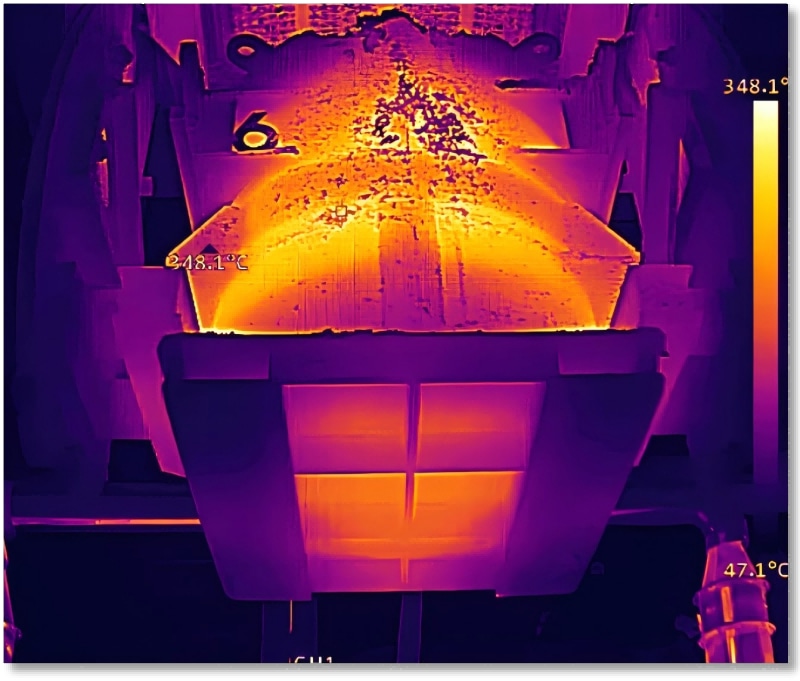
#Libros blancos
Soluciones de imágenes térmicas infrarrojas para fundición mecánica
Soluciones de imágenes térmicas infrarrojas para fundición mecánica
La fundición mecánica es una de las primeras técnicas de tratamiento térmico de metales que se dominaron en la producción moderna y se utiliza ampliamente en la fabricación de piezas y componentes para industrias como la aeroespacial/aviación, armamentística, de maquinaria, electrónica, petrolera, química, energética y del transporte. La temperatura es una variable crítica durante la fusión en la industria de la fundición; una medición y un control inadecuados pueden afectar directamente muchas características de calidad.
Limitaciones de la medición tradicional de temperatura
En la industria de la fundición, la formación de carbonilla se produce con facilidad durante la fusión. La mayoría de las soluciones de medición de temperatura disponibles se basan en puntos, lo que exige evitar las zonas oxidadas, lo que complica su implementación y genera errores de medición significativos, dificultando así la obtención de datos de temperatura precisos. Implementar la medición de temperatura sin contacto durante la fusión en la industria de la fundición es un gran reto.
Solución de imágenes térmicas: cómo abordar los límites de medición de la temperatura de fundición
El desarrollo de la tecnología de cámaras termográficas permite medir la temperatura en tiempo real durante la fusión. Una cámara termográfica es un dispositivo de imagen térmica capaz de detectar la distribución de la temperatura en la superficie de los objetos. Convierte la radiación infrarroja emitida por los objetos en imágenes visibles, mostrando así intuitivamente la distribución de la temperatura en la superficie de los objetos. Durante la fundición, la cámara termográfica puede monitorizar los cambios de temperatura de las piezas en tiempo real, lo que ayuda a los trabajadores a ajustar oportunamente los parámetros del proceso para garantizar la calidad de la fundición.
La aplicación de cámaras térmicas en el proceso de fundición se refleja principalmente en los siguientes aspectos:
Monitorización en tiempo real de la temperatura de fundición: Los trabajadores pueden usar cámaras térmicas para monitorear los cambios de temperatura de las piezas fundidas en tiempo real, lo que permite la identificación y resolución oportuna de posibles problemas, como sobrecalentamiento o sobreenfriamiento, mejorando así la calidad de la pieza fundida.
