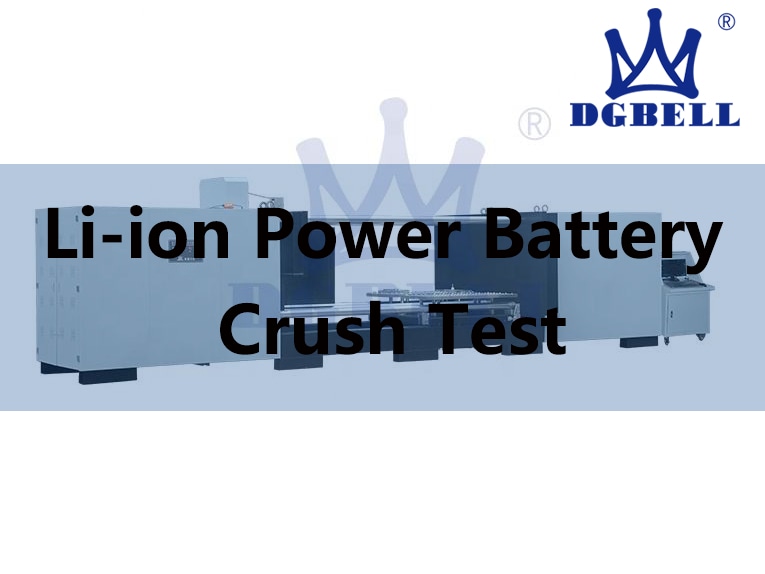
Ver traducción automática
Esta es una traducción automática. Para ver el texto original en inglés haga clic aquí
#Novedades de la industria
Prueba de aplastamiento de baterías de iones de litio - Parte 1
Prueba de aplastamiento de baterías de iones de litio - Parte 1
Guiados y apoyados por políticas, los vehículos eléctricos han entrado en un periodo de rápido desarrollo. El gobierno y los principales fabricantes de motores han formulado los correspondientes planes de desarrollo para los vehículos eléctricos. En el futuro, los vehículos eléctricos sustituirán gradualmente a los vehículos de combustible tradicionales. Sin embargo, tras una serie de colisiones de vehículos eléctricos, se han vuelto a producir incendios e incluso explosiones, lo que ha hecho que la gente se centre en la seguridad de los vehículos eléctricos. El vehículo eléctrico utiliza principalmente la batería de alimentación como fuente de energía, lo que conlleva una serie de problemas como el paquete de baterías de alimentación, el mazo de cables de alta y baja tensión y la protección del extremo de carga. Sin embargo, debido a las características de alto voltaje integrado y alta energía eléctrica, la disposición del paquete de baterías de potencia en el vehículo y la protección contra colisiones necesitan ser enfocadas.
Las leyes y normativas existentes establecen las normas de detección correspondientes para el abuso mecánico de los paquetes de baterías. Sin embargo, en las condiciones reales de la carretera, las formas de los accidentes automovilísticos son diferentes, y existe el riesgo de que los paquetes de baterías se aplasten tras la colisión de los vehículos, provocando incendios y explosiones. Por lo tanto, es necesario estudiar la seguridad en caso de colisión de las baterías eléctricas.
Algunos estudiosos han estudiado la seguridad de las baterías a partir de los componentes utilizados en las baterías, como los materiales de los electrodos, los separadores y los componentes del electrolito. También hay una serie de estudios experimentales sobre la batería de potencia, como la indentación, la flexión en tres puntos, la acupuntura y las pruebas de caída de peso, para explorar la respuesta mecánica de la batería de potencia bajo carga. También se lleva a cabo el análisis de simulación de la estructura de la batería y el comportamiento en caso de colisión de los vehículos de nueva energía, con el fin de proporcionar orientación para el diseño de la seguridad estructural de los vehículos con baterías de potencia.
En este trabajo, se toma como objeto de investigación un determinado tipo de batería de iones de litio, y se lleva a cabo la prueba de extrusión en diferentes direcciones de la celda. Mediante la recopilación de datos de presión de extrusión, temperatura y tensión, se determina la dirección de la célula que presenta una menor resistencia a la extrusión. A continuación, se determina la tolerancia al daño por extrusión de la célula mediante el análisis de diferentes condiciones de carga. En segundo lugar, se analiza la capacidad antiextrusión de los módulos en diferentes direcciones.
