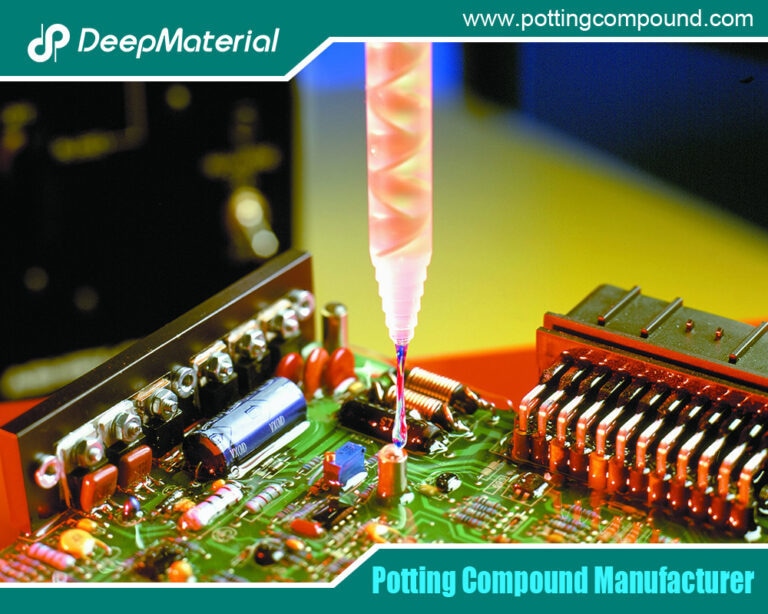
Ver traducción automática
Esta es una traducción automática. Para ver el texto original en inglés haga clic aquí
#Novedades de la industria
Revestimientos conformados para aplicaciones electrónicas
Mejor pegamento adhesivo para revestimientos conformados para fabricantes de electrónica
En el mundo de la electrónica, garantizar la durabilidad y la fiabilidad es primordial. Un método fundamental para conseguirlo es la aplicación de revestimientos conformados. Estas capas protectoras son esenciales para proteger los componentes electrónicos de factores ambientales como la humedad, el polvo, los productos químicos y las temperaturas extremas. Este artículo analiza los revestimientos conformados, sus tipos, aplicaciones, ventajas y tendencias futuras.
1. ¿Qué son los revestimientos conformados?
Los revestimientos conformados son capas protectoras que se aplican a los circuitos y componentes electrónicos para protegerlos de las condiciones ambientales que podrían causar daños o fallos. A diferencia de los revestimientos tradicionales, los revestimientos conformados están diseñados para adaptarse a los contornos del sustrato, proporcionando una capa uniforme de protección incluso en geometrías complejas.
1.1. Finalidad e importancia
El principal objetivo de los revestimientos conformados es aumentar la fiabilidad y la vida útil de los dispositivos electrónicos. Evitan que la humedad y los contaminantes provoquen cortocircuitos o corrosión, que pueden ser perjudiciales para el rendimiento de los conjuntos electrónicos. En aplicaciones de alta fiabilidad, como la aeroespacial, los dispositivos médicos y la electrónica militar, los revestimientos conformados son cruciales para mantener la funcionalidad en condiciones adversas.
1.2. Tipos de revestimientos conformados
Existen varios tipos de revestimientos conformados, cada uno con propiedades y aplicaciones distintas:
Recubrimientos acrílicos: Son populares por su facilidad de aplicación y eliminación. Los revestimientos acrílicos ofrecen una buena resistencia a la humedad y se utilizan normalmente en electrónica de consumo y aplicaciones de uso general.
Recubrimientos de silicona: Conocidos por su resistencia a altas temperaturas y su flexibilidad, los recubrimientos de silicona son ideales para aplicaciones expuestas a temperaturas extremas y vibraciones. Se utilizan habitualmente en los sectores aeroespacial y de automoción.
Revestimientos de poliuretano:Estos revestimientos ofrecen una excelente resistencia química y son adecuados para entornos en los que la exposición a productos químicos es un problema. Se utilizan en electrónica industrial y aplicaciones exteriores.
