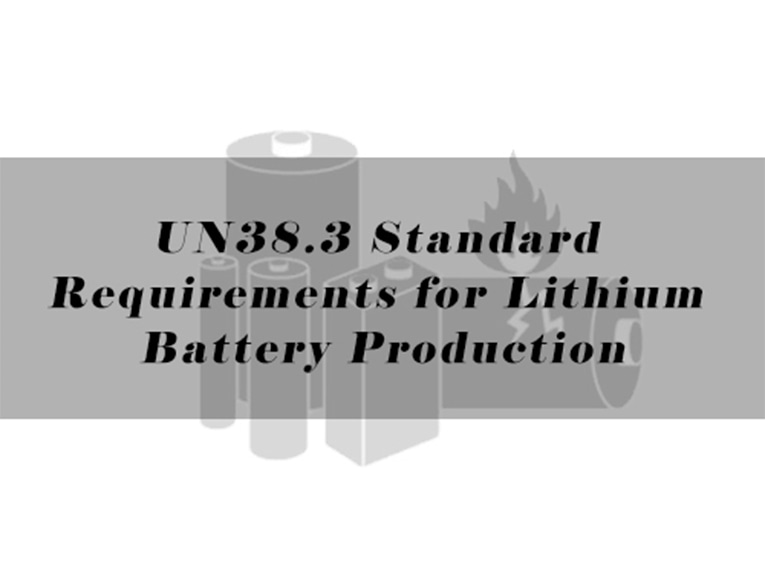
Ver traducción automática
Esta es una traducción automática. Para ver el texto original en inglés haga clic aquí
#Novedades de la industria
UN38.3 Requisitos estándar para la producción de baterías de litio
DGBell te dice que los requisitos de la norma UN38.3 para la producción de baterías de litio
UN38.3 Artículos y procedimientos de ensayo estándar
La norma UN38.3 incluye los siguientes 8 elementos de detección:
T1 de baja presión,
Ciclo de temperatura T2,
Vibración T3,
Choque T4,
Cortocircuito externo T5,
Impacto de objeto pesado T6 (núcleo de batería de litio),
Sobrecarga del T7 (batería de litio o batería de litio )
T8 descarga forzada (celdas de batería de litio).
Para las baterías de litio o los paquetes de baterías de litio, se requiere un total de 7 elementos de pruebas T1 → T5, T6 y T7. Sin embargo, para las celdas de batería de litio, se requieren las pruebas T1 → T5, T6 y T8. Entre ellas, las pruebas T6, T7 y T8 necesitan usar muestras separadas. Y la prueba T1 → T5 prueba secuencialmente la misma muestra.
Comparación de la ONU38.3 y las normas internacionales
En comparación con otros estándares internacionales de baterías de litio, las condiciones de ciclo de temperatura especificadas en el estándar UN38.3 son más exigentes y prolongadas. Otros estándares internacionales utilizan generalmente muestras separadas para las pruebas. Sin embargo, la prueba T1 → T5 en el estándar UN3813 prueba la misma muestra en secuencia. La prueba anterior puede tener un impacto negativo en la siguiente prueba, resultando en la no aprobación de la prueba. Si la batería de litio presentada para su inspección es probada para T1 → T5 en la norma UN 38.3, habrá un elemento no calificado. Las empresas necesitan volver a probar la norma UN 3813 después de la mejora del proceso, lo que extenderá enormemente el ciclo de pruebas.
Se puede saber por la Tabla 1 que, comparado con la norma internacional IEC62133, el tiempo de exposición a altas y bajas temperaturas del elemento de ciclo de temperatura en la norma UN3813 es de hasta 6 horas, y la temperatura de la prueba de baja temperatura es de -40 ± 2 ° C. Es más fácil hacer que los materiales internos de la célula de la batería se descompongan y generen gas. En caso de problemas en el proceso de producción, cuando el gas generado durante el choque de temperatura alcanza una cierta presión, es probable que el gas se escape del punto débil de la caja de la batería o del sello interno, lo que da lugar a fenómenos de baja calidad como la fuga de gas y la fuga de líquido.
Comparación de las normas UN38.3 y IEC62133
Norma del proyecto Método de detección Criterios de aceptación Diferencias entre las normas
Ciclo de temperatura UN38.3 Estándar Almacenar a 75 ± 2 ℃ durante al menos 6 h, y luego a la temperatura de prueba-40 ± 2 ℃ durante al menos 6 h. El máximo intervalo de tiempo entre dos temperaturas extremas de prueba es de 30 min. Este proceso debe repetirse 10 veces. Todas las células de prueba y los paquetes de baterías se almacenaron a una temperatura ambiente de 20 ± 5 ℃ durante 24 h. No hubo pérdida de masa, ni fugas, ni escapes, ni desintegración, ni grietas, ni combustión. Y el voltaje en circuito abierto de cada celda o batería de prueba totalmente cargada después de la prueba no es menor del 90% del voltaje antes de la prueba.
El estándar UN38.3 tiene una temperatura de prueba más baja. Y el tiempo de exposición de alta y baja temperatura es más largo.
