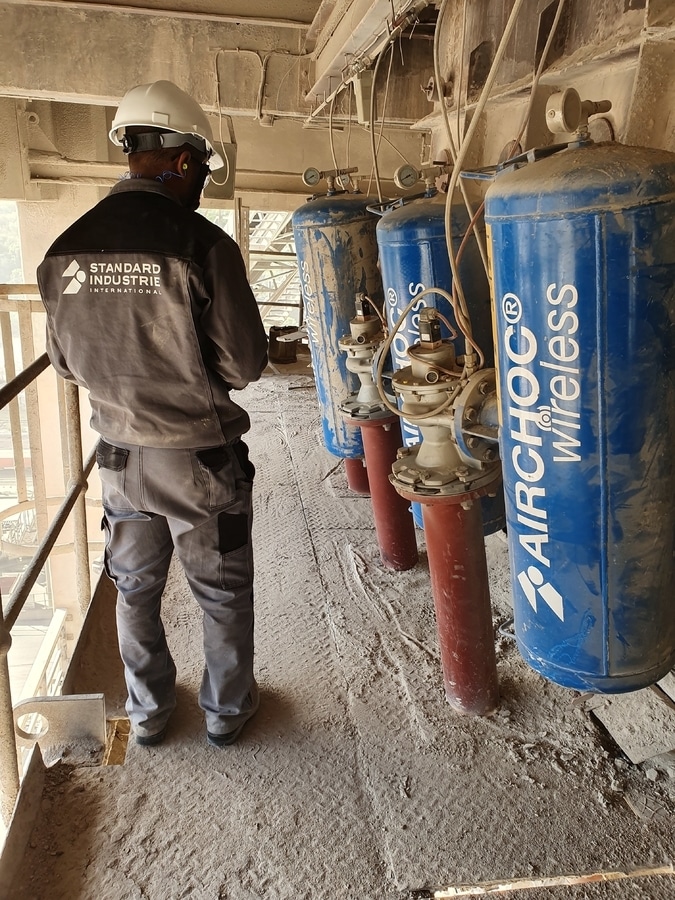
Ver traducción automática
Esta es una traducción automática. Para ver el texto original en inglés haga clic aquí
#Novedades de la industria
¿Cómo garantizar el mantenimiento del flujo de producción de cemento en 5 puntos?
Los fabricantes de cemento pueden utilizar varios métodos para prevenir y eliminar la acumulación de material y mejorar su flujo a lo largo del proceso de producción de cemento.
Standard Industrie International, especialista en equipos de manipulación y limpieza para la industria a granel, lleva muchos años colaborando con los grandes grupos cementeros en esta cuestión. Los expertos de esta empresa francesa, con presencia internacional, explican aquí cómo pueden tratarse las acumulaciones y atascos en distintas zonas de la cementera, mejorando así la productividad y la seguridad de la planta.
1- Eliminar las acumulaciones en la torre de precalentamiento y el efecto muñeco de nieve en el enfriador de clínker.
Estos problemas son frecuentes y deben evitarse para garantizar una producción de clínker estable y regular.
En este contexto, Standard Industrie International pone a disposición de sus clientes una gama completa de cañones de aire AIRCHOC®. Esto incluye tanto torres de precalentamiento como enfriadores. El diseño del cabezal AIRCHOC® es de acero fundido con un revestimiento de zinc iridiscente especialmente dedicado a resistir entornos de altas temperaturas.
Un programa secuenciado de disparo de los cañones de aire garantiza la eliminación de los riesgos de obstrucción y asegura una producción constante sin paradas.
CAJA DE CUCTOMER : LOMA NEGRA, planta de Zapala (parte del grupo brasileño INTERCEMENT) en Argentina
Esta fábrica de cemento equipó su torre de precalentamiento con 11 cañones de aire AIRCHOC® con el fin de eliminar las concreciones y evitar el anillado manual.
Se instalarán en el conducto ascendente durante la próxima parada del horno programada en agosto de 2022, además de los 18 AIRCHOC® adquiridos (12 cañones de aire en julio de 2018 y 6 cañones de aire en mayo de 2019) instalados en la entrada del horno, la cámara de humos y los cilindros. Esta planta, que cuenta con un horno de producción de 760 t/d de KHD de 1970, utiliza un 80% de gas y un 20% de fuelóleo. Los cañones de aire AIRCHOC® son muy eficaces en este tipo de instalación.