1.Fuga térmica de la batería de potencia
Tomando como ejemplo la batería de potencia de iones de litio, su principal mecanismo de funcionamiento implica la delitiación y la inserción de litio de los materiales del cátodo y el ánodo, así como la transmisión y difusión de iones de litio en el electrolito (masa) y los materiales del diafragma. La mayoría de los problemas de seguridad de las baterías eléctricas están directamente relacionados con la composición del material de la batería. Debido al abuso mecánico, como el sobrecalentamiento de la batería, la sobrecarga, la descarga, el impacto, la extrusión, etc., se producirán reacciones químicas entre los materiales internos de la batería, lo que provocará un calentamiento incontrolado y, finalmente, accidentes por incendio y explosión.
Tras un accidente de colisión, la estructura de la batería se deformará después de recibir un impacto y ser estrujada, lo que provocará el fallo de los materiales de los componentes internos, incluida la rotura del diafragma o la rotura de los materiales del cátodo y el ánodo, lo que dará lugar a un cortocircuito interno; El cortocircuito interno genera una gran cantidad de calor Joule, que conduce a la descomposición de los materiales de la batería única. Cuando la temperatura se sitúa entre 80 ℃ y 120 ℃, la interfaz de electrolito sólido (SEI) se descompone en primer lugar.
Cuando la reacción de descomposición de la membrana SEI avanza hasta cierto punto, se produce una serie de reacciones químicas posteriores. El desbordamiento térmico de la batería de iones de litio puede dividirse en las cinco etapas de reacción siguientes en función del aumento de temperatura: Reacción de descomposición de la membrana SEI, reacción del electrodo negativo y el electrolito, reacción de descomposición de la sustancia activa positiva, reacción del adhesivo y reacción de descomposición del electrolito. La reacción de generación de calor en el interior de la batería también producirá una gran cantidad de gas, y la presión en el interior de la estructura aumentará y se acumulará rápidamente; cuando la presión alcance el límite de carga de la estructura, puede producirse un incendio y una explosión. Cuando falla una sola batería, también se propagará rápidamente a las baterías adyacentes, lo que provocará el fallo del sistema de baterías y tendrá consecuencias más graves.
Cuando se produce un cortocircuito en la batería de alimentación, la tensión empieza a caer y la temperatura empieza a subir, por lo que la temperatura y la tensión pueden utilizarse como base de juicio para el fallo de la batería de alimentación. Teniendo en cuenta que la temperatura después de un cortocircuito interno sólo puede transferirse a la superficie de la batería durante un cierto tiempo, y se ve muy afectada por la temperatura ambiente, en comparación con la temperatura, la tensión es un parámetro que puede juzgar con relativa rapidez y precisión el fallo por cortocircuito de la batería de alimentación. El valor crítico de fallo por extrusión de este tipo de baterías puede determinarse por el aumento de la temperatura y el inicio de la caída de tensión.
La figura 1 muestra los datos de temperatura y tensión recogidos durante el proceso de desbocamiento térmico de la célula que se exprime en la prueba. En 0~36 s, la célula se exprime hasta cierto punto, la tensión sigue estable en 4,14 V, y la temperatura de la batería es de 26,2 ℃; Durante 37-38 s, la tensión cae a 2 mV, y la temperatura de la batería aumenta a 30,5 ℃; Cuando la carga alcanza los 50 s, la tensión medida es siempre de 2 mV, y la temperatura aumenta a 131 ℃. En este momento, se observa que la célula emite una gran cantidad de humo; Durante 50~51s, la temperatura de la batería aumentó de 131 ℃ a 614 ℃, y a continuación se produjo el incendio y la explosión.
La figura 2 muestra el fenómeno del humo, el fuego y la explosión cuando el calor de extrusión de una sola pila está fuera de control en la prueba.
2.Prueba de aplastamiento de la batería
Por lo general, el pack de baterías está situado bajo el suelo del vehículo. En caso de colisión frontal o trasera, hay suficiente espacio de absorción de energía delante y detrás del vehículo, la deformación estructural del suelo es pequeña, y el pack de baterías no sufrirá daños debido a la extrusión; sin embargo, cuando el vehículo sufre un impacto lateral, el espacio de absorción de energía lateral es pequeño, y la fuerza del impacto se transmite a la viga del suelo, el canal central y otras zonas a través del umbral. El paquete de baterías de potencia es fácil de ser apretado y dañado, causando así daños a los módulos internos y al monómero. Por lo tanto, puede proporcionar una base para el diseño de disposición segura de los paquetes de baterías de potencia y el juicio de fallos en la simulación para determinar la tolerancia al daño por extrusión de las celdas individuales mediante la prueba y el estudio del daño y el fallo de las celdas y los módulos de la batería en condiciones de extrusión.