Norma 1 del IEC62133. Coloque la celda individual o el paquete de baterías a una temperatura ambiente de 75 ° C ± 2 ° C para 4H
2. Reducir la temperatura ambiente a 20 ℃ ± 5 ℃ en 30 minutos, y mantenerla al menos 2H
3. Reducir la temperatura ambiente a -20 ℃ ± 2 ℃ en 30 minutos, y mantener 4H
4. Aumentar la temperatura ambiente a 20 ℃ ± 5 ℃ dentro de 30min, y mantenerla por lo menos 2h
5. Repita los pasos anteriores durante 4 ciclos.
6. Después del 5º ciclo, almacene e inspeccione la batería durante un período de recuperación de al menos 24H.
No hay fuego, no hay explosión, no hay fugas
Análisis de los resultados y causas de la prueba estándar UN3813
Primer caso
En el estándar UN3813, las baterías de litio probadas en el proyecto de ciclo de temperatura están completamente cargadas (100% SOC). Por lo tanto, cuando se someten a un choque de temperatura a largo plazo, pueden producirse reacciones secundarias relativamente graves dentro de la batería, generando una gran cantidad de gas. Si hay un problema con el proceso de fabricación de la batería, cuando se acumula una cierta cantidad de presión de aire, el gas y el electrolito pueden filtrarse por el hueco en la caja o el lugar donde se suelda.
Los problemas en el proceso de fabricación pueden tener las siguientes condiciones:
La soldadura de la caja de la batería y la tapa no es firme y no está sellada;
Faltan soldaduras, falsas soldaduras y grietas, y las soldaduras tienen grietas, rajaduras, etc.;
Cuando la bola de acero está sellada, el tamaño de la bola de acero es inadecuado, y el material de la bola de acero es diferente al del capuchón;
El polo positivo del casquillo no está bien remachado, y hay un hueco;
La elasticidad de la junta aislante no es adecuada, no es resistente a la corrosión, y es fácil de envejecer.
Los problemas como la pérdida de masa, las fugas y los escapes durante el ciclo de temperatura estándar de la norma UN38.3 están relacionados principalmente con el proceso de fabricación. La anatomía de la pila con fugas reveló que la pila fue sometida a una fuerza desigual durante el montaje, lo que provocó que la placa aislante interna de la pila se deformara, causando que la pila se fugara por la placa aislante.
Segundo caso
Además, la prueba también encontró que algunas baterías de litio no tienen pérdida de masa, ni fugas, ni escapes, ni desintegración, ni grietas, ni combustión después de la prueba del ciclo de temperatura. Sin embargo, debido a la reacción química entre los materiales activos de los electrodos positivo y negativo y el electrolito dentro de la batería durante el choque de temperatura, se generó una cierta cantidad de gas, lo que provocó un fenómeno de abultamiento durante la prueba.
Sin embargo, la batería de litio hinchada es más difícil de pasar la prueba de vibración durante la siguiente prueba de alta aceleración y vibración de larga duración. Es probable que la batería produzca fugas y escapes de gas, lo que provoca una pérdida excesiva de calidad y, en última instancia, el fracaso de la prueba de vibración. Para ello, los fabricantes de baterías de litio deben estar en la etapa de investigación y desarrollo, además de mejorar continuamente el rendimiento eléctrico, pero también deben tener muy en cuenta el impacto adverso del choque térmico en los materiales de la batería de litio.
Comenzando con los materiales de la batería de litio, se investigó la estabilidad de cada material químico a la temperatura de prueba especificada en el ciclo de temperatura de 75 ℃,-40 ℃, y los puntos de transición entre 75 ℃ y 40 ℃. Averiguar qué materiales son susceptibles de generar gas a la temperatura de prueba. A través de un gran número de experimentos para mejorar el proceso de estos materiales, o para encontrar otros materiales alternativos, para buscar un mejor equilibrio entre el rendimiento eléctrico y el rendimiento de seguridad de las baterías de litio.
Tercer caso
En otro caso, la célula de litio que se hinchó durante el ciclo de temperatura pasó las pruebas de vibración y choque posteriores. Sin embargo, la gran cantidad de gas generado internamente durante el ciclo de temperatura afecta negativamente a las piezas de soldadura alrededor del armazón. El choque de la presión del gas causa directamente que la fuerza de la soldadura se debilite en algunas zonas. En la prueba de cortocircuito externo después de la prueba de impacto, la batería monocelular de litio se calentó rápidamente, y se siguió generando una gran cantidad de gas en el interior de la carcasa. Cuando la presión interna de la carcasa se eleva hasta un cierto valor, el gas se libera de la zona en la que la resistencia de la soldadura se debilita, causando la ruptura de la carcasa. Como resultado, la prueba de cortocircuito externo no puede ser superada.
En la norma UN38.3 se utilizan las siguientes cámaras de prueba:
Probador de aplastamiento de baterías de servoordenadores
Sistema de prueba de vibración
Sistema de prueba de choque
Probador de penetración de clavos por aplastamiento de batería
Cámara de pruebas de simulación de altitud
Probador de impacto pesado
Cámara de prueba de cortocircuito de la batería de control de temperatura
Cámara de pruebas de aplastamiento de baterías
Cámara de pruebas de ciclos de temperatura