al ángulo de construcción de 30˚, lo que redujo el peso de la pieza impresa y mejoró el rendimiento del recubridor. Con un ángulo de 30°, el recubridor entra en contacto con menos polvo a lo largo de los bordes en comparación con ángulos de 90° y 0°durante cada movimiento de esparcimiento. El éxito de la orientación de 30 grados se atribuye a varios factores clave. En primer lugar, la transición gradual en la sección transversal de los soportes a las piezas sólidas dentro de cada capa minimiza las concentraciones de tensión y los posibles defectos, lo que la distingue de orientaciones como la de 0 grados, en la que se producen cambios bruscos. En segundo lugar, la ausencia de soportes sólidos, típicamente necesarios para los voladizos en orientaciones como la de 90 grados, contribuyó significativamente al éxito de la orientación de 30 grados. Esta eliminación de soportes no sólo agilizó el proceso de impresión, sino que también mitigó los retos asociados con el postprocesado y las imperfecciones de la superficie, mejorando en última instancia la calidad de la pieza y su integridad estructural. Además, se observó que las piezas impresas con una orientación de 30 grados presentaban un peso reducido en comparación con las impresas a 90 grados. Esta reducción de peso, aunque ventajosa en diversas aplicaciones, subrayó aún más la eficacia de la orientación de 30 grados. En conjunto, estos resultados ponen de relieve las múltiples ventajas de la orientación de 30 grados en la fabricación aditiva y ofrecen valiosas ideas para optimizar las estrategias de orientación en futuras aplicaciones.
En el caso de la CI-D, cuando el impulsor cerrado es pequeño, el fallo se produjo cuando el ángulo de construcción era de 0˚ . A pesar del pequeño tamaño del CI, el fallo en este ángulo no se debió a su tamaño, sino que se atribuyó a la debilidad de la estructura de soporte, como se muestra en la figura 9. Además, el uso de una alta velocidad de exploración de 900 mm/s dio lugar a la acumulación de residuos en la superficie del impulsor, como se ilustra en la figura 9. Además, se observaron daños a lo largo del borde, causados por los ajustes de alta potencia en estas regiones.
3.2 Impacto de los parámetros de la piel inferior en la construcción del impulsor cerrado
Down-skin denota típicamente capas, que suelen ir de 1 a 4, situadas por encima de los soportes o directamente sobre el polvo. Normalmente, tres capas se identifican como piel inferior y requieren parámetros de procesamiento distintos en comparación con las capas "interiores" o "centrales". Los parámetros relacionados con la capa inferior, como la velocidad y la potencia de escaneado, se consideran críticos para la construcción de cualquier pieza mediante la tecnología de fusión de lecho de polvo por láser. Cuando la densidad de energía de la capa inferior representa sólo el 20% de la densidad de energía de la capa interior, se producen daños apreciables en la pieza. Incluso en los casos en los que no se observan daños, se manifiestan signos de quemado y defectos en la superficie del impulsor cerrado, especialmente evidentes en impulsores cerrados de mayor tamaño como el CI-A, como se muestra en la figura 7. Esto subraya la importancia de dos factores principales que contribuyen al fallo de la pieza: la inadecuación de la estructura de soporte y la insuficiente densidad de energía del revestimiento inferior, que mide 12,15 J/mm³.
A medida que disminuye el diámetro del impulsor, como en el caso de un impulsor de 100 mm de diámetro, el impacto de la piel inferior disminuye, especialmente notable en un ángulo de construcción de 30˚ . A pesar de que la densidad de energía de la piel inferior sólo representa el 20% de la densidad de energía de la piel interior, pueden observarse pequeñas quemaduras en zonas específicas de la pieza impresa, como se muestra en la figura 10. Además, al aumentar el diámetro del impulsor, la densidad de energía de la piel inferior disminuye, como en el caso de un impulsor de 100 mm de diámetro. Además, el aumento del diámetro del impulsor aumenta la probabilidad de daños en la pieza. Sin embargo, la alineación de la densidad de energía de la piel inferior con la densidad de energía de la piel interior en un ángulo de 30˚ garantiza el éxito de la impresión del impulsor sin defectos, como se muestra en la figura 10.
