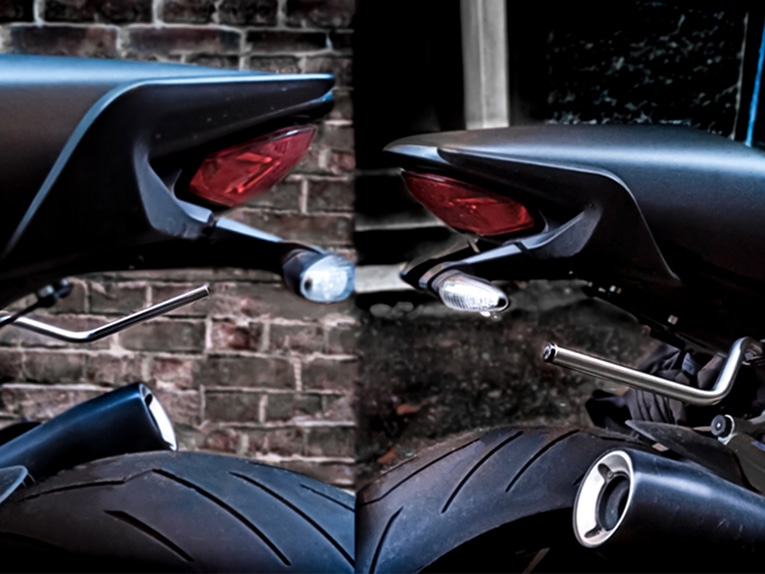
Ver traducción automática
Esta es una traducción automática. Para ver el texto original en inglés haga clic aquí
#Tendencias de productos
Piezas de repuesto para una moto: del escáner 3D a la impresión 3D
Actualización de la moto con el flujo de trabajo Scan-Design-Print de SHINING 3D
Con la tecnología 3D, la comunidad mundial de fabricantes, diseñadores profesionales e ingenieros hacen realidad los impresionantes artilugios. Como empresa que siempre se esfuerza por alcanzar la excelencia en los sectores de la digitalización 3D, el diseño inteligente y la impresión 3D, nuestro objetivo es inspirarle con un ramillete de ideas extraordinarias que usted también puede utilizar para mejorar su vida cotidiana de manera eficiente En el caso de hoy examinamos el proceso de sustitución de un recambio de moto que fue reproducido más rápido y mucho más rentable con las tecnologías desde el escaneo hasta la impresión, ¡impulsado por SHINING 3D!
¿No es conveniente cuando se va de viaje, tener todo lo necesario a mano sin necesidad de usar una gran maleta? Dos tubos de acero simétricos en el eje se pegan en una fijación de una motocicleta que compone un soporte de alforja y permiten así montar el equipaje en la parte trasera del vehículo. Desafortunadamente, uno de estos tubos se perdió durante la conducción, por lo que para continuar el viaje de conveniencia, se necesita un reemplazo. Hemos abordado este tema mediante la digitalización 3D y la impresión 3D en metal, tecnologías con las que SHINING 3D pretende mejorar y añadir valor a las vidas de muchos.
PASO 1: ESCANEO 3D
La digitalización 3D es una disciplina que todavía puede considerarse como una punta secreta extremadamente eficiente en la cadena de flujo de trabajo aditivo, porque puede sustituir a los complejos procesos de diseño y facilitar el desarrollo de productos en dimensiones revolucionarias. En nuestro caso, el recién lanzado escáner 3D portátil de luz híbrida EinScan HX se utiliza para digitalizar el tubo de acero sobrante. Los escáneres EinScan 3D popularizan la aplicación de la última tecnología de digitalización en 3D y la hacen accesible tanto a los profesionales, como a los creativos y a los aficionados en casa. Tras el proceso de digitalización, se exporta un archivo STL desde el software EXScan Pro, lo que allana el camino para el siguiente paso en la cadena de flujo de trabajo aditivo.
PASO 2: DISEÑO INTELIGENTE
El archivo STL exportado desde EXScan Pro se importa en el software Voxeldance Additive, un software de preparación de datos que ayuda a ahorrar tiempo de producción y a optimizar el flujo de trabajo de impresión. La geometría de la superficie bruta del STL se está reparando y cerrando a un modelo estanco utilizando el Módulo de Fijación. Dado que los dos tubos de acero que componen el soporte de equipaje son axisimétricos, la pieza escaneada se refleja alrededor de dos ejes para generar las características originales de la pieza faltante. Como en este caso queremos resaltar el valor excepcional que la tecnología digital 3D puede añadir, especialmente en el campo de la producción, decidimos imprimir en 3D el tubo con un material mucho más ligero que el original. La aleación de aluminio AlSi10Mg utilizada, pesa sólo 2/3 del acero inoxidable del que está hecha la pieza original.
Para crear una parte aún más fuerte que la original, se está utilizando el Aditivo de Estructura de Voxeldance. Este procedimiento fácil de usar ayuda a ahuecar la pieza, crear una estructura de rejilla altamente variable y añadir agujeros de vertido para eliminar el polvo no fundido dentro de la barra. El hecho de tener todas estas valiosas características combinadas en un solo software hace de Voxeldance Additive una poderosa herramienta para la preparación de datos de impresión en 3D.
PASO 3: FABRICACIÓN ADITIVA
Las piezas optimizadas se funden en la realidad por la impresora 3D láser dual de metal EP-M250 Pro. Para facilitar la retirada de las piezas impresas de la plataforma de construcción, la estructura de soporte ha sido diseñada utilizando el software de preparación Voxeldance Additive. Con la función de soporte automático, se utiliza un guión de parámetros de soporte predefinidos pero altamente ajustables para crear el soporte de forma perforada y fragmentada, pero lo suficientemente fuerte para mantener las piezas en posición. Después de 4,5 horas de fusionar las partículas de metal, los dos tubos pueden ser retirados fácilmente de la plataforma con las manos y los alicates.
PASO 4: POST-PROCESAMIENTO
Para lograr una superficie lisa y un buen aspecto general, el post-procesamiento es crucial. En la parte inferior de la pieza, la estructura de soporte se retira con alicates y limas. El uso de lija y una máquina de chorro de arena con corindón blanco dan a la pieza el perfecto acabado mate.
ANÁLISIS DE RENTABILIDAD
Combinando todos los factores de coste en este proceso como mano de obra, materia prima, electricidad, desgaste de la maquinaria y costes de local, se alcanza un total de 184 euros para ambos bares. El OEM sólo ofrece comprar un juego completo del sistema de alforjas por 310 euros. El uso de la impresión 3D en metal ha ayudado a reducir el peso de la montura de la alforja de 525 g a 86 g, lo que supone una reducción de peso del 83%, a la vez que aumenta la estabilidad gracias al diseño de estructuras de soporte integradas en el interior de las tuberías.
Si quieres saber más sobre el flujo de trabajo digital de Shining 3D o necesitas ayuda para calcular los costes totales de tu impresión, ¡contáctanos hoy! Estamos encantados de ayudarle a ahorrar tiempo, material y dinero - para más ideas brillantes!