2- Evitar la acumulación de material en la caja de humos y evitar la ralentización de la velocidad del gas.
Esta zona es clave y mantenerla libre de acumulaciones facilita la circulación del gas. He aquí un ejemplo de instalación de 5 MACSYS® en versión inalámbrica.
El MACSYS® es un tipo específico de cañón de aire que tiene varios cabezales conectados al mismo depósito. Para esta aplicación, las veinte cabezas están equipadas con manguitos de compensación antivibraciones. Cada manguito está conectado a la caja de humo mediante una red de tubos. Al final de cada terminación de tubo fijo hay deflectores, cada uno con sus particularidades en función del trabajo de limpieza requerido.
Jérémie FRELIEZ, responsable de la oficina de proyectos de Standard Industrie International, comenta las particularidades de esta instalación:
"El objetivo es llegar fácilmente a los rincones para mejorar la limpieza colocando cinco MACSYS® en cuatro niveles diferentes. La solución inalámbrica nos ha permitido ahorrar mucho en el coste de los cables y las bandejas portacables.
Se tarda una media de 2 a 3 minutos en llenar el depósito de doscientos litros a seis bares, lo que permite realizar disparos cortos. El resultado directo es una mejora de la calidad del cemento, así como del ritmo de producción. Tras esta instalación y su eficacia, el cliente equipó también el enfriador.
El MACSYS® Wireless está accionado por el mismo panel de control que permite gestionar hasta ciento veintiocho cañones de aire AIRCHOC®"
3- Evitar las concreciones en los silos de almacenamiento de material.
El atasco de material en los silos supone una pérdida de productividad, pero también un mayor riesgo para el personal de mantenimiento. Además, si una obstrucción se desprende, puede causar daños al caerse. El flujo de producción puede verse interrumpido.
Los cañones de aire AIRCHOC® se instalan en los silos para detener los atascos existentes, evitar que se formen otros nuevos y, en consecuencia, reducir o eliminar las intervenciones de limpieza. Este es el caso, en particular, de las tolvas de caliza, puzolana, arcilla y cal, y al final del proceso de los silos de recuperación de clinker, cemento y cenizas.
4- Limitar los riesgos de ensuciamiento relacionados con el uso de combustibles alternativos en todo el proceso de producción de cemento.
Hoy en día, la gran mayoría de las fábricas de cemento han aumentado el uso de combustibles alternativos, biomasa y residuos diversos para alimentar sus hornos. El coste de estos combustibles, más baratos que las "materias primas", su abundancia en el mercado local, la reducción de las emisiones de CO2, la preservación de los recursos y el alto rendimiento térmico de estos combustibles han dejado obsoletos los combustibles fósiles.
Hoy en día, el uso de combustibles alternativos ha empujado a Standard Industrie a adaptarse y ofrecer diferentes sistemas de cañones de aire para resolver estos nuevos problemas de obstrucción. Standard Industrie aporta una respuesta técnica adaptada a la evolución de las tecnologías. Quemar sólo carbón o quemar varios combustibles alternativos son procesos muy diferentes.
Benoît PLUCHON, Export Sales Manager de Standard Industrie International, comparte su experiencia:
"Nuestros expertos han observado en los últimos 15 años que el uso de combustibles alternativos cambia la naturaleza de las incrustaciones. En efecto, el contenido de azufre es generalmente más elevado que antes, cuando sus clientes quemaban combustibles 100% fósiles. Estudiamos la estabilidad del proceso y el funcionamiento del horno de cemento, incluida la acumulación de material en los ciclones u otras zonas del proceso, y llegamos a la conclusión de que los atascos habituales son más pegajosos y fuertes con el uso de combustibles alternativos"
Para mantener la eficacia de la instalación del cañón de aire y evitar que se produzcan "instalaciones de árbol de Navidad" (una gran cantidad de cañones instalados en la torre de precalentamiento), Standard Industrie optimizó la eficacia de su cañón de aire para que tuviera más impacto en los atascos.