La densidad de energía piel abajo es un parámetro crucial en el proceso de construcción de piezas, determinado por la complejidad y el tamaño de la pieza. En las piezas más pequeñas, su impacto es menos pronunciado que en las grandes. Para conseguir piezas sin defectos, lo ideal es que la densidad de energía de la cara inferior oscile entre el 80 y el 100% de la densidad de energía de la cara interior.
3.3 Efecto de la densidad de energía volumétrica (VED) en la microestructura del impulsor
El impulsor impreso con una densidad de energía de 35 J/mm³, considerada baja, muestra una falta de fusión atribuida a la alta velocidad de barrido, lo que resulta en un tiempo insuficiente para que el láser funda el polvo, como se muestra en la Figura 11. Al aumentar la densidad de energía a 55,55 J/mm³, estos problemas de falta de fusión y falta de adhesivo disminuyen debido a la densidad de energía óptima, lo que permite que el polvo se funda correctamente, como se ilustra en la figura 12.
3.4 Influencia del VED en la dureza
Las mediciones de dureza Vickers de las muestras impresas oscilaron aproximadamente entre 226 y 233 HV. Dos muestras, caracterizadas por una densidad de energía volumétrica (VED) de 40 J/mm³, presentaron valores de dureza inferiores a 230 HV. En concreto, las muestras CI-C-1y CI-C-2, con densidades de energía de 33,33 J/mm³ y 37,037 J/mm³, respectivamente. La mayoría de las muestras se encontraban dentro del intervalo de 220 a 230 HV, como se muestra en la tabla 3. En particular, la muestra CI-C-3, con una densidad de energía de 41,66 J/mm³, presentó la mayor dureza, de 233 HV.
Los valores de dureza Vickers (HV) obtenidos eran comparables a los de las piezas de 316L fabricadas por fundición, que suelen presentar una dureza de 210 HV. Sin embargo, los valores restantes fueron superiores a este valor de referencia. Se ha observado que cuanto más porosa es una muestra, menor es su dureza, ya que la presencia de poros permite que las indentaciones penetren más profundamente, lo que da lugar a indentaciones más grandes y, en consecuencia, a valores de HV más bajos. En este experimento, se hicieron esfuerzos intencionados para evitar los poros superficiales durante cada indentación, lo que dio como resultado una correlación mínima entre la dureza y la porosidad superficial.
3.5 Rugosidad de la superficie
La rugosidad de la superficie es un parámetro importante en la fusión de lecho de polvo por láser, en la que influye la densidad de energía. El aumento de la densidad de energía conduce normalmente a una reducción de la rugosidad media de la pieza. Esta reducción se produce porque una mayor densidad de energía permite una exposición más prolongada a alta energía y baja velocidad, facilitando una mejor fusión del polvo durante el proceso. Además, la disminución de la velocidad de escaneado aumenta la densidad de energía, reduciendo en consecuencia el efecto de formación de bolas durante el procesamiento, lo que contribuye aún más a reducir la rugosidad de la superficie. Por ejemplo, en la Figura 13, la rugosidad superficial máxima se observa en 13,82 µm cuando la densidad de energía es baja. Sin embargo, al aumentar la densidad de energía a 55 J/mm3, la rugosidad superficial disminuye a 12,79 µm.
3.6 Comparación con estudios anteriores
Los resultados se compararon con la revisión bibliográfica basada en el ensayo de dureza, en particular comparándolos con Eliasu et al[35]. Cerca de las propiedades mecánicas, observamos pequeñas diferencias en el ensayo de dureza en comparación con Eliasu et al[35], con un cambio de valor de rango entre 2 y 5 HV, como se muestra en la Tabla 4. Al comparar la microestructura, se observa que la microestructura de Eliasu et al. [35] es mejor que nuestro resultado actual, lo que puede haber causado los cambios observados en la dureza, como se muestra en la figura17.
4. Conclusiones
La impresión de un impulsor cerrado mediante fusión de lecho de polvo por láser requiere consideraciones cuidadosas de los parámetros de impresión para mitigar las complejidades asociadas al proceso de impresión. Esto incluye un diseño sutil para la selección adecuada del ángulo de construcción y el uso de una densidad de energía adecuada en el lecho inferior para una fabricación satisfactoria. En este estudio, se utiliza acero inoxidable 316L para fabricar el impulsor cerrado mediante la tecnología LPBF. Para conseguir piezas impresas con éxito y mejorar la calidad general de los impulsores cerrados, debe garantizarse la combinación óptima de varios factores cruciales.
