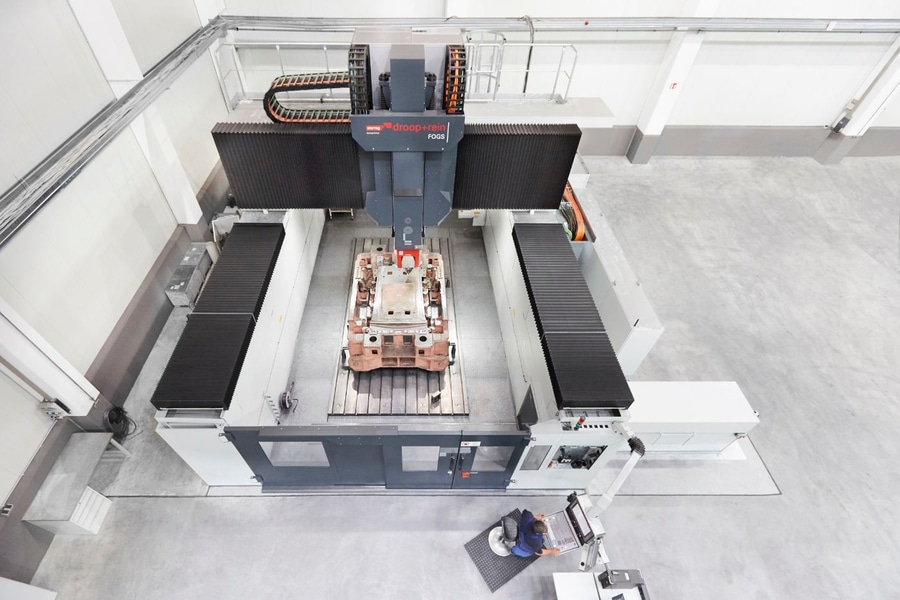
Ver traducción automática
Esta es una traducción automática. Para ver el texto original en inglés haga clic aquí
#Tendencias de productos
Actualización digital con IO-Link
Starrag Technology GmbH en Bielefeld (Alemania) es una empresa que produce máquinas herramientas y las equipa ampliamente con sensores IO-Link de ifm.
La implementación de Industria 4.0 crea una silueta digital de una planta para optimizar los procesos. La información esencial es proporcionada por muchos sensores que ya están instalados para el control de la maquinaria de todos modos. Gracias a la tecnología IO-Link, estos sensores proporcionan muchos más datos que meras señales de conmutación o valores analógicos. Starrag Technology GmbH en Bielefeld (Alemania) es una empresa que produce máquinas herramientas y las equipa ampliamente con sensores IO-Link de ifm
El centro de mecanizado de portales de la serie FOGS de Starrag Technology GmbH es una máquina que tiene estas características. Se utiliza en la ingeniería mecánica y en la industria aeronáutica y automovilística, por ejemplo, para fabricar piezas de carrocería. La máquina de la imagen se utiliza para procesar componentes de chasis (tren de aterrizaje) en la industria aeronáutica.
Estas complejas herramientas mecánicas requieren sensores para monitorear todos los medios (por ejemplo, refrigerantes y lubricantes, hidráulica, control de temperatura de la máquina). Se requieren tolerancias estrictas para las temperaturas del medio, los valores de presión y las cantidades de flujo volumétrico para garantizar que las herramientas se utilicen con una eficiencia óptima en los procesos de producción totalmente automatizados.
Sensores con interfaz digital
IO-Link es una robusta interfaz digital basada en niveles de señal de 24 V que, además de meras señales de conmutación, permite la comunicación bidireccional con el controlador a través del cable sensor regular. Los sensores transmiten valores de medición digitales e información de diagnóstico a través de IO-Link al maestro IO-Link, como un módulo IO, una pasarela o un PLC equipado con puertos IO-Link. Los sensores se conectan con conectores M12 estándar. Ya no son necesarios los cables apantallados y la correspondiente conexión a tierra.
Starrag Technology GmbH opta por los sensores de fluidos de ifm electronic. La razón: El especialista en sensores ofrece la mayor gama de productos de sensores de procesos con IO-Link.
Ajuste de los parámetros del sensor remoto
Una de las mayores ventajas del IO-Link es la posibilidad de transferir todos los datos de los parámetros necesarios a través del cable de conexión del IO-Link al sensor. Los datos de los parámetros del sensor (por ejemplo, puntos de conmutación, histéresis de conmutación, color de la pantalla) pueden transferirse desde el controlador a los sensores compatibles con IO-Link, ya sea en el momento de la instalación de los sensores o más tarde durante el funcionamiento y para ajustarlos a una situación específica. Beneficio para el cliente: Durante la fase de puesta en marcha de una máquina, los parámetros del sensor previamente proyectados pueden ser transferidos de forma rápida, sencilla y fiable al sensor. Si es necesario, por ejemplo en el caso de lotes pequeños, IO-Link permite almacenar en el sensor diferentes conjuntos de parámetros para diferentes productos por separado. Además, gracias al ajuste de parámetros basado en el controlador, la posterior optimización del proceso mediante el mantenimiento a distancia es fácil con IO-Link. En definitiva, se puede decir que IO-Link es una tecnología clave para las aplicaciones de la Industria 4.0.
