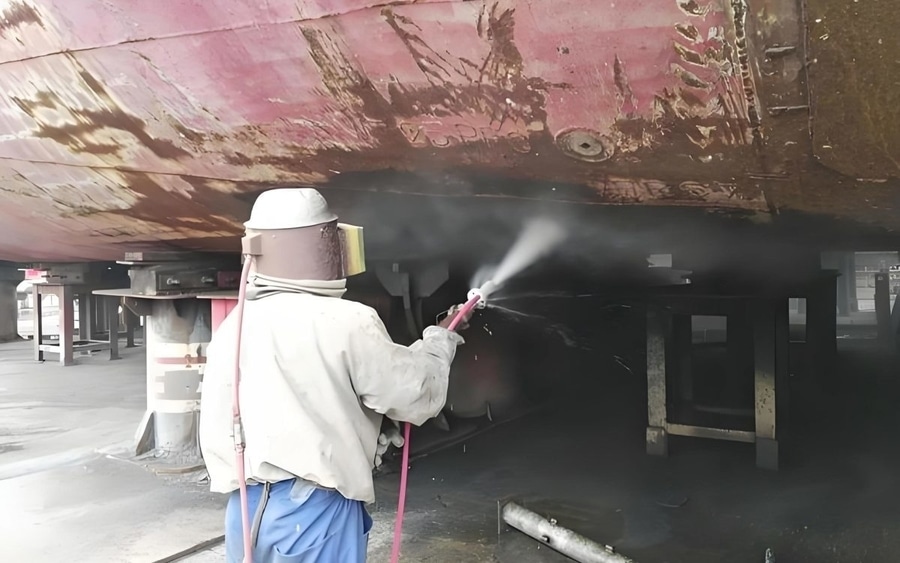
Ver traducción automática
Esta es una traducción automática. Para ver el texto original en inglés haga clic aquí
#Novedades de la industria
¿Un 40% más de eficacia en el chorreado? Puede que esté pasando por alto estos parámetros críticos
Descubra cómo el ajuste preciso de los parámetros puede aumentar drásticamente la productividad, reducir los costes y mejorar la calidad del acabado.
En la industria manufacturera, el chorro de arena es un método de tratamiento de superficies ampliamente utilizado para limpiar, eliminar óxido, dar rugosidad a la superficie y reforzarla. A pesar del uso de equipos de alto rendimiento, muchas empresas siguen sin alcanzar los niveles de producción y calidad esperados. A menudo, la causa no radica en el equipo en sí, sino en una mala configuración de los parámetros.
Este artículo explora los principales parámetros que influyen en la eficacia del chorreado, analiza en profundidad su impacto en el rendimiento y ofrece estrategias prácticas de optimización. Estas ideas pueden ayudar a los fabricantes a mejorar significativamente la productividad y la uniformidad, garantizando al mismo tiempo la estabilidad del equipo.
1. Parámetros básicos que afectan a la eficiencia del chorreado de arena
La eficacia de las operaciones de chorreado de arena viene determinada principalmente por los siguientes parámetros:
1.1 Presión de trabajo
Afecta directamente a la velocidad y la energía cinética de los abrasivos. Es un factor clave tanto para el rendimiento de la limpieza como para la rugosidad de la superficie.
1.2 Tipo y tamaño del abrasivo
Diferentes materiales abrasivos y tamaños de partículas son adecuados para diferentes tareas. Las partículas más grandes ofrecen una mayor fuerza de impacto pero un menor refinamiento superficial.
1.3 Tipo de boquilla y estado de desgaste
El diseño de la boquilla y el nivel de desgaste influyen en la forma y consistencia del chorro abrasivo. Las boquillas desgastadas reducen significativamente la eficiencia operativa.
1.4 Distancia de separación y ángulo de chorro
Una distancia demasiado corta puede dañar la superficie de la pieza; una demasiado larga reduce la eficacia del impacto. El ángulo de proyección debe adaptarse en función de la forma de la pieza y del resultado deseado.