- La utilización de un impulsor pequeño y grande con un ángulo de construcción de 30˚ reduce notablemente los defectos y daños durante el proceso de fabricación, mostrando resultados superiores en comparación con los casos en los que el ángulo de construcción se establece en 90˚ .
- Alinear la densidad de energía de la piel inferior con la densidad de energía de la piel interior en un ángulo de 30˚ garantiza una impresión correcta del impulsor sin defectos.
- Cuando la densidad de energía de la piel inferior representa sólo el 20% de la densidad de energía de la piel interior, se producen daños apreciables en la pieza. Incluso en los casos en los que no se observan daños, se manifiestan signos de quemado y defectos en la superficie del impulsor cerrado, especialmente evidentes en los impulsores cerrados de mayor tamaño.
- El aumento de la densidad de energía a 55,55 J/mm3 conduce a una reducción del polvo no fundido durante el proceso.
- El aumento de la densidad de energía disminuye la rugosidad de la superficie a 12,79 µm cuando la densidad de energía es de 55 J/mm3.
- La dureza del impulsor varía entre 226 y 233 HV, alcanzando un máximo a 233 HV cuando la densidad de energía es de 41,66 J/mm3.
Referencias
[1] P. Sulzer, Physical Principles, Centrifugal Pump Handbook, 2010,pp. 1-26.
[2] J.J.M. Timothy, C. Allison, Aaron M. Rimpel, Jason C. Wilkes, Robert Pelton, Karl Wygant,
Manufacturing and Testing Experience with Direct Metal Laser Sintering for Closed Centrifugal Compressor Impellers, 43rd Turbomachinery & 30th Pump Users Symposia, Pump & Turbo 2014, Houston, TX, 2014.
[3] A.A. Scot Laney, Derrick Bauer, Evaluation of Various Methods for Manufacturing One Piece, Small Tip Opening Centrifugal Compressor Impellers, Asia Turbomachinery and Pump Symposium, Marina Bay
Sands, Singapur, 2016.
[4] Meli, E.; Rindi, A.; Ridolfi, A.; Furferi, R.; Buonamici, F.; Iurisci, G.; Corbò, S.; Cangioli, F. Design and Production of Innovative Turbomachinery Components via Topology Optimization and Additive Manufacturing
Manufacturing. Int. J. Rotating Mach. 2019, 2019, 1-12, https://doi.org/10.1155/2019/9546831.
[5] Lezama-Nicolás, R.; Rodríguez-Salvador, M.; Río-Belver, R.; Bildosola,I. Un método bibliométrico para evaluar la madurez tecnológica: el caso de la fabricación aditiva. Scientometrics 2018, 117, 1425- 1452, https://doi.org/10.1007/s11192-018-2941-1.
[6] Aota, L.S.; Bajaj, P.; Sandim, H.R.Z.; Jägle, E.A. Fusión por cama de polvo láser como herramienta de desarrollo de aleaciones: Parameter Selection for In-Situ Alloying Using Elemental Powders. Materials 2020, 13, 3922, doi:10.3390/ma13183922.
[7] Keshavarzkermani, A.; Marzbanrad, E.; Esmaeilizadeh, R.; Mahmoodkhani, Y.; Ali, U.; Enrique, P.D.; Zhou, N.Y.; Bonakdar, A.; Toyserkani, E. An investigation into the effect of process parameters on melt pool geometry, cell spacing, and grain refinement during laser powder bed fusion. Opt. Láser
Technol. 2019, 116, 83-91, https://doi.org/10.1016/j.optlastec.2019.03.012.
[8] Qu, S.; Ding, J.; Fu, J.; Fu, M.; Zhang, B.; Song, X. Procesamiento por fusión de lecho de polvo láser de alta precisión de cobre puro. Addit. Manuf. 2021, 48, https://doi.org/10.1016/j.addma.2021.102417.
[9] Huang, S.; Narayan, R.L.; Tan, J.H.K.; Sing, S.L.; Yeong, W.Y. Resolving the porosity-unmelted
durante la aleación in situ de Ti34Nb mediante fusión de lecho de polvo por láser. Acta Mater. 2020, 204, 116522, https://doi.org/10.1016/j.actamat.2020.116522.
