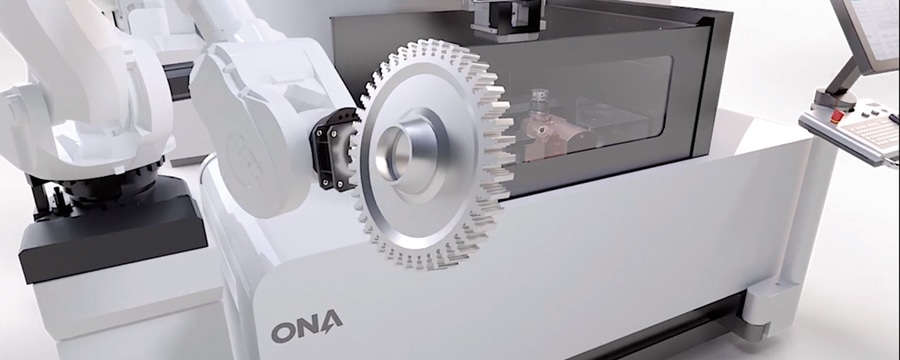
#Tendencias de productos
Máquina de electroerosión por hilo para el MECANIZADO DE FIRTREES de los discos de turbinas
Una de sus grandes virtudes es que es una máquina estándar. Se parte de una estructura base a la que se añaden módulos/accesorios en función del tipo de componente a fabricar. Ello posibilita el mecanizado de forma totalmente automatizada.
Una de sus grandes virtudes es que es una máquina estándar. Se parte de una estructura base a la que se añaden módulos/accesorios en función del tipo de componente a fabricar. Ello posibilita el mecanizado de forma totalmente automatizada.
Ser punta de lanza en investigación en electroerosión también para la industria aeronáutica. Uno de los grandes retos de ONA ha sido desarrollar tecnología EDM adaptada a proceso con objeto de convertir la electroerosión en un proceso de mecanizado competitivo y de calidad, incluso frente a procesos con más recorrido en el sector, como son el fresado o brochado. Un ejemplo de esto último es el corte de firtrees de los discos de las turbinas de aviación, aplicación principalmente se fabrica mediante brochado.
Un proyecto de éxito a destacar es el trabajo realizado en colaboración con una empresa del sector aeronáutico, en la que se trabajó en la fabricación de los firtrees para turbinas de aviación en la máquina ONA AV35 de electroerosión de corte por hilo (WEDM).
Se trata, sin duda, de uno de los proyectos más importantes y ambiciosos de ONA de los últimos tiempos. Por un lado, ha supuesto un cambio cultural en nuestra organizados, ya que diferentes departamentos han trabajado de manera estrecha en el desarrollo de la máquina. Por otro lado, gracias al esfuerzo y tecnología desarrollado la aplicación ha resultado exitosa, y se ha validad el proceso de fabricación de piezas con requisitos de exigencia muy elevada.
Actualmente existen pocas alternativas en el mercado a la AV35. Lo que distingue la máquina ONA AV35 frente a otras máquinas de electroerosión para la fabricación de firtree de los discos de turbina, es que la ONA AV35 una máquina estándar a la que se le añaden accesorios/módulos, que permite adaptarse a la fabricación de otros componentes. Es decir, no son equipos fabricados exclusivamente para un fin.
Desarrollar la máquina exigió muchas horas de investigación por parte de nuestro equipo, pero, una vez más, el esfuerzo mereció la pena. “Lo más complicado fue la coordinación entre Departamentos y también con el cliente. La máquina se ha diseñado en función de las necesidades específicas de los clientes. Los requerimientos de trazabilidad han requerido del uso de herramientas de software de última generación”, describe uno de nuestros técnicos.
El equipo AV35 conlleva importantes ventajas para las empresas, como una inversión inicial en maquinaria menor -gracias a esa adaptabilidad- y un incremento inmediato de la autonomía. Todo el proceso de mecanizado está automatizado y rigurosamente controlado para que la pieza cumpla con los requisitos marcados: se proporcionan continuamente datos y parámetros para conocer si se avanza según lo previsto y, en el caso de que haya algún error (un cambio de temperatura en el agua, etc.), se produce un aviso.
Tecnología a la altura del brochado y del fresado
Los discos son piezas rotativas críticas en una turbina de gas: alcanzan hasta las 60.000 revoluciones por minuto y deben estar preparados para resistir temperaturas y fluctuaciones de presión extremas, a la vez que tienen que ser ligeros y seguros. Resultan, por ello, esenciales tanto la calidad del material utilizado (por lo general superaleaciones con base de níquel) como el proceso de mecanizado (exigentes requisitos geométricos y de calidad superficial).
Las técnicas de mecanizado más empleadas para fabricar los firtrees de los discos de las turbinas han sido tradicionalmente las de arranque de viruta mediante contacto físico: brochado, rectificado y fresado. Siendo el brochado es el proceso quizás más conocido y empleado.