Optimización del proceso de fundición: Con base en los datos de temperatura proporcionados por las cámaras térmicas, los trabajadores pueden ajustar los parámetros del proceso de fundición, como la velocidad de vertido y la velocidad de enfriamiento, para obtener mejores resultados de fundición.
Prevención de defectos de fundición: Los trabajadores pueden utilizar cámaras térmicas para identificar posibles defectos que puedan ocurrir durante la fundición, como cavidades por contracción y grietas, lo que permite tomar medidas oportunas para su prevención o reparación.
Aplicación de la termografía industrial en la fundición mecánica
1. Monitoreo del proceso de colada continua
En el proceso de producción de colada continua de acero, el acero fundido refinado se transporta mediante una cuchara a una mesa giratoria, que gira hasta la posición de vertido designada, donde se vierte en la artesa. A continuación, el acero fundido en la artesa se distribuye uniformemente a múltiples cristalizadores a través del espacio de agua. El cristalizador, uno de los dispositivos principales de una máquina de colada continua, permite que el acero fundido se solidifique y adquiera forma rápidamente. Posteriormente, el tensor y el dispositivo de vibración de cristalización trabajan conjuntamente para extraer las palanquillas inicialmente solidificadas. Tras el enfriamiento y la agitación electromagnética, las palanquillas se cortan en losas que cumplen con los requisitos de especificación.
In procesos tradicionales, monitoreo de temperatura principalmente Se basa en operadores experimentados que observan el color de los tochos.Este método es bastante subjetivo y presenta errores mayores, lo que dificulta el cumplimiento de los requisitos de la colada continua moderna en cuanto a consistencia del producto y controlabilidad del proceso.
Para lograr un monitoreo de temperatura inteligente y basado en datos, cámaras térmicas fijas de temperatura ultraalta Se han adoptado e implementado ampliamente en posiciones críticas de "sector" de máquinas de colada continua. Pueden realizar Monitoreo en tiempo real y de alta precisión de la temperatura superficial de las palanquillas, generando imágenes térmicas dinámicas y curvas de temperatura que proporcionan soporte de datos intuitivo a los operadores, mejorando así las capacidades de control de procesos.
2. Monitoreo de materiales refractarios de cuchara
Los materiales refractarios se utilizan ampliamente en cucharas de cocción y otros dispositivos clave en plantas siderúrgicas. Pueden dañarse debido a vibraciones mecánicas, corrosión por alta temperatura, etc., lo que acorta su vida útil. Fenómenos como desprendimientos, grietas y fisuras se producen gradualmente en los materiales refractarios y, si no se detectan a tiempo, pueden provocar fugas de la fuente de calor de alta temperatura, dañando el dispositivo y el medio ambiente, y poniendo en peligro la seguridad de los trabajadores.
Para reconocer eficazmente los peligros tempranos, cámaras térmicas fijas pueden introducirse en tales circunstancias para Monitorizar en tiempo real la temperatura de dispositivos relevantes. El sistema puede capturar con precisión cambios anormales de temperatura, lo que genera una alerta inmediata cuando esta supera los umbrales establecidos. Mediante el análisis de imágenes térmicas y distribuciones de temperatura, se pueden detectar y localizar los puntos defectuosos cuando los materiales refractarios se encuentran en las primeras etapas de desprendimiento y agrietamiento.
El enfoque permite advertencia proactiva de fallas, eliminando los riesgos de seguridad antes de que ocurran. Esto garantiza la Operación segura, continua y eficiente Durante la producción en el taller, previniendo eficazmente fallas del dispositivo y accidentes de seguridad.
3. Medición de temperatura en la superficie de la cuchara
En entornos de fundición mecánica, las cucharas sirven como contenedores cruciales para transferir el hierro fundido y suelen reemplazarse cada dos semanas. Dado que Los cucharones están expuestos continuamente a condiciones de alta temperatura durante su uso.Cualquier aumento anormal de temperatura puede provocar accidentes graves que afecten la seguridad, como la rotura de la cuchara. Por lo tanto, la monitorización de la temperatura de la cuchara en tiempo real durante su vida útil no solo es una medida clave para la gestión de la seguridad, sino que también proporciona datos que respaldan la optimización del diseño estructural de la cuchara y prolongan su vida útil.
