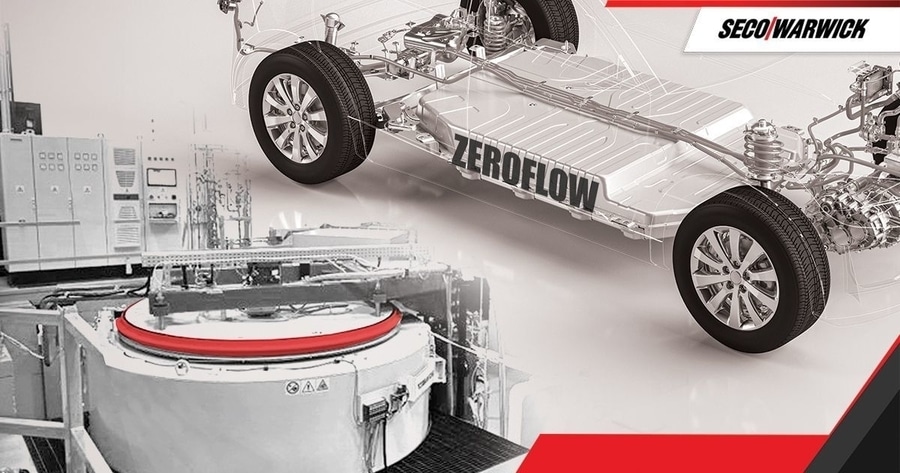
Ver traducción automática
Esta es una traducción automática. Para ver el texto original en inglés haga clic aquí
#Novedades de la industria
Un fabricante de vehículos eléctricos adquiere el segundo horno de retorta de SECO/WARWICK para la producción de chasis de coches eléctricos
Un fabricante internacional de vehículos eléctricos ha realizado un pedido al Grupo SECO/WARWICK de un horno de retorta avanzado diseñado para la nitruración mediante el método ZeroFlow®.
El mayor espacio de trabajo no estándar de la solución permitirá la nitruración de elementos de matriz muy grandes necesarios para la producción de chasis de vehículos eléctricos. Este es el segundo horno de este tipo y la cuarta solución SECO/WARWICK que se suministra a este socio.
Hornos de retorta VR con un diseño especial
La solución encargada es un horno de retorta avanzado, diseñado para la nitruración mediante el método ZeroFlow, así como para el revenido y el recocido. Los hornos de esta familia tienen un diseño compacto con purga de vacío, calentamiento eléctrico apoyado por un ventilador de circulación interna y un sistema de enfriamiento externo. El diseño especial de la retorta y el sistema de calentamiento, así como la instalación de gas, garantizan un funcionamiento duradero y fiable en condiciones industriales.
La solución se basa en un horno de retorta VR vertical estándar con un espacio de trabajo ampliado (Ø 1600 mm y 2800 mm de altura efectiva), que permitirá al Socio nitrurar las enormes matrices utilizadas para los chasis de los coches eléctricos.
"Se trata del cuarto horno SECO/WARWICK para este fabricante mundial de vehículos eléctricos. Nuestro producto resuelve el reto de nitrurar matrices para la producción de chasis de gran tamaño, utilizando un espacio de trabajo con un diámetro de 1.600 mm y una altura de 2.800 mm. El año pasado ya suministramos una solución similar a este socio. En SECO/WARWICK nos centramos en desarrollar un producto que satisfaga las necesidades de nuestros socios, por lo que las soluciones estándar cuentan con una serie de posibilidades de modificación y opciones. Gracias a ello, los clientes reciben un producto hecho a medida. Creemos que el enfoque individual de cada pedido es una de nuestras mayores ventajas en el mercado de las soluciones de tratamiento térmico de metales", afirma Maciej Korecki, Vicepresidente del Segmento de Vacío de SECO/WARWICK.
ZeroFlow: precisión y exactitud
La principal ventaja de la tecnología ZeroFlow es la capacidad de llevar a cabo procesos de nitruración precisos y totalmente controlados, que a su vez producen una alta precisión de las capas de nitrógeno obtenidas con el menor consumo de amoníaco posible.
"Hemos diseñado una solución con unas dimensiones que permiten la nitruración de piezas grandes y pesadas de un modo que cumple las especificaciones del cliente. El proceso patentado de nitruración controlada ZeroFlow® permite a los usuarios obtener resultados óptimos consumiendo incluso varias veces menos amoniaco en comparación con la nitruración tradicional, lo que es beneficioso tanto en términos económicos como ecológicos", comentó Jędrzej Malinowski, Director de Ventas de la Planta de Hornos de Vacío SECO/WARWICK.
El sistema de circulación de atmósfera instalado en el horno dirige el flujo de atmósfera a lo largo de las paredes de la retorta y a través de la carga. Esto garantiza una distribución adecuada de la temperatura durante el tratamiento térmico. ZeroFlow es una versión moderna de la nitruración gaseosa controlada que maximiza la eficacia y eficiencia del proceso, así como el rendimiento económico, superando significativamente los resultados de las soluciones tradicionales. Permite dar forma precisa a cualquier composición de la capa nitrurada, manteniendo un consumo mínimo de factores, y las emisiones de gas posteriores al proceso, cumpliendo las normativas más estrictas de protección del medio ambiente.