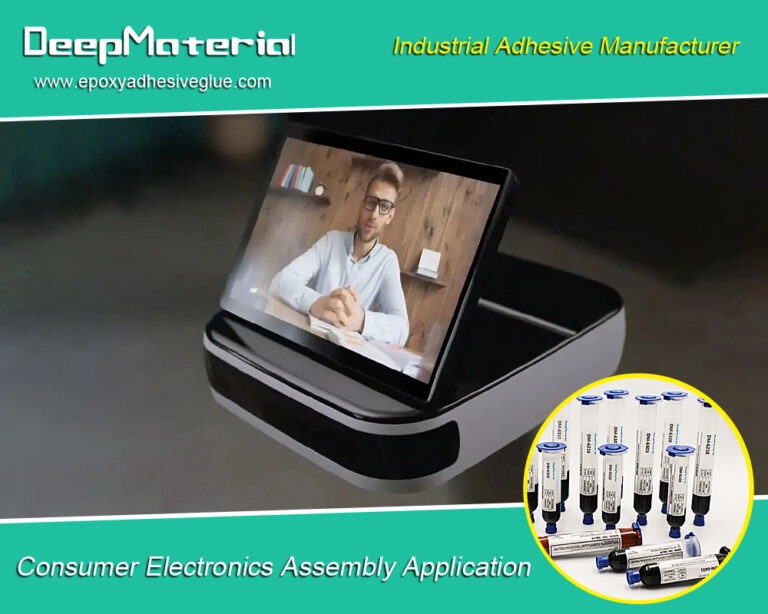
Ver traducción automática
Esta es una traducción automática. Para ver el texto original en inglés haga clic aquí
#Novedades de la industria
¿Puede utilizarse el revestimiento no conductor para electrónica en aplicaciones de automoción o aeroespaciales?
Mejor revestimiento no conductor Pegamento adhesivo para electrónica Fabricante
Sea cual sea el sector, proteger los componentes electrónicos delicados del desgaste externo es absolutamente vital. Los revestimientos no conductores hacen que esa protección sea absolutamente necesaria para las piezas que viven en entornos hostiles, como la industria automovilística y aeroespacial.
Crean un escudo contra la humedad, los productos químicos, las temperaturas extremas y cualquier otra cosa que pueda empañar su fabricación o afectar a su rendimiento Esta capa añadida de protección garantiza la durabilidad, la fiabilidad y un funcionamiento óptimo.
Ventajas del uso de revestimientos no conductores en los sectores de automoción y aeroespacial
Los revestimientos no conductores son una bendición para las industrias automovilística y aeroespacial. Para empezar, aumentan la vida útil de las unidades eléctricas al formar una capa hermética contra la humedad, los productos químicos y los elementos, especialmente en escenarios con grandes vibraciones o cambios de temperatura. Esto protege las conexiones de cortocircuitos o corrosión, lo que se traduce en un rendimiento impecable en todo momento
Además, el uso de estos recubrimientos ahorra dinero que, de otro modo, se gastaría en mantenimiento o reparaciones posteriores: una forma brillante de controlar los costes sin comprometer la calidad. Y por si esto fuera poco, la reducción del número de sustituciones supone una mayor sostenibilidad en los procesos de producción industrial.
Retos de la electrónica en entornos difíciles
Los componentes electrónicos utilizados en la industria aeroespacial y del automóvil están sometidos a una dura prueba. Desde el frío extremo hasta el calor abrasador, los componentes no sólo se dilatan y contraen -lo que a menudo provoca grietas por fatiga o fracturas por tensión-, sino que pueden enfrentarse a problemas de control de la humedad, como la condensación, que puede causar corrosión y fallos eléctricos.
Además, hay que gestionar el riesgo químico, sobre todo cuando se trata de combustibles, lubricantes u otras sustancias potencialmente peligrosas; podría producirse una degradación sutil de las piezas antes de que se manifieste por completo. Tampoco hay que olvidarse de las vibraciones
Todos esos motores que van como locos y los movimientos del transporte pasan factura a los componentes electrónicos si no se tiene el cuidado adecuado, y las sacudidas repentinas de los impactos significan que los componentes electrónicos delicados pueden no volver a estar en su sitio.
Cómo protegen los revestimientos no conductores los componentes electrónicos de los factores ambientales
Los revestimientos no conductores proporcionan un sólido escudo alrededor de los componentes electrónicos, defendiéndolos de los peligros de los factores ambientales. Funcionan como fieles caballeros que protegen contra la humedad o los productos químicos que puedan introducirse y dañar las delicadas conexiones eléctricas.
Esta capa de impermeabilización no sólo puede detener la corrosión o los cortocircuitos, sino que también actúa como aislante, regulando magistralmente las altas temperaturas al reducir la transferencia de calor y aislar del frío más intenso.