Doble copia de seguridad de los datos
Además de la configuración de los parámetros del sensor basada en el controlador, IO-Link a partir de la versión 1.1 garantiza el doble almacenamiento de datos de los parámetros del sensor en el dispositivo y en el maestro IO-Link. Dietmar Wallenstein, director del departamento de construcción electrónica y puesta en marcha de Starrag Technologies, dice: "Una de las grandes ventajas de IO-Link es la copia de seguridad automatizada de los datos del sensor que se realiza en segundo plano. Cada sensor (dispositivo) envía sus conjuntos de parámetros automáticamente al maestro de IO-Link. Allí, serán reflejados y almacenados como copia de seguridad. Tan pronto como se reemplaza un sensor, los datos se intercambian automáticamente con el nuevo dispositivo. Los datos de los parámetros se transferirán entonces automáticamente del maestro de IO-Link al dispositivo IO-Link. Esto facilita enormemente la sustitución de un sensor y reduce considerablemente el tiempo de inactividad de la máquina en caso de avería. Al mismo tiempo, esto reduce la carga de trabajo del personal de servicio y mantenimiento"
Los errores de ajuste de los parámetros de los sensores son cosa del pasado. La sustitución de un sensor sólo requiere la instalación mecánica. El cliente puede reemplazarlo sin necesidad de ningún tipo de soporte. El personal de mantenimiento no necesita ser entrenado con respecto a la configuración de los parámetros del sensor, ya que se realiza automáticamente en segundo plano. Gracias a esto, los problemas técnicos pueden ser resueltos mucho más rápido y de forma mucho más eficiente. Esto ahorra costes.
Transmisión digital sin errores de los valores medidos
Hasta ahora, las señales de los sensores analógicos se digitalizan mediante convertidores A/D y se escalan en el PLC. Esto conduce a inexactitudes del valor de medición real.
El IO-Link, sin embargo, proporciona los valores medidos del sensor digitalmente al controlador. Se descartan los errores de transmisión y la conversión de las señales analógicas. Los valores de medición transmitidos digitalmente pueden ser visualizados directamente en la sala de control. El valor transferido es siempre idéntico al valor de medición. Ya no hay desviaciones entre la visualización local y el valor que el PLC obtiene de la señal analógica. Gracias a IO-Link, incluso las interferencias con la señal analógica, por ejemplo causadas por campos electromagnéticos, son cosa del pasado.
Dos valores medidos - un sensor
Los modernos sensores de proceso de ifm a menudo proporcionan más de un valor medido. Dietmar Wallenstein dice: "A menudo, un sensor procesa más de un valor físico. Además de la cantidad de flujo volumétrico o la presión, por ejemplo, también es posible leer la temperatura del medio a través de la interfaz IO-Link. En el pasado, necesitábamos dos sensores para esto" Esto ahorra dinero en hardware, cableado y montaje, ya que en lugar de dos sensores sólo se necesita uno.
Datos de diagnóstico
Además de los datos de proceso, el sensor IO-Link también puede proporcionar datos de diagnóstico sobre el estado del dispositivo. Ejemplo: El sensor de nivel detecta los depósitos críticos y los señala al controlador. Los sensores fotoeléctricos detectan si una lente está sucia y la señalan automáticamente. Los sensores de presión almacenan las pérdidas mínimas de presión y los picos máximos de presión del proceso y totalizan el número de veces que se superan o no se alcanzan los valores límite. Esta funcionalidad adicional apoya al usuario de manera decisiva cuando se trata de un mantenimiento basado en la condición. Esta información ampliada sobre la condición minimiza los costosos tiempos de inactividad y aumenta la fiabilidad del proceso.
En resumen..
Los sensores ofrecen un valor adicional considerable si están equipados con IO-Link. Dietmar Wallenstein resume las ventajas de la tecnología Starrag:
"Todo el mundo habla de la Industria 4.0, y por supuesto nosotros en Starrag no ignoramos esta megatendencia. Cuando se trata de ingeniería mecánica, pensamos en particular en la actualización de la máquina digital. Por eso optamos por el IO-Link. Gracias a las robustas interfaces de bajo coste, los sensores nos proporcionan más información sobre el proceso que luego puede ser evaluado y optimizado de forma más eficiente. Esta es una de las grandes ventajas del IO-Link y una característica del sensor que contribuye a la Industria 4.0."