Para controlar con precisión los cucharones, cámaras térmicas fijas Por lo general, se implementan en áreas de acceso crítico en el sitio en los proyectos relacionados, lo que establece un sistema integral de monitoreo de la temperatura de la cuchara. El sistema presenta las siguientes funciones principales: Monitoreo de temperatura en tiempo real de las cucharas que pasan a través del área designada; reconocimiento del número de serie de las cucharas que pasan a través del área designada con algoritmos; y registro del número de serie de las cucharas y los datos de temperatura en las marcas de tiempo correspondientes en el backstage para el análisis general de los cambios de datos de temperatura de las cucharas.
4. Medición de la temperatura de la carcasa y el interior del horno rotatorio
El horno rotatorio es un dispositivo clave para la calcinación de pellets en el proceso de fundición. Su temperatura interna se mantiene típicamente por encima de los 1200 °C, mientras que en la zona de cocción alcanza los 1300-1400 °C. El funcionamiento a alta temperatura no solo afecta la vida útil de los materiales refractarios y los componentes estructurales, sino que también es uno de los factores clave que determinan la calidad del producto y la eficiencia de la producción. Un control inadecuado de la temperatura puede provocar accidentes de seguridad graves, como incendios o explosiones.
Por lo tanto, es particularmente crítico realizar un monitoreo en tiempo real y un diagnóstico de tendencias de las temperaturas en las paredes internas y externas del horno rotatorio. sistema de cámara térmica fija se puede implementar en Monitorizar continuamente la temperatura de la pared exterior del horno rotatorio y obtener imágenes completas de la distribución térmica.Con base en esto, se pueden detectar a tiempo aumentos anormales de temperatura y descensos del refractario localizados. Además, se puede establecer una base de datos de temperatura histórica para brindar soporte de datos para la optimización de parámetros operativos, la alerta de fallas y el mantenimiento del dispositivo, mejorando así la operación segura, estable e inteligente del horno rotatorio.
5. Monitoreo de la placa mediana en la producción de acero y laminación
En las acerías, las palanquillas de chapa mediana permanecen sin terminar antes del proceso de fabricación y laminación del acero. Solo mediante rigurosos procedimientos de calentamiento y laminación se pueden transformar en chapas de acero de calidad. Durante la producción de chapa mediana, El control de la temperatura es decisivo para la calidad de la placa media, la vida útil del molde y el ciclo de producción. Por lo tanto, se ha convertido en una medida tecnológica indispensable en las tecnologías modernas de fabricación y laminación de acero. La precisión del control de temperatura durante la fabricación y laminación de acero afecta directamente la consistencia del producto, la vida útil del laminador y la eficiencia general de la producción.
Para minimizar la diferencia de temperatura dentro del horno, mejorar la uniformidad de la temperatura de la losa, extender la vida útil del dispositivo y reducir el consumo de energía, así como las pérdidas por oxidación y quema, camaras termicas se introducen en la línea de producción para realizar mediciones de temperatura sin contacto En las placas que salen del horno. Este enfoque captura eficazmente la distribución de la temperatura en las distintas áreas de la superficie de las placas. Mediante el análisis de los datos de imágenes térmicas, es posible identificar con precisión las causas de las temperaturas desiguales para optimizar los parámetros del proceso de calentamiento y garantizar una calidad estable de la placa, lo que proporciona un sólido soporte para una fabricación y laminación de acero eficientes, ecológicas e inteligentes.
6. Monitoreo del procesamiento de placas de acero
En la línea de producción de laminado de acero de la acería, las placas deben someterse a un tratamiento de deformación plástica según la longitud, el ancho y el espesor del producto terminado. Durante el proceso, es necesario un monitoreo continuo. la planitud, las dimensiones geométricas y la curvatura de la superficie de las placas para garantizar la calidad de los productos terminados.