Además de todo esto, los revestimientos no conductores ofrecen propiedades de absorción de impactos: un amortiguador para cualquier vibración o sacudida presente que, de otro modo, podría causar un fallo mecánico o evitar una posible desconexión debido a una manipulación brusca.
Tipos de revestimientos no conductores disponibles para la electrónica
Cuando se trata de proteger los componentes electrónicos de temperaturas extremas, humedad e impactos en aplicaciones aeroespaciales o de automoción, existen varias opciones.
Los recubrimientos a base de silicona ofrecen una protección flexible capaz de repeler daños químicos y soportar cambios de temperatura, así como movimientos bruscos. Los epoxis son excelentes para adherirse a las cosas de forma segura: resisten excepcionalmente bien el calor y la tensión provocada por las vibraciones, lo que los hace populares entre los vehículos de ingeniería aeronáutica.
El poliuretano tiene una increíble resistencia a la abrasión, por lo que es una opción obvia cuando se busca algo elástico pero duradero. Perfecto para el duro entorno de cualquier coche o avión
Pero supongamos que lo que más importa es la perfección absoluta. En ese caso, el revestimiento de perileno es su compañero: a prueba de humedad y completamente sellado contra compuestos de autopsia, fundentes de temperatura y desechos de fontanería, lo que los hace perfectos para los niveles más altos de electrodefensa en aeronaves
Factores a tener en cuenta al seleccionar un revestimiento no conductor para aplicaciones aeroespaciales o de automoción
A la hora de elegir un revestimiento no conductor para automóviles o aviones, hay que tener en cuenta varios factores. Todo se reduce al entorno al que estarán expuestas las piezas eléctricas: cambios de temperatura, niveles de humedad, productos químicos y vibraciones o choques deben tenerse en cuenta a la hora de elegir el producto adecuado para que pueda soportar estas situaciones y proteger sus componentes eléctricos.
Además, hay que asegurarse de que el material es compatible con lo que ya existe en esos sistemas; de lo contrario, es tirar el dinero: las pruebas de compatibilidad deben indicarle si este revestimiento reaccionará mal con algo de lo que hay dentro.
Además, siempre hay que pensar en los métodos de aplicación; algunos revestimientos pueden requerir un recubrimiento por pulverización, mientras que otros pueden necesitar un recubrimiento por inmersión o incluso una deposición al vacío, dependiendo de la amplitud de la zona que se quiera cubrir o de la profundidad de la capa de protección
En resumen: también hay que tener en cuenta el coste, tanto a corto plazo, como los costes iniciales y el equipo necesario, como a largo plazo, para el mantenimiento.
En otras palabras, hay que investigar antes de elegir, porque el equilibrio entre coste y rendimiento garantiza la mejor relación calidad-precio.
Métodos de aplicación de revestimientos no conductores en electrónica
Los recubrimientos no conductores pueden aplicarse a los componentes electrónicos por diversos medios, desde la pulverización con pistola o sistema automatizado hasta el recubrimiento por inmersión, pasando por la más sofisticada deposición al vacío.
La pintura por pulverización es una opción de moda porque lo cubre todo con una capa uniforme, por muy intrincada que sea la forma de la superficie. Con el recubrimiento por inmersión se consigue uniformidad y precisión, pero para componentes delicados o estructuras complejas, puede que no sea suficiente.
Si, en cambio, opta por aspirar esa capa, tendrá la seguridad de obtener un grosor preciso independientemente de las especificaciones de su equipo, siempre que cumplan los criterios establecidos, como los niveles de complejidad y los requisitos de volumen de producción.
Por tanto, considere detenidamente cada método antes de elegir uno, en función de la tarea electrónica que tenga entre manos, y elija sabiamente.
Últimas palabras
El campo de los revestimientos no conductores para componentes electrónicos, que tienen que soportar las condiciones más exigentes, es cada día más avanzado. La investigación y el desarrollo siguen revitalizando estos sistemas de protección, prometiendo un mayor rendimiento y una mayor durabilidad.
Para garantizar el máximo nivel de protección, se examinan constantemente nuevas tecnologías y materiales, como la nanotecnología para mejorar las barreras y la resistencia a la humedad, los productos químicos e incluso las temperaturas extremas Si todo va bien con esa investigación, esto podría significar una larga defensa para la electrónica utilizada en la aviación y los automóviles.
Además, la eficiencia y eficacia de los procesos de revestimiento están experimentando mejoras significativas gracias a los avances en sus aplicaciones. Por ejemplo, se están desarrollando pulverizadores robotizados para garantizar que las formas o superficies complejas se cubran de forma precisa y uniforme en todo momento, lo que reduce el tiempo de los procesos de recubrimiento y su coste
Para más información sobre la elección del mejor revestimiento no conductor para electrónica, visite DeepMaterial en https://www.epoxyadhesiveglue.com/category/epoxy-adhesives-glue/.