1.5 Caudal de abrasivo
El control preciso del caudal de abrasivo garantiza un equilibrio entre la calidad y el coste operativo.
2. Estrategias de optimización para parámetros clave
2.1 Ajuste de la presión de trabajo
Para una limpieza intensa (por ejemplo, eliminación de óxido), ajuste la presión a 0,5-0,8 MPa.
Para la preparación de superficies de precisión (por ejemplo, precapa), mantenga 0,3-0,5 MPa.
Un estabilizador de presión puede reducir el derroche de energía y la dispersión del abrasivo.
2.2 Selección del abrasivo adecuado
La granalla de acero ofrece fuertes efectos de granallado para piezas metálicas.
Las perlas de vidrio o el óxido de aluminio producen acabados más suaves.
Evite los abrasivos demasiado gruesos que aceleran el desgaste de la boquilla. Sustituya regularmente las partículas de polvo ultrafinas de los abrasivos reciclados.
2.3 Mantenimiento de la boquilla
Utilice boquillas de carburo de boro o carburo de silicio para prolongar su vida útil.
Inspeccionar diariamente el diámetro de la boquilla. Sustitúyalas si el desgaste supera el 10%.
Las boquillas tipo Venturi pueden mejorar la eficacia del chorreado en más de un 40%.
2.4 Optimización de la distancia y el ángulo
Ángulo de chorro recomendado: 45°-75° para una limpieza y decapado óptimos.
Distancia de separación ideal: 100-300 mm para un equilibrio entre impacto y cobertura.
Los sistemas de granallado robotizados o automatizados garantizan la uniformidad y repetibilidad en el procesamiento por lotes.
2.5 Automatización y control inteligente
Los sistemas PLC o las pantallas HMI permiten la supervisión y el ajuste en tiempo real.
Instale sensores inteligentes para controlar el caudal de abrasivo, el desgaste de las boquillas y las condiciones ambientales.
Los sistemas de control de bucle cerrado ayudan a mantener un rendimiento de granallado estable con una intervención manual mínima.
3. Estudio de caso: Mejoras reales gracias a la optimización
Un proveedor de piezas de automoción de primer nivel optimizó la configuración de su equipo de chorreado de arena y observó mejoras notables en la eficacia de la producción y la fiabilidad del equipo:
El tiempo medio de procesamiento por pieza se redujo de 12 a 7 minutos, una mejora del 42%.
El consumo de energía se redujo de 9,2 kWh a 6,5 kWh por hora.
La tasa de defectos superficiales se redujo del 3,1% al 0,7%, lo que mejoró considerablemente la consistencia del producto.
El ciclo de sustitución de boquillas pasó de 10 a 18 días, lo que redujo el tiempo de inactividad y los costes de mantenimiento.
Gracias a la optimización de la presión de trabajo, la selección del abrasivo y el rendimiento de las boquillas, la empresa logró una mejora de más del 40% en la eficiencia del chorreado, al tiempo que reducía significativamente los costes operativos.
4. Conclusión
El rendimiento del chorreado de arena viene determinado no sólo por el diseño físico del equipo, sino también por lo bien que se ajusten e integren sus parámetros. Un enfoque sistemático de la optimización de los parámetros permite a los fabricantes aumentar el rendimiento, reducir el consumo de energía y garantizar una alta calidad del producto.
A medida que avanza la automatización industrial, el chorreado de arena evoluciona hacia operaciones digitalizadas, ecológicas y basadas en la precisión. El ajuste continuo de los parámetros, el mantenimiento proactivo y la integración de sistemas inteligentes son factores clave para mantenerse a la cabeza en el competitivo panorama de la fabricación.
Si desea mejorar el rendimiento de su sistema de arenado o necesita soluciones de optimización personalizadas, nuestros expertos técnicos están aquí para ayudarle. Póngase en contacto con nosotros hoy mismo para recibir asesoramiento personalizado y asistencia técnica.