Actualmente, Cámaras de luz visible acopladas con ajustes de exposición Se adoptan principalmente en obra para evaluar la planitud y uniformidad de las placas. Sin embargo, debido al repetido proceso de enfriamiento por agua necesario después del laminado, suele haber una cantidad significativa de vapor de agua y vapor En el sitio, esto dificulta gravemente la captura de imágenes con luz visible, lo que dificulta la captura precisa del contorno de las placas. Mientras tanto, a medida que la temperatura de la placa disminuye gradualmente, el brillo de la imagen se reduce significativamente con parámetros de exposición fijos, lo que afecta aún más la claridad de la imagen y la precisión de detección.
En consecuencia, método tradicional de imágenes de luz visiblePresentan claras limitaciones en condiciones complejas de alta temperatura y alta humedad.Existe una necesidad urgente de introducir tecnología de percepción visual que sea más adecuada para escenarios industriales de alta temperatura para lograr un monitoreo estable y un reconocimiento inteligente del estado de la placa.
7. Medición de temperatura de moldes de fundición a presión
La fundición a presión es un proceso de fundición de precisión de metales que se caracteriza por introducir metal fundido a alta presión en una cavidad de molde con una forma compleja. Una máquina de fundición a presión es una máquina utilizada para la fundición a presión. Bajo presión, el metal fundido se inyecta en el molde para su enfriamiento y conformado, obteniendo piezas fundidas sólidas tras el embutido. Una temperatura desigual o inadecuada del molde provocará directamente Defectos del producto, deformación de la fundición por expulsión, grietas, adherencia del molde, depresiones superficiales, cavidades por contracción y burbujas calientes. Las diferencias significativas en la temperatura del molde influirán en distintos grados en el tiempo de llenado, el tiempo de enfriamiento y el tiempo de pulverización.
El sistema La cámara térmica se puede utilizar para la monitorización de temperatura sin contacto. La temperatura del molde antes y después de pulverizar el desmoldante garantiza su temperatura. Los peligros ocultos se pueden identificar comparando y analizando los datos históricos monitoreados.
8. Monitoreo PLC integrado para fundición a presión
La fabricación de motores y carrocerías de vehículos se realiza mediante fundición en caliente. Para garantizar la calidad de los componentes, es necesario controlar la temperatura del molde antes y después del proceso de fundición a presión, incluyendo la temperatura del molde antes y después de la fundición a presión y la temperatura del molde después del enfriamiento por pulverización de agua. Vinculación del dispositivo in situ y del PLC de fundición a presión darse cuenta de la monitoreo en tiempo real De la temperatura del molde y de la línea de producción de fundición a presión totalmente automatizada. Al mismo tiempo, se puede registrar la temperatura total de producción del molde.
La parte delantera está equipada con una cámara térmica en líneaLos datos de la cámara termográfica se obtienen mediante el protocolo de red. La cámara termográfica se conecta al PLC mediante el programa de backend para confirmar el estado actual antes y después de la fundición a presión. Posteriormente, se obtienen los datos de temperatura del dispositivo para su evaluación. La pantalla grande muestra la temperatura y las imágenes infrarrojas. Antes y después de la fundición a presión en los dos últimos periodos.
9. Monitoreo de temperatura de dispositivos de potencia mecánica
Dispositivos como motores, ventiladores, bombas y compresores en el campo de la potencia mecánica generalmente incluyen componentes de transmisión como cojinetes, engranajes, correas y acoplamientos, que transfieren energía mecánica mediante fricción. En ese caso, se producirá un calentamiento por fricción tras un funcionamiento prolongado. Una vez que la temperatura supera un umbral seguro, puede causar daños al dispositivo, además de desperdicio de energía y accidentes que afectan a la seguridad.
El sistema cámara térmica, ser un Herramienta de monitoreo de temperatura sin contacto, puede detectar con precisión posibles fallas. Como desalineación de rodamientos, lubricación deficiente, deslizamiento de correas y desplazamiento de poleas, sin tiempo de inactividad. Al proporcionar imágenes en tiempo real, ayuda a localizar rápidamente los puntos críticos, ofreciendo al personal de operación y mantenimiento una base intuitiva y eficaz para la toma de decisiones, reduciendo así eficazmente la fricción, mejorando la eficiencia de la transmisión y contribuyendo al ahorro de energía y la reducción de emisiones.