Revestimientos epoxídicos:Los revestimientos epoxídicos ofrecen una sólida protección contra la humedad y los productos químicos, pero son más rígidos y difíciles de eliminar que otros tipos. Suelen utilizarse en aplicaciones de alta fiabilidad y entornos difíciles.
Revestimientos de parileno: Los revestimientos de parileno se aplican mediante deposición de vapor, creando una capa fina y uniforme con excelentes propiedades de barrera. Se utilizan en dispositivos médicos, electrónica y aplicaciones aeroespaciales.
2. Métodos de aplicación
Se pueden utilizar varios métodos para aplicar revestimientos de conformación, cada uno de ellos adecuado para distintos tipos de revestimientos y requisitos de producción.
2.1. Aplicación por pulverización
La aplicación por pulverización es un método versátil para revestimientos acrílicos, de poliuretano y de silicona. Consiste en pulverizar el revestimiento sobre la superficie utilizando una pistola pulverizadora o una lata de aerosol. Este método es adecuado tanto para procesos manuales como automatizados, por lo que resulta ideal para la creación de prototipos y la producción de volúmenes bajos o medios.
2.2. Recubrimiento por inmersión
El revestimiento por inmersión consiste en sumergir todo el conjunto en un baño de revestimiento para que éste cubra todas las superficies. Este método se utiliza habitualmente para revestimientos acrílicos y de poliuretano y es adecuado para la producción de grandes volúmenes. El revestimiento por inmersión garantiza una capa uniforme, pero puede no ser ideal para conjuntos con componentes delicados.
2.3. Aplicación con brocha
La aplicación con brocha es un método manual de recubrimiento con una brocha o aplicador. Este método es útil para retoques o producción a pequeña escala, pero requiere mucha mano de obra y puede dar lugar a espesores de revestimiento desiguales.
2.4. Recubrimiento selectivo
El revestimiento selectivo consiste en aplicar el revestimiento sólo en zonas específicas del conjunto, normalmente con equipos automatizados. Este método es ideal para proteger componentes sensibles dejando otras regiones sin recubrir. Se suele utilizar con revestimientos acrílicos y de silicona en producciones de volumen medio a alto.
2.5. Deposición de parileno
Los revestimientos de parileno se aplican mediante un proceso de deposición de vapor en una cámara de vacío. El material de revestimiento se vaporiza y luego se deposita sobre el sustrato, creando una capa fina y uniforme. Este método es adecuado para aplicaciones que requieren gran precisión y una cobertura uniforme, como los dispositivos médicos y la electrónica de alta tecnología.
3. Ventajas de los revestimientos conformados
Los revestimientos conformados ofrecen varias ventajas que mejoran el rendimiento y la longevidad de los dispositivos electrónicos.
3.1. Protección contra factores ambientales
Los revestimientos conformados proporcionan una barrera contra la humedad, el polvo, los productos químicos y las temperaturas extremas. Esta protección evita la corrosión, los cortocircuitos y la degradación de los componentes electrónicos, garantizando un rendimiento fiable en entornos difíciles.
3.2. Mayor fiabilidad
Los revestimientos conformados contribuyen a la fiabilidad general de los conjuntos electrónicos protegiéndolos de las agresiones ambientales. Esto es especialmente importante en aplicaciones críticas como la aeroespacial, la automoción y los dispositivos médicos, donde un fallo puede tener graves consecuencias.
3.3. Mayor durabilidad
Los conjuntos electrónicos revestidos son más resistentes a la tensión mecánica, las vibraciones y los ciclos térmicos. Esta mayor durabilidad prolonga la vida útil del dispositivo y reduce la necesidad de reparaciones o sustituciones frecuentes.
3.4. Rendimiento mejorado
Los revestimientos conformados pueden ayudar a mantener el rendimiento de los componentes electrónicos evitando que los contaminantes interfieran en su funcionamiento. Esto es especialmente importante en aplicaciones de alta frecuencia y alta precisión, en las que incluso pequeñas interferencias pueden afectar al rendimiento.