[10] Mukherjee, T., Wei, H.L., De, A. y DebRoy, T., 2018. Heat and fluid flow in additive manufacturing- Part II: Powder bed fusion of stainless steel, and titanium, nickel and aluminum base alloys.
Computational Materials Science, 150,pp.369-380.
[11] Aota, L.S.; Bajaj, P.; Sandim, H.R.Z.; Jägle, E.A. Laser Powder-Bed Fusion as an Alloy Development Tool: Parameter Selection for In-Situ Alloying Using Elemental Powders. Materials 2020, 13, 3922, doi:10.3390/ma13183922.
[12] Fernández, S.; Jiménez, M.; Porras, J.; Romero, L.; Espinosa, M.M.; Domínguez, M. Additive
Fabricación Aditiva y Rendimiento de Impulsores Funcionales de Bombas Hidráulicas en Tecnología de Modelado por Deposición Fundida. J. Mech. Des. 2015, 138, 024501, https://doi.org/10.1115/1.4032089.
[13] Ponticelli, G.S.; Tagliaferri, F.; Venettacci, S.; Horn, M.; Giannini, O.; Guarino, S. Re-Engineering of an Impeller for Submersible Electric Pump to Be Produced by Selective Laser Melting. Appl. Sci. 2021, 11, 7375, https://doi.org/10.3390/app11167375.
[14] Mikula, J.; Ahluwalia, R.; Laskowski, R.; Wang, K.; Vastola, G.; Zhang, Y.-W. Modelling the influence of process parameters on precipitate formation in powder-bed fusion additive manufacturing of
IN718. Mater. Des. 2021, 207, 109851, https://doi.org/10.1016/j.matdes.2021.109851.
[15] O'brien, J.; Montgomery, S.; Yaghi, A.; Afazov, S. Process chain simulation of laser powder bed fusion including heat treatment and surface hardening. CIRP J. Manuf. Sci. Technol. 2021, 32, 266-276,
https://doi.org/10.1016/j.cirpj.2021.01.006.
[16] Yavari, R.; Williams, R.; Riensche, A.; Hooper, P.A.; Cole, K.D.; Jacquemetton, L.; Halliday, H.(.; Rao, P.K. Thermal modeling in metal additive manufacturing using graph theory - Application to laser powder bed fusion of alarge volume impeller. Addit. Manuf. 2021, 41, 101956,
https://doi.org/10.1016/j.addma.2021.101956.
[17] Tupac-Yupanqui, H.; Armani, A. Additive Manufacturing of Functional Inconel 718 Parts from Recycled Materials. J. Mater. Eng. Perform. 2021, 30, 1177-1187, https://doi.org/10.1007/s11665-020-05402-8.
[18] Kladovasilakis, N.; Kontodina, T.; Charalampous, P.; Kostavelis, I.; Tzetzis, D.; Tzovaras, D. A Case Study on 3D Scanning, Digital Reparation and Rapid Metal Additive Manufacturing of a Centrifugal Impeller. En Proceedings of the 24th Innovative Manufacturing Engineering and Energy International Conference (IManEE), Atenas, Grecia, 14-15 de diciembre de 2020, https://doi.org/10.1088/1757-
899x/1037/1/012018.
[19] Tian, Y.; Ren, H.; He, J.; Zha, X.; Lin, K.; Zhou, M.; Xiong, Y. Surface roughness improvement of Ti- 6Al-4V alloy overhang structures via process optimization for laser-powder bed fusion. J. Manuf.
Process. 2024, 110, 434-446, https://doi.org/10.1016/j.jmapro.2024.01.008.
[20] Guo, J.; Wang, Y.; Wang, Y.; Peng, S.; Wang, F. Simulation Study on the Energy Utilization Efficiency of a Turbine Impeller Based on a Selective Laser Melting Process. Appl. Sci. 2023, 13, 10657,
https://doi.org/10.3390/app131910657.
[21] Yaghi, A.; Ayvar-Soberanis, S.; Moturu, S.; Bilkhu, R.; Afazov, S. Design against distortion for additive manufacturing. Addit. Manuf. 2019, 27, 224-235, https://doi.org/10.1016/j.addma.2019.03.010.
[22] Kumar, A.; Shandiz, M.A.; Sikan, F.; Brochu, M. Propiedades microestructurales y mecánicas de un impulsor cerrado IN625 sin soporte interno fabricado mediante fusión de lecho de polvo láser (L-PBF). Mater. Sci. Eng.