Además, la cámara térmica demuestra una ventaja significativas en varios procesos de seguimiento clave en comparación con otros métodos tradicionales. Monitoreo de temperatura en revistas, supera las limitaciones de no poder contactar y medir temperaturas en componentes giratorios de alta velocidad, lo que permite la identificación oportuna de riesgos de fallas causados por sobrecalentamiento de los rodamientos, evitando así interrupciones en la producción. En la detección de grietas en cojinetesPuede identificar microgrietas en la superficie que son difíciles de discernir a simple vista, lo que permite una alerta temprana. En la monitorización de fallos de aislamiento del motorPuede establecer umbrales de temperatura para alertas de alarma en tiempo real para ayudar a abordar problemas como mala disipación de calor y aislamiento anormal, previniendo accidentes de seguridad importantes.
10. Monitoreo de la temperatura de la soldadura por fricción
La soldadura por fricción es un método de soldadura común en la industria de la fundición mecánica. Actualmente, los usuarios no pueden comprender de forma intuitiva y eficaz la temperatura de los puntos de soldadura durante la soldadura, y Los trabajadores cualificados confían únicamente en su experiencia para la operación y el control.Requiere una larga experiencia por parte de los trabajadores y, además, es propenso a fluctuaciones significativas de temperatura, lo que no garantiza la calidad de la soldadura. Por lo tanto, es fundamental observar intuitivamente la información de temperatura del punto de soldadura y comprenderla de manera oportuna y precisa para garantizar la calidad de la soldadura.
Monitorizando remotamente la temperatura del punto de soldadura en tiempo real con un cámara térmica sin contactoSe logra un control preciso de la temperatura, lo que resulta en una calidad de soldadura óptima y una mayor eficiencia de producción. Este método evita las limitaciones de las técnicas de medición tradicionales.
11. Monitoreo de temperatura de revestimientos de acero al cromo-molibdeno para enfriamiento
Los revestimientos de acero al cromo-molibdeno son materias primas clave de uso común en la industria de la fundición mecánica. Se utilizan ampliamente como refuerzo entre el revestimiento resistente al desgaste y el cilindro del molino de bolas para soportar el cono, proteger el dispositivo y amortiguar el impacto del mineral triturado. Con un diseño eficaz, estos revestimientos pueden reducir la vibración del dispositivo y prolongar su vida útil. Tras ser descargados del horno, los revestimientos se colocan en una zona de enfriamiento para su tratamiento. La medición manual tradicional de temperatura y enfriamiento por aspersión están ineficiente y requiere mucha mano de obraAdemás, la exposición prolongada a un entorno de alta temperatura puede ser perjudicial para la salud de los operadores.
En comparación con los dispositivos tradicionales de medición fija de temperatura puntual, camaras termicas puede proporcionar Imágenes de distribución de temperatura visual más intuitivas y ayudan a los operadores a monitorear el estado de la temperatura de los revestimientos en tiempo real. Pueden realizar monitoreo de temperatura sin contacto, lo que permite un seguimiento completo de los cambios de temperatura en todas las áreas de la superficie del revestimiento. En ese caso, se pueden identificar a tiempo posibles problemas de sobrecalentamiento o enfriamiento irregular, y se puede optimizar el proceso de enfriamiento para aumentar la eficiencia, reducir la mano de obra y garantizar la seguridad de los operadores.
