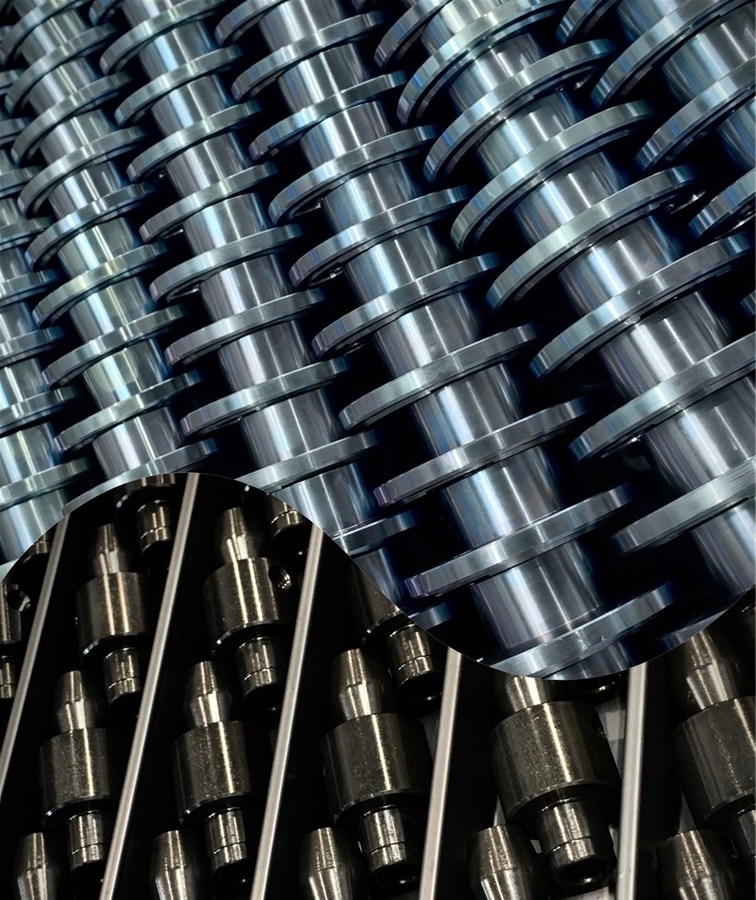
Ver traducción automática
Esta es una traducción automática. Para ver el texto original en inglés haga clic aquí
#Novedades de la industria
{{{sourceTextContent.title}}}
Las bombas de filtro OMG y la experiencia ROCCA
{{{sourceTextContent.subTitle}}}
Procesos de Zincado
{{{sourceTextContent.description}}}
El cincado representa una alternativa válida a los tratamientos galvánicos como el cromado o el niquelado.
El zinc es un metal azul-blanco, conocido desde la antigüedad tanto como elemento puro como componente de las aleaciones de Cu-Zn (latón)
Es naturalmente abundante y se produce principalmente a partir de la extracción de la blenda (ZnS)
Después del hierro, el zinc es el metal de uso más amplio y diversificado.
Su uso como capa protectora eficiente, rentable y duradera para los materiales ferrosos es una de las principales aplicaciones
El zinc tiene un excelente poder protector del hierro: para esta propiedad particular sólo el cadmio puede competir con el zinc, pero la toxicidad del Cd y la normativa vigente limitan su uso únicamente a la protección de artículos que requieren un alto rendimiento en condiciones muy estrictas (sector militar).
Por lo tanto, existen dos mecanismos de protección para la galvanización sobre el hierro:
1) Uno físico debido al efecto de barrera de la capa compacta y gruesa de zinc, que aísla el material subyacente del entorno corrosivo;
2) uno electroquímico, que actúa en áreas donde la protección física es inexistente por cualquier razón.
Para obtener una buena adhesión del depósito al sustrato, como en todos los tratamientos galvánicos, la preparación de la superficie es un aspecto muy importante a realizar.