A 2023, 874, https://doi.org/10.1016/j.msea.2023.145080.
[23] O.D. Ian Campbell, Kowen Joseph, Wohlers Terry, 3D Prinitng and Additive Manufacturing Global State of the Industry, Wholers Report, Wholers Associates, 2018.
[24] Herzog, D.; Asami, K.; Scholl, C.; Ohle, C.; Emmelmann, C.; Sharma, A.; Markovic, N.; Harris, A. Design guidelines for laser powder bed fusion in Inconel 718.J. Laser Appl. 2022, 34, 012015,
https://doi.org/10.2351/7.0000508.
[25] Rebaioli, L.; Fassi, I. A review on benchmark artifacts for evaluating the geometrical performance of additive manufacturing processes. Int. J. Adv. Manuf. Technol. 2017, 93, 2571-2598,
https://doi.org/10.1007/s00170-017-0570-0.
[26] Yang, S.; Tang, Y.; Zhao, Y.F. Un nuevo método de consolidación de piezas para adoptar la libertad de diseño de la
additive manufacturing. J. Manuf. Process. 2015, 20, 444-449, https://doi.org/10.1016/j.jmapro.2015.06.024.
[27] Grasso, M.; Laguzza, V.; Semeraro, Q.; Colosimo, B.M. In-Process Monitoring of Selective Laser
Melting: Spatial Detection of Defects Via Image Data Analysis. J. Manuf. Sci. Eng. 2016, 139, 051001, https://doi.org/10.1115/1.4034715.
[28] Li, J.; Cao, L.; Xu, J.; Wang, S.; Zhou, Q. Clasificación inteligente de la porosidad in situ de la fusión selectiva por láser basada en la monitorización coaxial y el procesamiento de imágenes. Medición 2021, 187, 110232,
https://doi.org/10.1016/j.measurement.2021.110232.
[29] Leung, C.L.A.; Marussi, S.; Atwood, R.C.; Towrie, M.; Withers, P.J.; Lee, P.D. In situ X-ray imaging of
in situ X-ray imaging of defect and molten pool dynamics in laser additive manufacturing. Nat. Commun. 2018, 9, 1-9, https://doi.org/10.1038/s41467-018-03734-7.
[30] Cacace, S.; Pagani, L.; Colosimo, B.M.; Semeraro, Q. El efecto de la densidad de energía y la estructura de porosidad
on tensile properties of 316L stainless steel produced by laser powder bed fusion. Prog. Addit. Manuf. 2022, 7, 1053-1070, https://doi.org/10.1007/s40964-022-00281-y.
[31] Sun, Z.J.; Tan, X.P.; Tor, S.B.; Yeong, W.Y. Selective laser melting of stainless steel 316L with low porosity and high build rates
porosity and high build rates. Mater. Des. 2016, 104, 197-204, https://doi.org/10.1016/j.matdes.2016.05.035.
[32] Clijsters S, Craeghs T, Buls S, Kempen K, Kruth JP (2014) Control de calidad in situ del proceso de fusión selectiva por láser mediante un sistema de monitorización del baño de fusión de alta velocidad y en tiempo real. Int J Adv Manuf Technol. https:// doi. org/ 10. 1007/ s00170-014-6214-8
[33] Lippolis, V., Irurhe, O., Porricelli, A. C. R., Cortese, M., Schena, R., Imafidon, T., et al. (2017). Coocurrencia natural de aflatoxinas y ocratoxina A en jengibre (Zingiber officinale) de Nigeria. Food control 73, 1061-1067. https://doi.org/10.1016/j. foodcont.2016.10.026
[34] Gu, D.; Shen, Y. Balling phenomena in direct laser sintering of stainless steel powder: Mecanismos metalúrgicos y métodos de control. Mater. Des. 2009, 30, 2903-2910,
https://doi.org/10.1016/j.matdes.2009.01.013.
[35] Eliasu, A.; Czekanski, A.; Boakye-Yiadom, S. Effect of laser powder bed fusion parameters on the microstructural evolution and hard of 316L stainless steel
microstructural evolution and hardness of 316L stainless steel. Int. J. Adv. Manuf. Technol. 2021, 113, 2651-2669, https://doi.org/10.1007/s00170-021-06818-9.