12. Monitoreo de temperatura de impresión 3D
La tecnología de impresión 3D, también llamada fabricación aditiva, es un nuevo tipo de proceso de fundición mecánica. Se trata de una tecnología que, a partir de archivos de modelos digitales, emplea materiales adherentes como metal en polvo o plástico y construye objetos mediante impresión capa a capa. Control de temperatura Durante el proceso de impresión es crucial para las propiedades de unión, el rendimiento de apilamiento y la precisión de impresión del materialSi la temperatura de impresión es demasiado baja, la viscosidad del material aumentará y la velocidad de extrusión se ralentizará. Si la temperatura es demasiado alta, el material tiende a licuarse, la viscosidad disminuye, la fluidez aumenta y la velocidad de extrusión es demasiado rápida, lo que impide la formación de filamentos con un control preciso. Por lo tanto, es fundamental controlar la temperatura con precisión durante la impresión 3D.
Durante el proceso, La cámara térmica, al ser una herramienta de medición de temperatura sin contacto, puede realizar un monitoreo de temperatura preciso y en tiempo real.Esto ayuda a garantizar una temperatura estable y precisa durante todo el proceso de impresión en la industria de la impresión 3D. La cámara térmica puede monitorizar exhaustivamente los cambios de temperatura en componentes críticos como el cabezal y la cama de impresión, previniendo así defectos de impresión causados por fluctuaciones de temperatura y mejorando la calidad y la eficiencia del producto, contribuyendo así al desarrollo inteligente y refinado de la tecnología de impresión 3D.
13. Monitoreo de seguridad de tornos de procesamiento
Dispositivos como cortadoras y rodillos a menudo requieren que los operadores alimenten manualmente los componentes. Durante el procesamiento, las manos de los operadores suelen estar cerca del área de procesamiento, y las máquinas no pueden determinar automáticamente cuándo arrancar o detenerse. Incluso una pequeña desviación en la alimentación puede provocar fácilmente lesiones a los operadores.
Para abordar este asunto, Generalmente se instalaban varios conjuntos de dispositivos raster en el sitio. Cuando un objeto entra en el área de detección del ráster, los dispositivos emisor y receptor lo identifican y emiten automáticamente una señal de control para cortar la alimentación del dispositivo. Sin embargo, estos dispositivos no pueden distinguir entre piezas y componentes, ni entre las partes del cuerpo del operador, lo que provoca su activación frecuente cada vez que se alimenta. hace que el dispositivo se detenga con frecuencia, afectando la eficiencia de la producción y sin proteger eficazmente a los operadores.
Para optimizar la solución existente, camaras termicas, gracias a su principio de funcionamiento, Puede reemplazar eficazmente los dispositivos raster tradicionales.Pueden monitorear las diferencias de temperatura entre las piezas y componentes y el cuerpo humano in situ y determinar si la mano de un operador se encuentra cerca de una zona peligrosa. Pueden establecer una zona de advertencia de seguridad y monitorear los cambios de temperatura en tiempo real mediante líneas y áreas de medición de temperatura.
Si los operadores introducen las manos por error en el área de medición y la temperatura supera el umbral de seguridad establecido (p. ej., 35 °C), el dispositivo activará una alarma y enviará una señal a través de E/S para conectarse al sistema de control PLC, apagando así automáticamente el dispositivo de procesamiento. Esta medida mejora considerablemente la seguridad del procesamiento, protegiendo a los operadores durante el mismo y evitando posibles accidentes con lesiones.
Ventajas de la cámara térmica Raythink para la fundición mecánica
1. Inspección inteligente y alerta temprana de fallas
Cámaras térmicas combinadas con herramientas profesionales de medición de temperatura permiten seleccionar libremente las áreas de monitoreo y obtener automáticamente el punto de temperatura más alto para inspecciones periódicas. La comparación de imágenes térmicas ayuda a detectar daños en los dispositivos medidos y notifica al personal o conecta dispositivos de automatización para su gestión y control.
2. Análisis de datos y mantenimiento predictivo
Se pueden configurar el umbral de temperatura, la duración y el intervalo de muestreo para la recopilación automática de datos. Se utilizan cámaras termográficas para medir el campo de temperatura de la pared exterior del dispositivo. Posteriormente, se analiza la relación lineal entre la temperatura de la pared exterior de la caldera de colada mecánica y la corrosión del refractario del revestimiento interior. La relación obtenida sirve de referencia para la elaboración de planes de mantenimiento.
