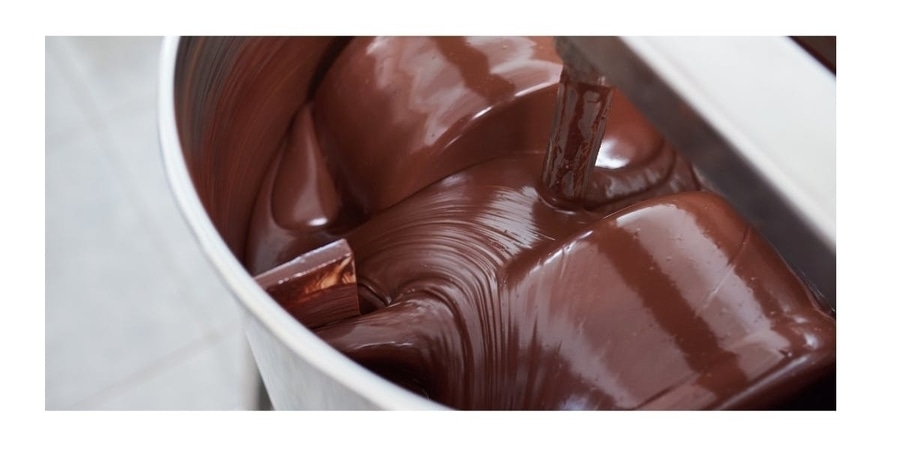
#Tendencias de productos
Lo que hay que saber para transportar fluidos viscosos
¿Trabaja con productos viscosos como aceites, jarabes, ceras, chocolates o fluidos viscosos similares?
Entonces sabrá que el procesamiento de líquidos viscosos conlleva una serie de retos únicos:
1. Mantenimiento de la fluidez: Al cambiar la temperatura, las propiedades de fluidez varían y hay que controlarlas con más cuidado.
2. 2. Limpieza: la pegajosidad hace que sea mucho más difícil de limpiar, por lo que debe prestar especial atención a la limpieza para garantizar la higiene en sus instalaciones de producción.
3. Costes de eliminación de residuos: la alta viscosidad aumenta considerablemente los residuos y los costes, reduciendo la eficiencia de los procesos de fabricación.
4. Necesidad de equipos especiales adaptados al flujo viscoso.
Por ejemplo, si comparamos un cliente que transporta agua y otro que transporta un producto viscoso como el chocolate, podemos ver que el líquido viscoso presenta una mayor resistencia al flujo. Si no proporcionamos una solución especial para transportar y gestionar el flujo del producto viscoso, la temperatura no se mantiene y disminuye considerablemente en el trayecto.
Como puede ver, la viscosidad supone un importante reto para todas las etapas de producción, especialmente en el sector alimentario.
1. Elegir la manguera adecuada para mantener la temperatura
Venair tiene una solución especial para transportar productos viscosos, una manguera con calefacción eléctrica. Se trata de una manguera calefactada eléctricamente de silicona altamente flexible FDA y USP VI que proporciona una temperatura regular en toda su longitud. Suele utilizarse para aplicaciones en las que es fundamental garantizar una temperatura constante para ayudar a mantener una fluidez óptima del producto transportado.
La manguera puede resistir las siguientes escalas de temperatura: -55°C/+180°C (-67ºF/ 356ºF)
La manguera presenta un sistema eléctrico totalmente integrado que garantiza un sistema de seguridad completo y un acabado muy suave, lo que la convierte en la solución perfecta para la mayor higienización del proceso.
El calentamiento directo gestionado adecuadamente es la mejor solución que se puede proporcionar, mediante un calentamiento eléctrico de baja densidad de vatios se puede gestionar el flujo de fluido, evitar el sobrecalentamiento y mitigar la degradación involuntaria.
Puede descargar los detalles técnicos para obtener más información.
Sin embargo, cuando el control de la temperatura no es tan crítico para el proceso de fabricación, una solución alternativa puede ser utilizar TELCRA, una manguera aislante que ofrece aislamiento térmico y ayuda a reducir el descenso de la temperatura a lo largo de la manguera.
La manguera puede resistir las siguientes escalas de temperatura: -55°C / +180°C (-67°F/356°F).
Puede descargar los detalles técnicos para obtener más información o buscar más información en nuestro último artículo.
2. Elija las conexiones adecuadas para asegurar el flujo de fluido
Utilizar una manguera engarzada que evite la contaminación es fundamental. En Venair todas nuestras mangueras están engarzadas con un sistema SZR, un sistema que elimina las contaminaciones que puedan aparecer entre la unión de la manguera y los racores colocando dos racores en el extremo al mismo nivel de la manguera.
El sistema SZR evita las máximas diferencias de diámetro entre el racor metálico y la manguera, asegurando un flujo continuo de producto sin turbulencias internas. Esto supone un ahorro de tiempo al permitir realizar la limpieza in situ (CIP) sin necesidad de desmontarla. El sistema de montaje SZR garantiza un mayor nivel de no retención en las mangueras flexibles, así como una mayor seguridad de uso. Descubra más información sobre nuestras soluciones de racorado en el siguiente artículo.
3. Utilice diseños personalizados para optimizar su proceso de producción
Nuestros expertos pueden ofrecerle construcciones personalizadas que se adapten a sus diseños de maquinaria y procesamiento para lograr una optimización de los procesos.
Podemos construir las mangueras con diferentes materiales adaptados a sus necesidades de compatibilidad de fluidos y presión, nuestra manguera calefactada se construye de forma estándar con silicona platino USP VI, sin embargo, puede fabricarse con los siguientes materiales:
Cubierta aislante y anticondensación para proteger a los operarios de las quemaduras.
Capas interiores de materiales de fluorocarbono o fluoropolímero para una mayor compatibilidad química con productos químicos como ácidos y aceites.
Podemos fabricar construcciones de mangueras calefactadas bajo demanda; codos y formas especiales que se adaptan a cualquier tipo de maquinaria utilizada para el procesamiento alimentario o farmacéutico: mezcladoras, secadoras, llenadoras, recubridoras...
Solemos ayudar en una amplia gama de procesos, para aplicaciones alimentarias presentamos una amplia experiencia en el procesamiento de chocolates, miel, caramelos, jarabes y cremas. En el sector farmacéutico y cosmético, trabajamos con parafinas, ceras y glicerinas. Sin embargo, podemos ayudarle en cualquier tipo de aplicación que necesite para controlar la viscosidad.
Para más información y asistencia, puede llamar a cualquiera de nuestros asesores que presentamos en todo el mundo.
4. Garantizar una instalación y un mantenimiento seguros
Para garantizar una instalación y operatividad segura de la manguera, debe tener en cuenta:
Instalarla para que sea accesible en cualquier momento y no se vea obstaculizada en su posición y movimiento natural.
Asegurarse de que la manguera está protegida de daños causados por influencias mecánicas, térmicas o químicas del exterior.
Además, para asegurar un correcto mantenimiento, debe inspeccionar periódicamente las mangueras interna y externamente. En caso de daños internos o externos visibles, no debe ponerla en funcionamiento.
Para más información sobre la seguridad y la instalación, consulte nuestras directrices y recomendaciones.
5. Utilice códigos QR rastreables para un mantenimiento y una sustitución eficaces
La manguera calefactada puede marcarse con un código QR que permite conservar todos los datos esenciales como la fecha de fabricación, el número de lote, el certificado, la presión máxima .... Esto facilita el cumplimiento de todas las normativas y la realización de trabajos de mantenimiento y sustitución eficaces.