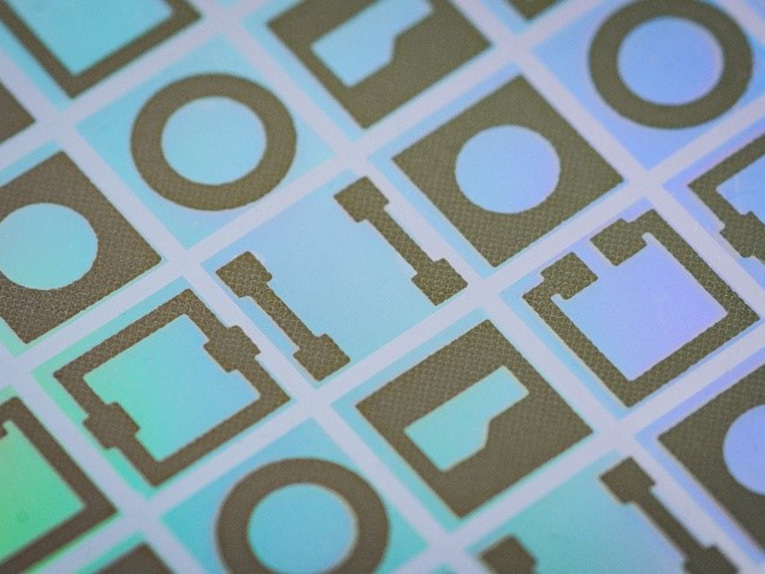
Ver traducción automática
Esta es una traducción automática. Para ver el texto original en inglés haga clic aquí
#Novedades de la industria
Producción de microópticos más barata y sencilla
Gracias a la microóptica y la nanoóptica se crean sistemas ópticos cada vez más compactos. Esto abre el camino a funcionalidades completamente nuevas que no pueden conseguirse con la óptica convencional. La impresión UV, por su parte, hace realidad la producción en serie rentable de este tipo de ópticas.
¿Qué son las microópticas y dónde se utilizan?
En pocas palabras, la microóptica es una versión miniaturizada de la óptica convencional. Los componentes de esta última, como lentes, espejos o prismas, son sólo unos pocos órdenes de magnitud más largos que la longitud de onda de la luz que los atraviesa.
Los endoscopios médicos son una aplicación en la que las ventajas de reducir el tamaño de la óptica resultan especialmente evidentes. En los últimos años, la microóptica y las técnicas de fabricación correspondientes han permitido reducir todo el módulo óptico (incluido el sensor de imagen) a un cubo con una longitud de arista <1 mm (véase la figura 1a).
Además de sus reducidas dimensiones, la microóptica también permite aplicar conceptos nuevos y mejorados a tareas ópticas centenarias, como los sistemas de proyección. En lugar de utilizar lentes individuales dispuestas una detrás de otra para crear una voluminosa configuración para la proyección de imágenes, se utiliza una matriz de microlentes para paralelizar la proyección. De este modo se consigue un elevado flujo luminoso con una fracción del tamaño de los sistemas de proyección convencionales, gracias a la reducción de la distancia focal (véase la figura 1b).
Si la dimensión se reduce de micro a nanoscópica, el método de dirección de la luz cambia de refractivo a difractivo. Esto abre un sinfín de nuevas posibilidades. Por ejemplo, los elementos ópticos difractivos (DOE) pueden utilizarse para cambiar un haz láser colimado (recto) en prácticamente cualquier distribución de luz deseada. Un ejemplo notable es la creación de un patrón de puntos utilizado en la detección 3D para medir la anchura, la altura y la profundidad de un objeto (véase la figura 1c).
¿Cómo funciona el proceso de fabricación?
Este nuevo tipo de óptica requiere naturalmente nuevos métodos de fabricación. Los métodos convencionales, como el moldeo por inyección, son menos adecuados debido a los tamaños de estructura y la alineación precisa que requieren.
El proceso de micro/nanoimpresión UV es ahora una herramienta establecida y fácilmente disponible en las máquinas estándar que ofrecen varios fabricantes. En este caso, se aplica un material de curado UV líquido y transparente a una oblea de vidrio y, a continuación, se pone en contacto con un sello estructurado. Una vez que el sello ha definido la geometría de la óptica, como las lentes y las DOE, el material se cura con luz UV. A continuación se retira el sello y la oblea estructurada se corta en módulos individuales (véase la figura 2).
Integración de aperturas como capa funcional
Las cosas se complican un poco más cuando hay que integrar características adicionales en un elemento óptico. Las aperturas, por ejemplo, son elementos clave en muchos diseños ópticos.
Hasta ahora, las aperturas se integraban de serie en la óptica impresa mediante un proceso fotolitográfico. Para ello, primero se crea una capa de cromo estructurada en una oblea de vidrio y, a continuación, se imprime la óptica directamente en la oblea.
