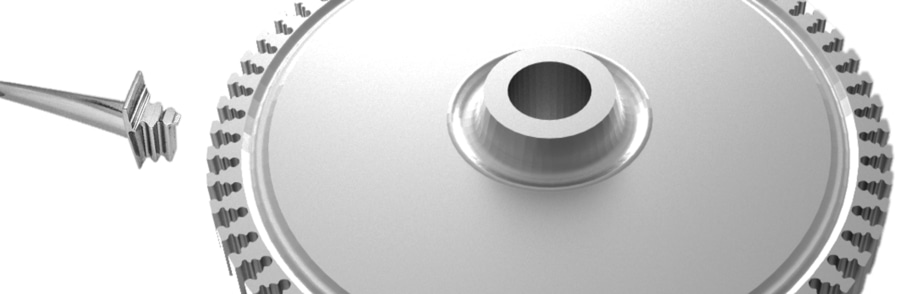
#Tendencias de productos
SEGURO Y REPRODUCIBLE: REDONDEO DE MUESCAS CON FORMA DE ESPINA DE PEZ
DESBARBADO Y REDONDEO DE DISCOS DE TURBINA
MUESCAS CON FORMA DE ESPINA DE PEZ Y PIES DE ÁLABE: LO MÁS IMPORTANTE ES CONSERVAR LA FORMA
Los discos de turbina y de compresor tienen unas ranuras de montaje, conocidas como muescas con forma de espina de pez, en las que se insertan los álabes de la turbina. El brochado, la electroerosión por hilo y el fresado se han consolidado como los métodos de fabricación de estas ranuras de montaje. Durante el proceso se forman rebabas o bordes afilados en la muesca. Para que el montaje pueda llevarse a cabo correctamente y evitar lesiones, los bordes de la ranura y los del pie del álabe deben estar libres de rebabas y tener un radio definido. Solo así es posible garantizar el buen funcionamiento de los componentes. Especialmente las superficies de presión en las que el pie del álabe y el disco están en contacto durante el funcionamiento deben cumplir tolerancias muy ajustadas de entre 10 y 20 µm. Para que los álabes estén perfectamente colocados, es necesario que durante el proceso de desbarbado y redondeo no se produzca ninguna desviación de la forma en dichas superficies.
PRECISIÓN DE REPETICIÓN: POR QUÉ LOS PROCESOS ROBOTIZADOS NO SON LA MEJOR ELECCIÓN
El proceso habitual para este paso es el desbarbado y redondeo mecánico parcialmente robotizado con una muela o un cepillo. Las herramientas empleadas se desgastan con el tiempo, razón por la cual los resultados del mecanizado no se mantienen constantes durante el ciclo de vida de la herramienta. Los bordes afilados, por ejemplo, cortan las puntas del cepillo y producen en él un desgaste difícil de calcular, lo que se traduce en unos resultados muy variables y en una fuerte contaminación del proceso causada por los residuos del cepillo. También las muelas abrasivas sufren un desgaste irregular que debe compensarse con el movimiento del robot. La abrasión hace que se cuelen impurezas en el proceso.
Cuando la geometría de la pieza de mecanizado es compleja, el redondeo suele tener un resultado asimétrico, dado que la muela o el cepillo solo pueden adaptarse hasta cierto punto a la geometría de la muesca con forma de espina de pez o directamente no son capaces de llegar a los lugares de difícil acceso. Esto da lugar a un redondeo asimétrico y de calidad variable que a menudo incumple las tolerancias, produce desviaciones de la forma y, por lo tanto,
acarrea un aumento de los descartes y de los costes.
COMPARACIÓN DE PROCESOS ALTERNATIVOS
En su búsqueda de un proceso alternativo que permitiera obtener unos resultados de mecanizado más convincentes, un fabricante de sistemas de propulsión evaluó junto con OTEC dos tecnologías de rectificado distintas.
El primero de esos métodos, en el que se utilizaba un vibrador de artesa redondo, demostró ser inadecuado para esa aplicación, pues ni siquiera después de varias horas de proceso fue posible mantener las roturas de bordes completamente dentro del rango de tolerancia. En los ensayos realizados, el redondeo conseguido no era simétrico ni tenía una precisión reproducible. Además, el incremento del nivel de ruido y las consiguientes vibraciones resultaron ser un problema, ya que en las inmediaciones se utilizan instrumentos de medición sensibles.
