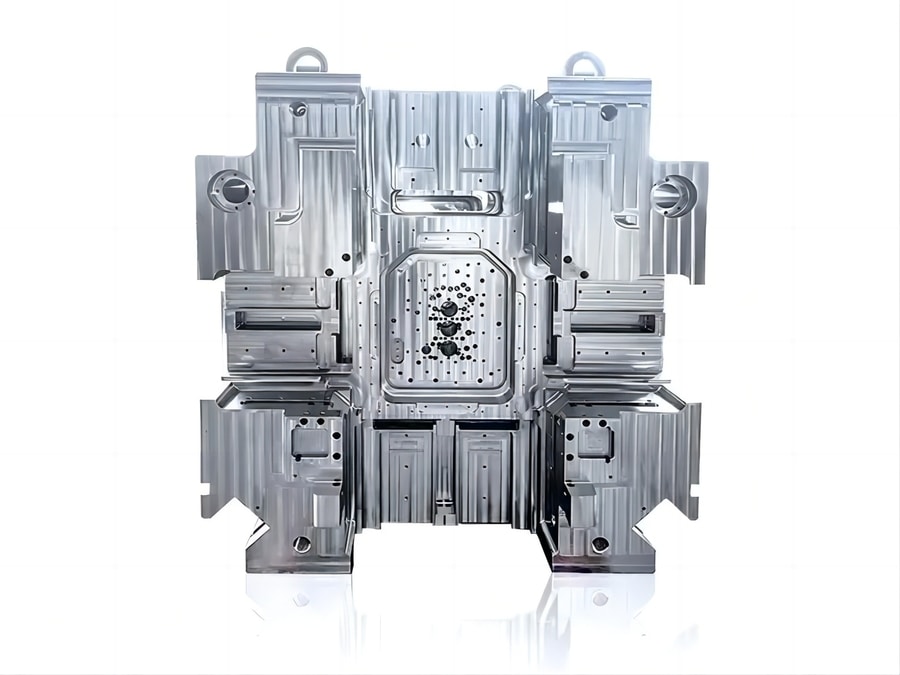
Ver traducción automática
Esta es una traducción automática. Para ver el texto original en inglés haga clic aquí
#Novedades de la industria
En La Producción De Bastidores De Aleación De Moho Para Motores De Tres Cilindros En Vehículos De Gasolina, Cómo Lograr La Estabilidad Más Adecuada Entre Tensión Y Resistencia
En La Producción De Bastidores De Aleación De Moho Para Motores De Tres Cilindros En Vehículos De Gasolina, Cómo Lograr La Estabilidad Más Adecuada Entre Tensión Y Resistencia
En la producción de bastidores de molde de aleación para motores de tres cilindros de vehículos de gasolina, ¿cómo se consigue la estabilidad más adecuada entre tensión y resistencia, y por qué son importantes esas características para el rendimiento general y la durabilidad de los componentes del motor?
Los bastidores de moldes de aleación sirven de inspiración para los enfoques de fundición de precisión que preocupan en la producción de componentes para motores de 3 cilindros en vehículos de gasolina. Lograr la estabilidad estándar de oro entre rigidez y potencia en esos bastidores de molde es un elemento vital del método de fabricación, con implicaciones de largo alcance para el rendimiento y la longevidad de los aditivos del motor.
Rigidez y fuerza:
La rigidez y la electricidad son casas mecánicas esenciales que desempeñan un papel fundamental en la capacidad de los bastidores de moldes de aleación. La rigidez se refiere de nuevo a la capacidad del tejido para soportar la deformación, mientras que la resistencia mide su potencial para hacer frente a fuerzas externas sin romperse ni ceder. En el contexto de los marcos de moho de aleación, situar la estabilidad adecuada entre estos hogares es crucial por varias razones.
Resistencia a la deformación:
La rigidez es esencial a lo largo del proceso de fundición, en el que el armazón del molde está sometido a diversos rangos de tensión y presión térmica. Si el bastidor del molde carece de suficiente presión, puede deformarse en estas condiciones, lo que provocaría imprecisiones dentro de la pieza fundida y comprometería la precisión de los componentes del motor. Mantener el equilibrio dimensional es primordial para producir aditivos que se adhieran a tolerancias estrictas y cumplan las especificaciones de diseño.
Resistencia a las fuerzas de fundición:
La resistencia es igualmente crítica, especialmente cuando se piensa en las fuerzas ejercidas en todo el sistema de fundición. Los materiales fundidos se inyectan en el molde a presiones excesivas, creando fuerzas internas de gran tamaño dentro del armazón del molde. Un cuerpo de molde con electricidad ok asegura que es capaz de resistir esas fuerzas sin sucumbir a la deformación o fallo estructural. Esto es principalmente crítico para asegurar la longevidad y fiabilidad del armazón del molde a lo largo de repetidos ciclos de fundición.
Resistencia al calor:
Además de la presión y la resistencia, los marcos de molde de aleación deben mostrar una alta resistencia al calor. La forma de fundición implica exponer los marcos de molde a temperaturas prolongadas debido a las sustancias fundidas. Las aleaciones resistentes al calor garantizan que los marcos conserven su integridad estructural y sus propiedades mecánicas incluso en situaciones térmicas excesivas. Esta característica es esencial para evitar la deformación, el reblandecimiento u otros tipos de daños térmicos que comprometerían la funcionalidad de los marcos de moho.
Mejora de la longevidad y la fiabilidad:
El equilibrio final entre tensión y energía contribuye inmediatamente a la longevidad y fiabilidad de los marcos de moho de aleación. Un marco de molde correctamente diseñado, con la combinación adecuada de estas características, puede soportar las duras situaciones del proceso de fundición durante un ciclo de vida prolongado. Esto no sólo reduce la frecuencia de las sustituciones del cuerpo del molde, sino que además minimiza el tiempo de inactividad en el método de producción, lo que se traduce en un aumento de la eficacia y la rentabilidad habituales.
En conclusión, alcanzar el equilibrio correcto entre rigidez y energía en los bastidores de moldes de aleación para motores tricilíndricos es un proceso meticuloso que requiere una cuidadosa selección de materiales y consideraciones de diseño. La interacción entre estas características es fundamental para mantener la precisión dentro del sistema de fundición, garantizar la exactitud dimensional y mejorar la durabilidad de los bastidores de moldes.