3.5. Rentabilidad
Aunque el coste inicial de aplicar revestimientos conformados puede ser más elevado, las ventajas a largo plazo compensan el gasto. La mayor fiabilidad y durabilidad reducen la necesidad de mantenimiento y sustituciones, lo que en última instancia se traduce en un ahorro de costes a lo largo de la vida útil del dispositivo.
4. Retos y consideraciones
A pesar de sus ventajas, los revestimientos conformados presentan varios retos y consideraciones que deben tenerse en cuenta.
4.1. Selección del tipo de revestimiento
La elección del tipo de revestimiento adecuado para una aplicación específica requiere una cuidadosa consideración de las condiciones ambientales, los materiales de los componentes y los requisitos de rendimiento. Cada revestimiento tiene sus propiedades y limitaciones, por lo que es esencial adaptar el revestimiento a las necesidades de la aplicación.
4.2. Proceso de aplicación
El proceso de aplicación de revestimientos conformados puede ser complejo y requerir equipos y conocimientos especializados. Garantizar una cobertura uniforme, evitar defectos y controlar el espesor del revestimiento son factores críticos para lograr un rendimiento óptimo.
4.3. Compatibilidad con componentes
Algunos revestimientos de conformación pueden reaccionar con determinados materiales o componentes, pudiendo causar daños o afectar al rendimiento. Para evitar problemas, es esencial comprobar la compatibilidad del revestimiento con todos los componentes antes de la aplicación.
4.4. Retirada y reparación
La eliminación de los revestimientos de conformación puede ser un reto en los casos en que sea necesario realizar reparaciones o modificaciones. Diferentes revestimientos requieren diferentes métodos de eliminación; algunos pueden ser más difíciles de eliminar que otros. El proceso de selección del revestimiento debe tener en cuenta la posibilidad de reparación y la facilidad de eliminación del revestimiento.
5. Tendencias futuras en revestimientos conformados
El campo de los revestimientos conformados evoluciona continuamente, y la investigación y el desarrollo continuos dan lugar a nuevos avances y tendencias.
5.1. Materiales avanzados
Los investigadores están explorando nuevos materiales y formulaciones para los revestimientos conformados con el fin de mejorar sus propiedades y rendimiento. Los avances en nanotecnología y polímeros están conduciendo al desarrollo de revestimientos con mejores propiedades de barrera, flexibilidad y resistencia medioambiental.
5.2. Recubrimientos inteligentes
Los revestimientos innovadores son una tendencia emergente que implica la incorporación de sensores o elementos funcionales en el revestimiento. Estos revestimientos pueden monitorizar en tiempo real las condiciones ambientales o los cambios en la integridad del revestimiento, ofreciendo capas adicionales de protección y capacidades de diagnóstico.
5.3. Recubrimientos ecológicos
Cada vez se hace más hincapié en el desarrollo de revestimientos conformados ecológicos que minimicen el impacto ambiental. Los revestimientos a base de agua y de bajo contenido en COV (compuestos orgánicos volátiles) son cada vez más comunes, en consonancia con los objetivos de sostenibilidad y los requisitos normativos.
5.4. Integración con la automatización
La integración de los procesos de revestimiento conforme con la automatización y las tecnologías de la Industria 4.0 mejora la eficiencia y la coherencia de la producción. Los sistemas automatizados de revestimiento equipados con funciones avanzadas de control y supervisión están mejorando la precisión y la calidad de las aplicaciones de revestimiento.
Conclusión
Los revestimientos conformados protegen los componentes electrónicos y garantizan su fiabilidad y longevidad. Con varios tipos de revestimiento y métodos de aplicación disponibles, los fabricantes pueden elegir la mejor solución. Aunque hay que tener en cuenta algunos retos, las ventajas de los revestimientos conformados los convierten en una valiosa inversión en electrónica de alto rendimiento. A medida que avance la tecnología, el campo de los revestimientos conformados seguirá evolucionando, ofreciendo nuevas soluciones e innovaciones para satisfacer las demandas de un panorama electrónico en constante cambio.
Para más información sobre la elección de los mejores revestimientos conformados para aplicaciones electrónicas, visite DeepMaterial en https://www.pottingcompound.com/.