3. Flexible y conveniente con bajos costos de mantenimiento
Las cámaras termográficas ofrecen un funcionamiento flexible y práctico. Ya no se requieren construcciones preliminares, como la instalación de una plataforma fija y el cableado, y el coste de mantenimiento del dispositivo es relativamente bajo.
4. Integración de sistemas conveniente y de desarrollo propio
Raythink ha desarrollado todos sus productos de hardware, desde detectores hasta módulos y productos terminados. Estos productos... Admite varios protocolos de red como ONVIF, MODBUS y MQTT, lo que facilita la integración de sistemas. Mientras tanto, Raythink ha desarrollado su software de plataforma en la nube VIS-3000 para la integración de sistemas. Este software está diseñado para el acceso y la gestión de dispositivos empresariales. Accede de forma integral a los dispositivos de monitorización en línea desarrollados por Raythink y otros fabricantes mediante los protocolos privados de Raythink, GB28181, ONVIF y MQTT, ideales para el acceso a dispositivos LAN a gran escala.
Presentación del proyecto 1: Mejora de la eficiencia de un fabricante de fundición a presión
Durante la producción de fundición a presión, el control de la temperatura, como el de los moldes, es uno de los factores clave del proceso. Un campo de temperatura estable dentro de los moldes afecta directamente la calidad de la fundición, la eficiencia de la producción y su vida útil, lo que influye en los costos de producción y los beneficios económicos. Si no se mantiene la temperatura del molde dentro del rango requerido, la apariencia y la calidad interna de las piezas fundidas pueden verse afectadas, lo que resulta en una menor eficiencia de la producción. Las cuestiones específicas son las siguientes:
Temperatura excesivamente alta: Se producirán defectos como daños y burbujas, que prolongarán el tiempo de enfriamiento y reducirán la eficiencia de la producción.
Temperatura excesivamente baja: Se producirán defectos como cierre en frío, mal funcionamiento y poros que perjudicarán la calidad del producto.
En la producción de moldes de fundición a presión, estos suelen estar expuestos a entornos de alta temperatura y alta presión. La inestabilidad del campo de temperatura aumenta la probabilidad de fallos de los moldes debido a la expansión y contracción térmica periódicas, lo que no solo acorta su vida útil, sino que también afecta gravemente la eficiencia de la producción.
Demandas de los clientes
Medición de temperatura infrarroja: La temperatura se puede medir al final del proceso de pulverización, tras el hundimiento del molde. La termografía infrarroja se utiliza para evaluar la uniformidad de la temperatura del molde, lo que permite a los ingenieros ajustar fácilmente los parámetros de la máquina de fundición a presión en función de la temperatura.
Activación del umbral de temperatura: Se configuran los umbrales de temperatura, el tiempo y la duración para recopilar datos automáticamente y generar una curva de temperatura. En caso de un enfriamiento anormal, se activa una alarma de temperatura para garantizar la monitorización en tiempo real durante la producción. Mientras tanto, se genera una curva de fluctuación de temperatura que facilita a los ingenieros el seguimiento de los cambios de temperatura.
Solución
La tecnología de imágenes térmicas infrarrojas se utiliza para controlar la temperatura, con señales de alarma de temperatura anormal enviadas al sistema PLCAl recibir una alarma de alta temperatura, el sistema PLC puede controlar automáticamente el robot para realizar el tratamiento de pulverización y extender el tiempo de pulverización para el enfriamiento. El sistema destaca por su capacidad de enfriamiento automático, controlando la temperatura dentro del rango requerido sin necesidad de intervención manual. Esto puede mejorar significativamente la eficiencia de producción y prolongar la vida útil de los moldes.
Presentación del proyecto 2: Monitoreo de temperatura para un horno rotatorio
Debido al calentamiento de la zona de combustión, la pared interior cercana al cabezal del horno rotatorio alcanza la temperatura más alta. Con el aumento del tiempo de funcionamiento del horno rotatorio, el revestimiento interior se adelgaza e incluso se desprende debido a la alta temperatura constante y la fricción de los clínkeres. En consecuencia, la temperatura de la pared de la tubería cambia drásticamente y la temperatura en el horno rotatorio se distribuye de forma desigual, lo que dificulta su funcionamiento estable y fiable. Una temperatura demasiado alta provocará una calcinación excesiva, mientras que una temperatura baja provocará una calcinación insuficiente. Ninguna de las dos producirá resultados de calcinación óptimos.