Con respecto a la electroerosión, el desarrollo de nuevos generadores ha sido el principal impulso que ha hecho que la electroerosión se haya convertido en un proceso de fabricación viable y competitivo para la fabricación de componentes del sector aeronáutico. Las principales ventajas que ha supuesto el desarrollo de los nuevos generadores EDM son: capacidad de proporcionar mucha más potencia, aumentando así la productividad, y la adaptación de la tecnología y estrategia de mecanizado para conseguir una disminución de la zona afectada térmicamente y la disminución de la capa blanca, aspectos indispensables especialmente en el sector aeronáutico.
Estos y otros avances han ido poco a poco situando a nuestra tecnología a la altura del brochado y el fresado en cuanto a la calidad en el producto final. Y a día de hoy se puede decir que, además de alcanzar las estrictas tolerancias que exigen las piezas aeronáuticas, el proceso WEDM de ONA ofrece también una mayor flexibilidad a los fabricantes de turbinas en términos de plazos y de referencias: les permite adaptarse más rápido que los procesos de mecanizado convencionales.
La máquina AV35 de ONA tiene en cuenta todos los detalles, desde la compensación de posicionamiento de la pieza, pasando por la optimización de la tecnología y terminando por la total conectividad para una perfecta trazabilidad de todo el proceso.
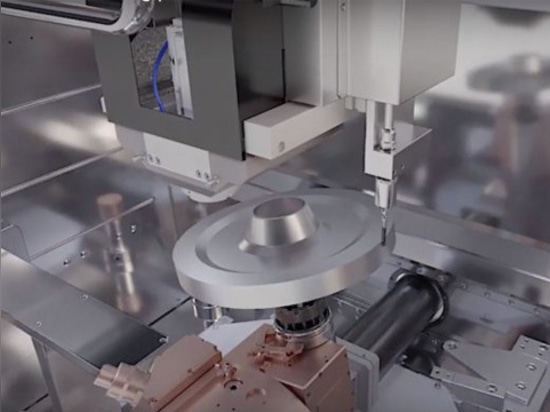
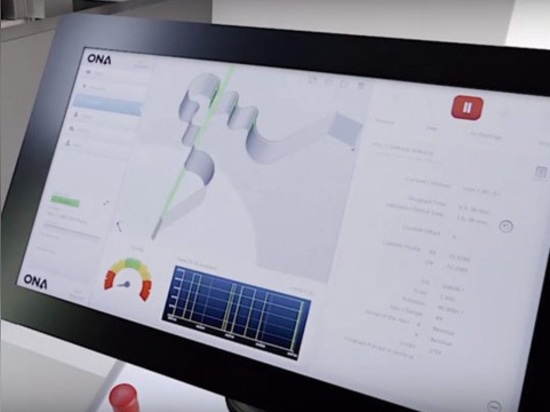
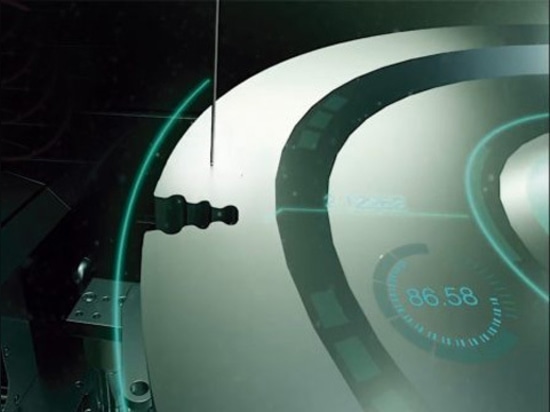
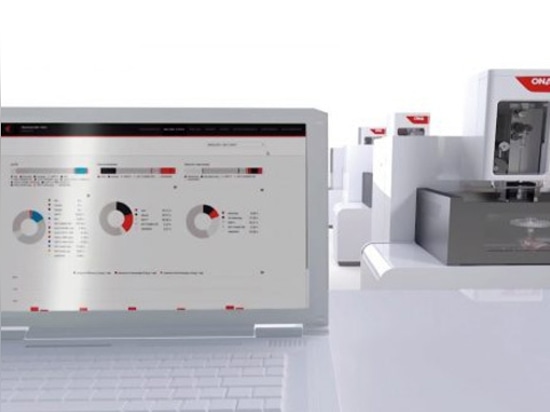
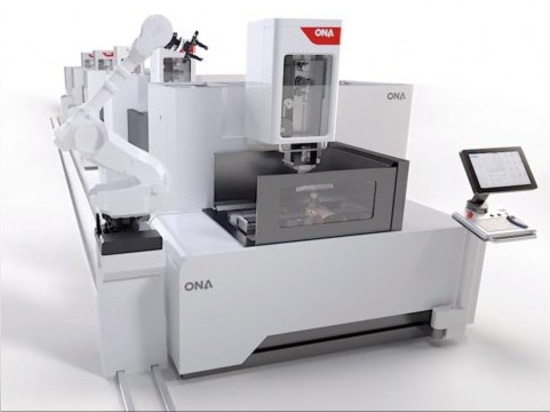