David FREGEZ, Jefe de Producto de Standard Industrie International desde hace más de 15 años, explica:
"Desde hace más de 5 años, Standard Industrie sugiere a sus clientes que cambien de opinión sobre el tamaño de los dispositivos mecánicos. Anteriormente, para un proceso que quema una gran mayoría de combustibles fósiles, el estudio técnico y la oferta se proponían con un AIRCHOC® con un diámetro de salida de 100 mm (4"). Al realizar una comparación, comprobamos que el uso de dicho diámetro era menos eficaz cuando nuestros clientes utilizaban una mezcla de combustibles fósiles y alternativos. La fuerza de impacto generada no era suficiente y el aumento de la secuencia de encendido no era realmente eficaz a lo largo del tiempo. Además, implicaba un mantenimiento adicional con costes añadidos y pérdida de un tiempo valioso. Se sabe que el cambio gradual a cabezales de 150 mm (6") es muy eficaz y económico"
5- Limpiar los silos de almacenamiento de cemento
El almacenamiento de cemento en grandes silos de hormigón no es inmune a los atascos. Algunas plantas optan por instalar sistemas de limpieza como los cañones de aire AIRCHOC® y otras optan por limpiar manualmente sus silos de forma periódica, cuando las extracciones se bloquean y el producto se queda pegado en las paredes.
Cyril PARISOT, responsable del departamento "Servicios de limpieza" de Standard Industrie International, explica:
"Existen distintos métodos, como boquillas de fluidificación, vibradores, acceso mediante cuerdas o explosiones, pero no son las soluciones más eficaces ni las más seguras.
La GIRONET, en cambio, es la solución de limpieza más segura del mercado para obtener un resultado muy satisfactorio. Se trata de una máquina que debe colocarse en la parte superior del silo. Un brazo articulado se desliza por el interior y el motor, controlado desde el exterior, acciona una serie de herramientas para limpiar toda la unidad de almacenamiento. Los clientes que eligen este método recuperan casi la capacidad de almacenamiento original. El equipo de intervención de Standard Industrie International restablece toda la capacidad del silo sin intervención humana en su interior, y lo importante es que así se elimina cualquier riesgo de accidente. El GIRONET existe en versión ATEX, pero aparte de esta última evolución, es el equipo que menos cambios ha sufrido en nuestra empresa, ya que ha demostrado su eficacia tras numerosas actuaciones. Nuestros equipos intervienen 10 meses al año para el mantenimiento de las unidades de almacenamiento o para solucionar problemas en caso de bloqueo total".
CASO DE CLIENTE : CALCIA Beaucaire en Francia
Debido a la humedad, el silo de cemento se atascó y creó un puente, por lo que la extracción ya no era posible. Sólo una intervención del equipo STANDARD INDUSTRIE hizo que el silo fuera operativo y seguro, sin operarios en el silo.
¿Cómo funciona este tipo de intervención?
En caso de que la planta se enfrente a una reducción de la capacidad de recogida, el uso de la GIRONET neumática, propuesta por Standard Industrie International, ayudará a limpiar los silos y permitirá recuperar toda la capacidad de almacenamiento.
El brazo articulado de la GIRONET, que gira 360°, elimina los problemas de ratoneras. Esta solución cumple las estrictas normas de seguridad: Evita cualquier presencia humana en el interior de los silos. La intervención de la GIRONET permitirá aumentar la capacidad de recogida para evitar interrupciones de suministro. La GIRONET es eficaz en cualquier tipo de atasco, producto o unidad de almacenamiento. Puede utilizarse sin detener la producción.
Además, la desobstrucción con la POWERNET resolverá los problemas de obturación mediante la rotura segura del material atascado para que fluya más libremente. La POWERNET se utiliza antes que la GIRONET cuando la unidad de almacenamiento está completamente atascada. La idea de la POWERNET es crear una chimenea a través de la cual se utilizará la GIRONET para descolgar las acumulaciones.
El medio ambiente, la seguridad y la rentabilidad están en el centro de toda industria; existen muchas alternativas a corto y medio plazo en el mercado. Standard Industrie International, muy implicada en la industria cementera, ha optado por ofrecer a los grandes grupos internacionales productos de calidad que combinan una tecnología avanzada con una respuesta adaptada a los problemas de productividad.