El recubrimiento electrolítico con espesores de 5 - 12 Micrones (con un valor máximo de 30 Micrones) suele ser muy uniforme
La uniformidad de los espesores es una ventaja muy importante, especialmente para las piezas sensibles y precisas, cuyas tolerancias pueden mantenerse sin necesidad de tratamientos adicionales.
Esta característica hace que el galvanizado sea adecuado para piezas pequeñas y medianas como tornillos, pasadores, pernos...
El cincado electrolítico también se aplica para cubrir las chapas y los alambres de acero en el sector industrial. Estos tratamientos se llevan a cabo en plantas que trabajan en un ciclo continuo y con una alta productividad. El resultado es la obtención, en poco tiempo, de depósitos gruesos, uniformes y resistentes a la corrosión con un aspecto estético agradable.
Como una de las principales ventajas de este tratamiento radica en la rentabilidad del proceso, la industria mecánica comenzó a preferir este tratamiento.
El significado de la galvanización es la aplicación de un revestimiento de zinc por electrodeposición en régimen de corriente continua, a partir de una solución acuosa de sales de zinc.
Dependiendo de la geometría y las dimensiones de las piezas a tratar, se utilizan plantas estáticas o en barriles.
- Cincado estático: las piezas a galvanizar se enganchan en estructuras especiales plastificadas -llamadas "marcos", que son los medios por los que se lleva la corriente a las piezas colgadas en las unidades llamadas barras.
Esta solución garantiza la mejor calidad en términos de resistencia a la corrosión y resultados estéticos
Se puede utilizar para piezas de grandes dimensiones o también para piezas delicadas con hilos finos.
- Zincado en barril: también mediante sistemas automáticos, las piezas se cargan en un equipo de plástico (barril), que gira alrededor de su propio eje. El zinc se deposita por el paso de la electricidad a través de los agujeros del barril.
A fin de evitar enredos y madejas durante el rodaje, las piezas contenidas en el barril deben tener una geometría y un peso adecuados.
El rodamiento en sí mismo puede causar pequeñas abolladuras en las piezas, con el resultado de una menor resistencia a la corrosión.
El barril, a diferencia del armazón, no requiere mano de obra para cargar cada pieza individualmente.
Dependiendo de la temperatura de trabajo, la galvanización podría ser caliente o fría.
La creciente demanda de productos protegidos contra la corrosión ha llevado, a lo largo de los años, al desarrollo de varios procesos de galvanización.
A continuación encontrará los baños de galvanización utilizados:
Baños de galvanización con cianoalcalina:
El galvanizado con cianoalcalina fue el primer proceso utilizado por la industria para la deposición electrolítica del zinc.
A pesar de su fácil manejo, la gran flexibilidad operativa y el hecho de que no requiere una preparación de superficie muy precisa, las nuevas normativas ecológicas y la mayor sensibilidad de los operadores a las cuestiones de seguridad ambiental han hecho que este proceso se haya abandonado casi por completo
Se utiliza sólo en caso de baja concentración de zinc y cianuro, especialmente en grandes sistemas manuales para el tratamiento de piezas muy voluminosas.
Baños alcalinos sin cianuro:
Se introdujeron en el mercado más bien lentamente, debido a problemas de brillo y de pasivación de los depósitos.
Hoy en día, tras la superación de estas limitaciones, el proceso está experimentando un éxito extraordinario, especialmente en el cincado estático
Las soluciones tienen un bajo contenido de metal y están completamente libres de agente complejante, con interesantes ventajas económicas y operativas para el tratamiento y descarga de aguas residuales y de lavado.
Procesos de galvanización con ácido:
Desde su primera introducción en el mercado, los baños de galvanización con ácido han tenido una aceptación positiva debido a sus ventajas: mayor conductividad y ahorro de electricidad, mayor velocidad de deposición, utilización de productos no tóxicos y, para los baños de cloruro, un aspecto estético de los depósitos muy cerrado a los de níquel-cromo
Los principales procesos de galvanización ácida se pueden agrupar en dos categorías: los revestimientos de sulfato y de cloruro de Zn
Baños de sulfato:
Estos baños se utilizan casi exclusivamente para la galvanización de la banda y el alambre de hierro en plantas que trabajan en un ciclo continuo
Los depósitos son generalmente opacos o semibrillantes
No se utilizan aditivos brillantes; para algunas aplicaciones se utilizan aditivos de refinado de granos.
