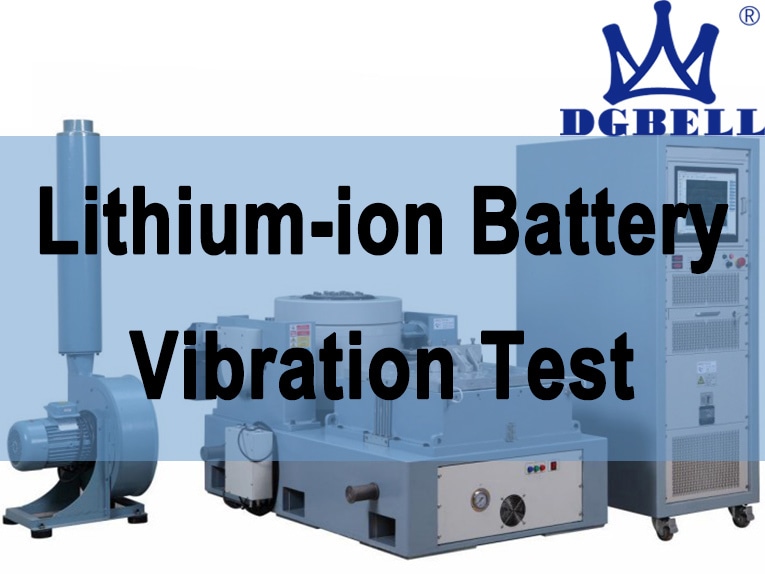
Ver traducción automática
Esta es una traducción automática. Para ver el texto original en inglés haga clic aquí
#Novedades de la industria
Prueba de vibración de baterías de iones de litio
Prueba de vibración de baterías de iones de litio
Las baterías de iones de litio plantean riesgos de seguridad tanto en la aviación civil y el transporte por carretera como en el transporte y los electrodomésticos. Con el fin de encontrar soluciones a estos problemas, se estudió el impacto de la vibración mecánica en el rendimiento y el desbordamiento térmico de las baterías de iones de litio en condiciones de baja tensión. En condiciones de baja tensión, la vibración mecánica provoca un aumento de la temperatura de fuga térmica de las baterías de iones de litio y un cambio significativo en el tiempo de aparición de las válvulas de seguridad.
Las vibraciones mecánicas de baja frecuencia y gran amplitud aceleran el proceso de cortocircuito de las baterías, mientras que las vibraciones de alta frecuencia aumentan la temperatura de ignición y el volumen de escape de las baterías de litio. Para las baterías de iones de litio 18650, la temperatura a la que salta la válvula de seguridad está entre 140~150 ℃. Cuando la válvula de seguridad salta, la intensidad de liberación de gas es relativamente alta, y la señal de gas puede ser una variable clave para la advertencia de seguridad de la batería de litio. Después de una vibración de bajo voltaje, la capacidad de descarga de las baterías de iones de litio es menor que la de la batería original, y la velocidad de descarga es más rápida que la de la batería original
1 Tipo de fallo de la batería de iones de litio
Como "corazón" de un coche, las baterías de iones de litio determinan la distancia recorrida por el coche. El sistema de baterías de iones de litio consta de cuatro componentes principales: módulos de baterías (monoceldas en serie y en paralelo), sistema de gestión de baterías (BMS), sistema de gestión térmica y componentes eléctricos y mecánicos. La función principal del BMS es controlar el voltaje, la corriente y la temperatura de la batería en tiempo real a través de sensores de concha, actuadores, chips de control principal, etc. Sin embargo, debido al envejecimiento y deterioro internos de cada batería individual del paquete de baterías, así como a la corrosión del circuito durante el proceso de agrupación de baterías, un funcionamiento inadecuado durante el uso puede provocar factores externos anormales, como sobrecargas y descargas. El efecto combinado de estos factores internos y externos provoca fallos internos y externos de la batería. Los fallos internos de las baterías de iones de litio pueden clasificarse en tipos como sobrecarga, sobredescarga, cortocircuito interno y embalamiento térmico.
Los fallos internos están causados por el mal funcionamiento del BMS y del propio sensor, lo que impide que éste funcione correctamente. Por otro lado, están causados por reacciones electroquímicas y cortocircuitos internos en la estructura interna de la batería, que dan lugar al fenómeno de dendritas de litio. Sin embargo, el peligro de los fallos externos en las baterías de iones de litio suele ser mayor que el de los fallos internos. Los fallos externos pueden desencadenar una reacción en cadena de fallos internos, provocando en última instancia un calentamiento incontrolado. Los fallos en los sensores suelen ser los más fáciles de pasar por alto, pero pueden acarrear graves consecuencias.
Los BMS se basan en sensores para lograr funciones como el control equilibrado, el diagnóstico de fallos y la estimación del estado de carga (SOC). Si el sensor experimenta desviaciones, deriva o deja de funcionar, no puede obtener datos en tiempo real ni emitir juicios precisos y razonables sobre el estado actual de la batería. Esto no sólo puede reducir el rendimiento, sino también provocar importantes accidentes de seguridad. Sin embargo, debido a la gran ocultación de los sensores, el diagnóstico es difícil, lo que constituye también el foco y la dificultad de la investigación actual sobre sensores.