El proceso fotolitográfico implica un gran número de pasos:
- Recubrimiento de una oblea de vidrio con una capa homogénea de cromo
- Depósito de una capa fotorresistente
- Estructuración de la capa fotorresistente mediante una etapa de litografía
- Revelado químico de la capa fotorresistente
- Eliminación de una parte de la capa de cromo
- Eliminación de la capa fotorresistente restante
Desventajas de esta solución:
- Este proceso es muy complejo y, por tanto, caro.
- Además, restringe mucho las posibles aplicaciones de este tipo de aperturas. Este proceso sólo funciona en obleas de vidrio y, por lo general, no es compatible con la estructuración de una capa de cromo en la propia óptica polimérica.
- Pueden surgir otros problemas debido a una adhesión insuficiente de la capa de cromo al vidrio o del material polimérico al cromo.
Nuevo enfoque 1: incrustación directa de un material funcional en la óptica
Muchos de los problemas mencionados pueden evitarse incrustando un material funcional (por ejemplo, negro) directamente en la óptica polimérica. Una forma de conseguirlo es imprimir estructuras de canales definidas además de la estructura óptica durante el proceso de impresión. A continuación, estos canales pueden rellenarse con un material negro de baja viscosidad que se cura con luz ultravioleta o calor (véase la figura 3). Esto simplifica enormemente el proceso.
Otra ventaja de esta opción es que las propiedades termomecánicas de los dos materiales (ópticamente transparente y negro) están mucho más próximas entre sí que las del vidrio, el cromo y el polímero. Así se evitan las tensiones térmicas provocadas por desajustes en el coeficiente de expansión térmica (CET). Esto mejora directamente la fiabilidad, como han demostrado las pruebas de ciclos de temperatura. Como este método ya no requiere sustratos de vidrio, el peso y la altura de las ópticas se minimizan de forma eficaz y, al mismo tiempo, se reducen los costes.
Nuevo enfoque 2: Utilización de un soporte provisional
Otro enfoque posible es empezar con un soporte temporal (por ejemplo, una lámina de plástico). Las aberturas se producen en el soporte mediante serigrafía de un polímero que bloquea la luz. Tras el curado UV o térmico del polímero, se procede a la impresión UV estándar, en la que las estructuras ópticas pueden alinearse con precisión con las aberturas. Una vez endurecido el material transparente y retirado el sello, puede despegarse la lámina portadora. El resultado es un módulo óptico completamente monolítico (totalmente polimérico) con aberturas integradas (véase la figura 4).
Ambos nuevos enfoques tienen la ventaja común de que las propiedades de los materiales negros pueden adaptarse a cualquier diseño óptico y a sus respectivos procesos:
- Ejemplo 1: Un material serigrafiable con viscosidad moderada y un elevado coeficiente de absorción para una alta densidad óptica en capas finas de pocos µm.
- Ejemplo 2: Un material para el relleno de estructuras funcionales con baja viscosidad y un coeficiente de absorción moderado para una alta densidad óptica en estructuras de unos pocos 100 µm.
- Incluso es posible incorporar una función de filtro espectral directamente en el polímero (por ejemplo, bloqueando un determinado rango de longitudes de onda mientras se permite la transmisión en otro rango de longitudes de onda).
Integración de capas funcionales conductoras de la electricidad
Algunas aplicaciones requieren la integración de estructuras conductoras de la electricidad en el elemento óptico. Un ejemplo es el elemento difusor utilizado en los sensores de tiempo de vuelo o en los sensores de luz estructurada que forman el haz láser colimado del emisor. En este caso, las estructuras conductoras se utilizan como red de seguridad para detectar posibles daños en el elemento difusor, evitando así cualquier amenaza del haz láser emitido. Para producir dicha red de seguridad puede utilizarse un proceso similar al empleado para las aberturas. Sin embargo, se utiliza un adhesivo isótropo conductor de la electricidad (ICA) en lugar de un polímero negro.
En primer lugar, se serigrafía un ICA (por ejemplo, DELO DUALBOND IC343) sobre una lámina portadora temporal que contiene diversas estructuras (por ejemplo, pistas conductoras, aberturas). A continuación, se utiliza un material transparente de curado UV (por ejemplo, DELO KATIOBOND OM614) para imprimir una nanoestructura en esta lámina, que forma el elemento óptico difractivo. Al despegar la lámina portadora se crea una oblea de polímero completa con varias DOE y una estructura conductora integrada (véase la figura 6).
Conclusión
Este proceso impresiona por su sencillez y rentabilidad:
- Se pueden utilizar procesos sencillos de impresión UV para producir elementos ópticos miniaturizados como lentes o DOEs con funcionalidades adicionales (por ejemplo, conductores eléctricos o aperturas negras).
- Para ello sólo se necesitan dos materiales: Un material transparente de curado UV para la óptica principal y un material relleno de curado UV o térmico que proporcione la conductividad eléctrica o la propiedad de apantallamiento de la luz.
- Este enfoque también permite superar posibles problemas de fiabilidad (por ejemplo, el desajuste térmico), ya que las propiedades termomecánicas de los dos materiales pueden igualarse.
En DELO encontrará una amplia gama de productos de este tipo. Le ayudaremos a encontrar una solución adecuada para los requisitos específicos de su aplicación individual.