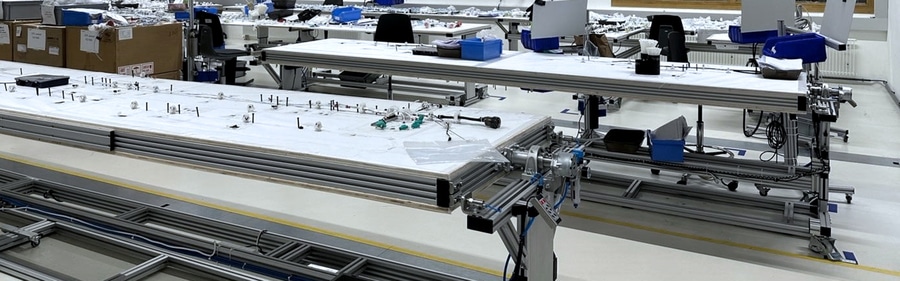
Ver traducción automática
Esta es una traducción automática. Para ver el texto original en inglés haga clic aquí
#Novedades de la industria
Tiempos de cambio cortos con mesas de montaje modulares
Tiempos de cambio cortos con mesas de montaje modulares y ergonómicas fabricadas con perfiles de aluminio
Situación inicial:
La empresa suiza Pilatus Aircraft Ltd, que opera a escala internacional, es conocida por sus aeronaves únicas en el mundo, como aviones de entrenamiento y aviones polivalentes más pequeños. Para las distintas aeronaves se necesitan diversos mazos de cables, que difieren mucho en cuanto a diseño, como longitud y forma. En función del diseño del mazo de cables, se alineaban mesas sencillas con la forma requerida y se les colocaban las placas adecuadas. Aunque este método funcionaba en principio, dificultaba el trabajo cómodo y seguro. Por un lado, uno se golpea con las patas de la mesa al trabajar y, por otro, no es posible adoptar una postura cómoda y ergonómica. Además, colocar las mesas es incómodo y lleva mucho tiempo.
El reto:
El objetivo de Pilatus era conseguir un sistema de puestos de trabajo que aumentara la ergonomía y la seguridad de los empleados y que, al mismo tiempo, fuera modular y se pudiera adaptar y ampliar con flexibilidad en cualquier momento. También debía acortarse y simplificarse el tiempo de cambio de las mesas y tableros para instalar los distintos mazos de cables. No deberían ser necesarios más de dos empleados para convertir las grandes superficies de trabajo.
Solución:
Phoenix Mecano colaboró estrechamente con KKS Ultraschall AG para desarrollar una propuesta de diseño a medida. Esta cooperación se basó en una larga colaboración y en un profundo conocimiento de las condiciones específicas de KKS Ultraschall AG. Con la ayuda de los archivos STEP proporcionados, el cliente pudo hacerse una idea detallada y realizar los ajustes necesarios antes de la producción final de la carcasa de la máquina, lo que hizo que el proceso de desarrollo fuera especialmente eficaz. La excelente comunicación y el entendimiento mutuo facilitaron enormemente la colaboración. Incluso los cambios menores se implementaron de forma rápida y eficaz, lo que favoreció todo el proceso de desarrollo. Phoenix Mecano también tuvo en cuenta requisitos especiales como la conformidad con las normas y el uso de perfiles cerrados. Tras la finalización, Phoenix Mecano organizó el transporte de la carcasa de la máquina a KKS Ultraschall AG, con entrega modular debido al tamaño de la carcasa de la máquina. Esta modularidad facilitó el montaje in situ y garantizó una integración perfecta con el sistema de grabado y limpieza. Además, Phoenix Mecano proporcionó a KKS Ultraschall AG espacio de almacenamiento para resolver cualquier problema de espacio de forma flexible y eficiente.
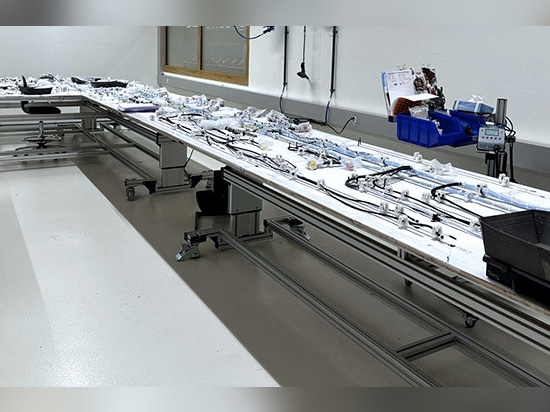