El segundo proceso con la máquina Streamfinish de OTEC obtuvo resultados prometedores en muy poco tiempo desde la primera prueba. Gracias al posicionamiento preciso del componente durante el proceso, bastaron 15 minutos para que todas las roturas de bordes se encontraran dentro del margen de tolerancia, con un redondeo muy simétrico en todo el borde. Los demás ensayos demostraron también la reproducibilidad y estabilidad del proceso. La desviación de la forma en las superficies de presión, inferior a 1 µm, era tan mínima que no fue necesario realizar ningún tipo de ajuste en el proceso de brochado previo. Además, como el proceso apenas produce ruidos y vibraciones, puede llevarse a cabo cerca de equipos de medición sensibles.
ESTAS SON LAS VENTAJAS QUE YA HAN CONVENCIDO A VARIOS FABRICANTES DE SISTEMAS DE PROPULSIÓN:
Tiempo de proceso más corto de apenas 15 minutos.
Redondeo muy simétrico y uniforme.
Resultados seguros y reproducibles.
Eliminación de rebabas sin residuos.
Mínima desviación de la forma en las superficies de presión de la muesca con forma de espina de pez.
Cumplimiento seguro y medible de tolerancias ajustadas inferiores a 1 µm.
Abrasión puramente mecánica: no se utilizan aceleradores químicos.
¿CÓMO FUNCIONA STREAMFINISH?
En el proceso Streamfinish desarrollado por OTEC, los componentes, como los discos de turbina y los álabes de turbina o de compresor, se enganchan en un soporte y se sumergen en un depósito giratorio lleno de producto de rectificado o pulido (médium). Las piezas de mecanizado pueden rotar también o colocarse en un
determinado ángulo dentro de la corriente.
El movimiento relativo que se produce entre el componente y el médium da como resultado un mecanizado homogéneo. Gracias a las enormes fuerzas de mecanizado de hasta 9 toneladas, es posible realizar una abrasión selectiva en menos tiempo que con cualquier otro método de mecanizado de superficies. Según el tamaño, el estado inicial y la preparación del componente (por ejemplo, el biselado de los bordes), pueden conseguirse radios de hasta 700 µm en 15 minutos. Gracias al grano ultrafino del médium, este proceso de redondeo vale también para geometrías complejas y de difícil acceso.
OTEC es la única empresa que ofrece máquinas Streamfinish con sistema automatizado integrado para componentes grandes y pesados. El nuevo modelo SF-HP es adecuado para piezas de hasta 650 mm de diámetro y hasta 200 kg
de peso.
DEFINICIÓN DEL PROCESO CON LOS EXPERTOS DE OTEC PRÄZISIONSFINISH
La tecnología Streamfinish de OTEC también es perfecta para los componentes que exigen un mecanizado posterior igual de preciso, como álabes de turbina y de compresor, pies de álabe, blisks, servoválvulas, ruedas dentadas, tuercas de bolas circulantes o componentes de chasis. Independientemente de la geometría y de los requisitos de calidad superficial o de redondeo, el equipo de expertos del OTEC Finishing Center le ayudará a definir el proceso. Juntos encontraremos el proceso adecuado para sus componentes. Pida cita ahora para asistir en persona o por internet al mecanizado de sus componentes.
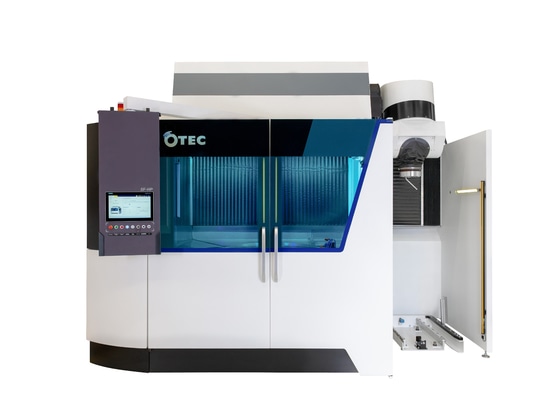
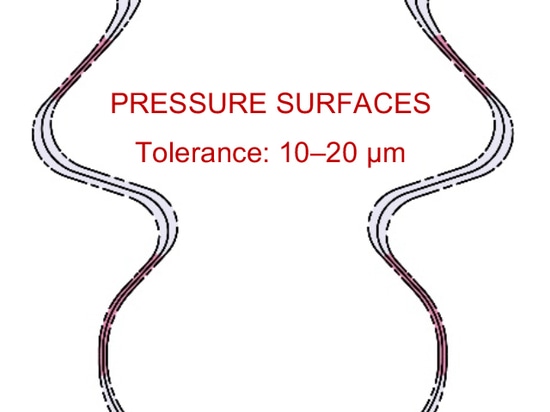