Los BMS gestionan paquetes de baterías compuestos por cientos o incluso miles de baterías individuales. Debido a las características similares de los fallos de las celdas de las baterías, los fallos de los sensores y los fallos de los conectores, así como al hecho de que muchos fallos son esencialmente pequeños y están muy ocultos, es difícil identificarlos rápidamente. Por ello, el BMS produce ocasionalmente errores de diagnóstico y funcionamiento. Es crucial para la seguridad del automóvil detectar rápidamente y diagnosticar con precisión múltiples fallos de la batería. El proceso de diagnóstico de fallos de la batería puede dividirse a grandes rasgos en cuatro aspectos: detección de fallos, clasificación de fallos, localización de fallos y aislamiento de fallos. El procesamiento de datos de las baterías desempeña un papel fundamental en el diagnóstico de fallos de las baterías, y la eficacia de la eliminación de ruido puede verificarse eficazmente incorporando métodos matemáticos de filtrado morfológico.
2 Problemas con los métodos de diagnóstico para la medición de la tensión
(1) En aplicaciones prácticas, los sistemas de gestión de baterías sólo pueden medir la tensión en los bornes de cada batería individual del pack de baterías. Para que el valor de medición de la tensión incluya la tensión en los bornes individuales y la tensión en los conectores, es necesario añadir líneas de medición adicionales, lo que sin duda aumenta la complejidad del equipo. Si, al principio del diseño del sistema de gestión de baterías, la tensión recogida incluye la tensión en los bornes y la tensión en el conector, hará que el sistema de gestión de baterías no pueda obtener con precisión la tensión en los bornes de la batería y, por tanto, no pueda controlar y gestionar eficazmente la carga y descarga de la batería, lo que es propenso a fallos de sobrecarga y descarga
(2) Los cambios de tensión provocados por cambios en la resistencia interna de la batería son similares a los cambios de tensión durante los fallos de conexión Ambos están en el mismo orden de magnitud, por lo que los métodos de diagnóstico basados en señales de tensión también se enfrentan al reto de distinguir entre fallos de conexión y fallos con aumento de la resistencia interna de la batería.
(3) Cuando se produce un ligero aflojamiento de la conexión dentro del pack de baterías, el aumento de la resistencia de contacto es muy pequeño. Si la corriente de trabajo del pack de baterías es pequeña, un fallo de conexión de este tipo no provocará cambios significativos en la señal de tensión. Por lo tanto, es posible que el método de diagnóstico basado en la señal de tensión mencionado anteriormente no pueda detectar a tiempo un ligero aflojamiento de la conexión.
3 El impacto de la vibración
Realización de pruebas de carga y descarga a presión atmosférica de baterías sometidas a un tratamiento de vibración a baja tensión, para demostrar los cambios en el rendimiento de carga y descarga de las baterías de litio tras el transporte aéreo. Los resultados mostraron que tras el tratamiento de frecuencia de vibración a 60 Hz y 80 Hz en un entorno de baja tensión, el efecto de carga era inferior al de la batería original, y el tratamiento a 60 Hz tuvo el impacto más significativo en la capacidad de las baterías de litio;
Las demás frecuencias de vibración aceleran todas la velocidad de carga, y la variación es significativa a 120 Hz. Durante el proceso de descarga, la curva de la batería de iones de litio con tratamiento de vibración de 120 Hz presenta la mayor desviación, mientras que la curva con 200 Hz tiene la menor desviación. Las desviaciones restantes van de pequeñas a grandes, incluyendo 60 Hz, 80 Hz, 180 Hz, 160 Hz, 140 Hz y 100 Hz.
Se comprobó que no existía una correlación positiva entre la frecuencia de vibración y la situación de descarga, lo que puede indicar que los daños en la estructura causados por la vibración están relacionados con la capacidad de respuesta de la propia estructura de la batería a la frecuencia y la amplitud. Algunas frecuencias y amplitudes de vibración producen mayores daños en la estructura de las baterías de litio 18650.
De la comparación general de las curvas de carga y descarga se desprende que la capacidad de descarga de todas las baterías que han sufrido vibraciones es menor que la de la batería original, y la velocidad de descarga es más rápida que la de la batería original. Esto puede indicar que la capacidad y el rendimiento de descarga de la batería se verán dañados por la vibración mecánica.
De hecho, después de haber sido sometida a vibración mecánica, el grado de contacto entre los electrodos positivo y negativo en el electrolito de las baterías de iones de litio cambiará, dando lugar a un cambio en el área de contacto entre el electrodo y la solución electrolítica, lo que dificulta la transferencia de iones de litio al electrodo negativo durante la carga y descarga, y por lo tanto reduce la cantidad de litio incrustado en el electrodo negativo.
4 Conclusión
En este artículo se propone un método de diagnóstico de fallos en las conexiones de los paquetes de baterías de iones de litio basado en señales de vibración mecánica y se obtienen las siguientes conclusiones. El uso de diferentes láminas cerámicas piezoeléctricas para generar la excitación de vibración, medir la respuesta de vibración y extraer las características de tiempo-frecuencia de la señal de respuesta puede lograr eficazmente la clasificación de los modos de fallo de conexión de punto único y multipunto. En futuros trabajos se optimizará la disposición de las láminas cerámicas piezoeléctricas, se recogerán las señales de vibración del entorno del vehículo y se adecuará este método para el diagnóstico de fallos de conexión de los paquetes de baterías de iones de litio de los vehículos