Baños de cloruro:
En 1970, tras una amplia investigación y debido a las necesidades ecológicas (la necesidad de eliminar el cianuro de los baños de galvanización electrolítica), se introdujo en el mercado el primer proceso de galvanización con ácido brillante. Los depósitos obtenidos son muy brillantes y fáciles de cromar. Se requiere una preparación muy cuidadosa. Los eventuales restos de aceites de motor, grasas y óxidos en las piezas a tratar deben ser eliminados completamente antes de la electrodeposición.
Las características y ventajas de estos procesos pueden resumirse de la siguiente manera:
- un importante poder de brillo y nivelación de los depósitos;
- excelentes rendimientos y alta velocidad de deposición, superiores a las obtenidas mediante el uso de otros electrolitos;
- menor fragilidad del hidrógeno;
- posibilidad de deposición sobre hierro fundido y aceros aleados.
En lo que respecta a las desventajas, se destacan las siguientes:
- la eventual corrosión de las partes metálicas de las plantas desprotegidas;
- necesidad de líneas de pretratamiento precisas;
- depósitos más tensos;
- distribución de espesores inferior a la obtenida con soluciones alcalinas
- interrupción del procesamiento debido a los tratamientos periódicos con peróxido de hidrógeno para la purificación del hierro.
Para saber más sobre el tema, consulte el "Manuale Trattamenti e Finiture" - 2003 - edición Tecniche Nuove.
BOMBAS DE FILTRO OMG
El tratamiento de galvanización está muy extendido entre nuestros clientes. Las bombas de filtro OMG pueden ser utilizadas tanto con soluciones ácidas como alcalinas; de hecho están diseñadas con el uso de materiales resistentes al desgaste, a la acción del tiempo y al efecto corrosivo causado por los componentes de los baños de galvanización.
Cuando la cantidad de Fe en los baños de Zn ácido es elevada, se aconseja tapar los papeles filtrantes con tierra de diatomeas y carbón, utilizando la misma bomba de filtro OMG; esta operación permite prolongar en el tiempo el uso de los papeles filtrantes y retener las suspensiones oleosas en el baño.
También señalamos que la relación correcta entre la dimensión del baño y la capacidad efectiva es la siguiente:
***Cincado estático: 1:3
***Cincado romático: al menos 1:4 (incluso mejor 1:5)
El cumplimiento de esta proporción permite:
- En un principio, reducir considerablemente la cantidad de Fe en el baño y por lo tanto mantenerla constante;
- reemplazar los papeles de filtro con mucha menos frecuencia
Un aspecto digno de mención es el de los materiales de construcción de las bombas de filtro OMG: resistentes al desgaste, a la acción del tiempo y a las soluciones ácidas y alcalinas.
El cliente que queremos presentar en el boletín, seleccionó la bomba de filtro modelo TE25 (capacidad efectiva: 25 000 l / h, capacidad: 56 000 l / h), correctamente dimensionada para sus necesidades de producción. Durante el período 2013-2020 los clientes compraron 6 máquinas modelo TE25
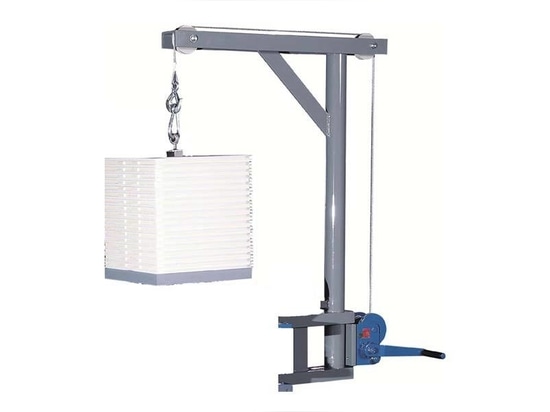
{{medias[143775].description}}