La inspección manual de rutina tradicional difícilmente puede descubrir áreas excepcionales, incapaz de imponer controles de seguridad efectivos para los hornos rotatorios. Además, el gran tamaño y la rotación continua del horno dificultan la inspección manual y la hacen propensa a omisiones, mientras que Las mediciones de temperatura de un solo punto pueden provocar fallas no detectadas y respuestas retrasadas..
Solución de imágenes térmicas
Las cámaras térmicas permiten monitorear la temperatura en cualquier condición climática, analizar las tendencias de temperatura y generar alarmas para la pared exterior del horno rotatorio, lo que reemplaza la inspección manual. Las cámaras térmicas transmiten imágenes y datos de temperatura a la sala de control en tiempo real para prevenir, gestionar y activar alarmas con antelación.
El cabezal del horno rotatorio inyecta combustible en el horno. Los gases de escape generados durante la combustión se dirigen al material y luego se descargan por el cabezal de descarga. La temperatura disminuye gradualmente desde el cabezal hasta el cabezal de descarga. La temperatura en la posición de enfriamiento del cabezal puede alcanzar los 1400 °C, pero la temperatura en el cabezal de descarga es de tan solo 500 a 800 °C. Las cámaras térmicas pueden... Monitorizar el estado de funcionamiento y los campos de temperatura de la combustión en el horno rotatorio en tiempo real para visualización visual en tiempo real de la temperatura y consultas históricas de temperatura.
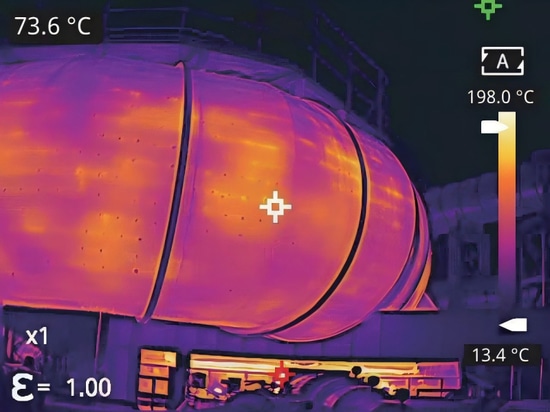
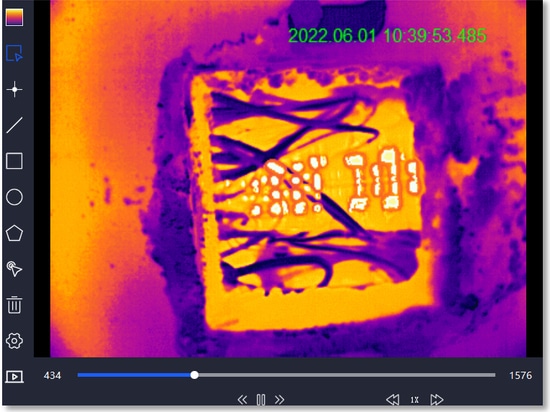
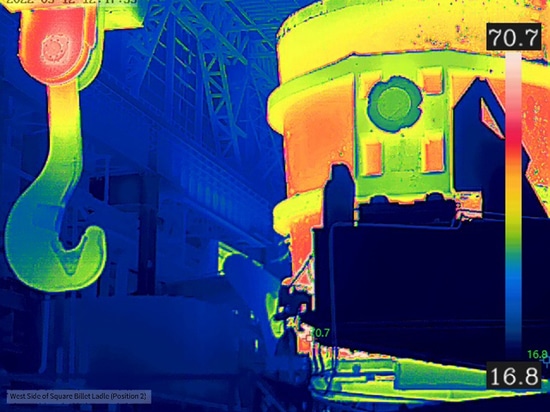