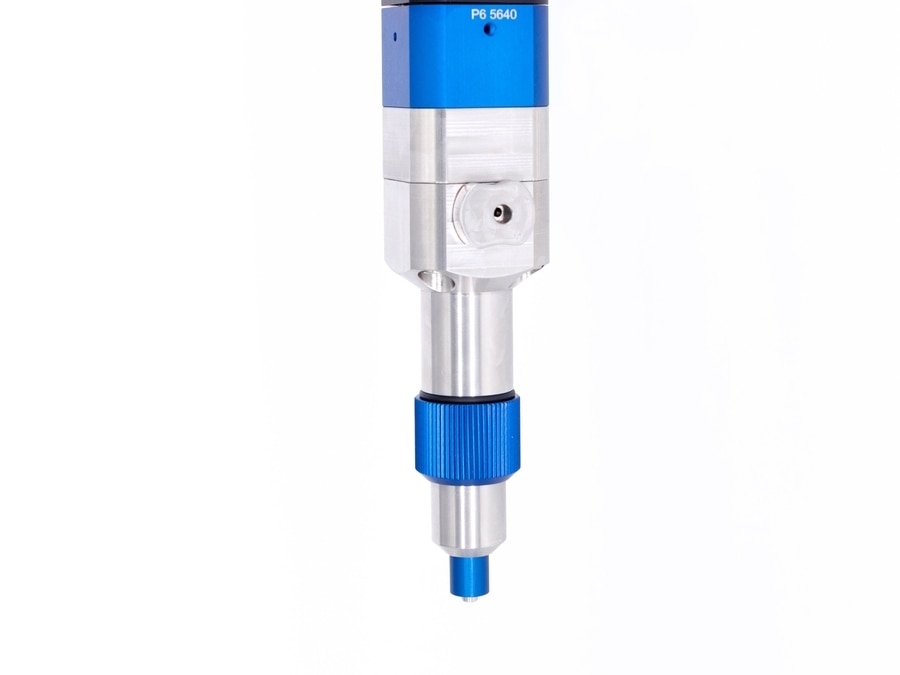
Ver traducción automática
Esta es una traducción automática. Para ver el texto original en inglés haga clic aquí
#Novedades de la industria
Un proveedor de automoción sustituye las bombas de pistón por surtidores y reduce considerablemente los costes de mantenimiento
Los requisitos de los clientes se han multiplicado por cuatro
Introducción
Los costes de servicio y mantenimiento son fundamentales para reducir el coste total de propiedad de la maquinaria de producción, y no sólo en los procesos de alto rendimiento. En este contexto, la filial estadounidense de un conocido proveedor automovilístico alemán preguntó recientemente a preeflow. La empresa utiliza un lubricante de extrema presión para proteger los componentes contra la corrosión y el agarrotamiento. Cada proceso de lubricación suministra 100 mg de lubricante directamente desde un dosificador y con ayuda de bombas de pistón. El proceso de dispensación en sí dura 1,4 segundos. Los siguientes 100 mg de lubricante se dispensan tras una pausa de 4 segundos. El resultado es un tiempo de funcionamiento diario de aproximadamente 21,75 horas los días laborables y de 11 horas los sábados y domingos, con sus periodos de funcionamiento reducidos.
El problema: costes de mantenimiento demasiado elevados
La presión de funcionamiento de 40 bares debe ajustarse a la baja antes de la dispensación, y esto se ha identificado como un punto neurálgico en el proceso. En este punto se produce aglomeración debido a la separación del aceite y las partículas. Como resultado, el lubricante -que ya es extremadamente abrasivo debido a su alta densidad de partículas- presenta un alto riesgo de causar desgaste, así como de atascar los dosificadores.
Estos dos factores hacen necesaria la sustitución completa de todas las válvulas cada 4 semanas, con un coste de unos 1.000 dólares por válvula. Extrapolado a 30 líneas que funcionan en paralelo, eso supone 360.000 dólares al año fiscal. La empresa se propuso reducir ese coste excesivo y vio la posibilidad de hacerlo modificando técnicamente el sistema de dispensación.
Del campo al laboratorio: Disposición de las pruebas y ajustes técnicos
El equipo de preeflow dirigido por Tobias Unger recibió el encargo de realizar una serie de pruebas para evaluar si podían ejecutarse entre 228.000 y 230.000 ciclos de dispensación en un periodo de 30 días. La restricción clave era que sólo se permitían variaciones de cantidad de 50 mg mín./máx.
Además, se acordó que se proporcionarían declaraciones específicas y pruebas de imagen sobre los efectos del lubricante abrasivo en los componentes de preflujo.
Las pruebas se realizaron con tres eco-PEN600 con rotores revestidos de CC + VisLas y utilizando dos eco-Control EC200 2.0. El software se actualizó para poder registrar y exportar los datos del motor. También se instaló un flowplus-MONITOR QC.
No se disponía de datos sobre la viscosidad del producto Regular Grade Anti-Seize & Lubricating Compound sometido a prueba. Antes de las pruebas se facilitaron datos sobre el aceite utilizado y los rellenos de grafito, escamas de cobre, polvo de aluminio y óxido de zinc.
Las pruebas se realizaron en un banco de pruebas dispuesto en forma de T. En primer lugar, el material de ensayo se transfirió a recipientes diferentes, ya que los que se habían entregado estaban deformados. Los dosificadores, dispuestos en forma de T, se conectaron a las unidades de control de la izquierda y la derecha según su disposición y funcionaron en modo 2N (sincronización). El surtidor central estaba conectado a una unidad de control, que funcionaba en modo de surtidor único (1N). Los tres dispensadores estaban conectados centralmente al MT-XS. El sistema se calibró para una densidad supuesta de 1,24 g/cm³.
La producción media de los primeros 10 disparos de dispensación después de la calibración fue de 0,100 g cada uno en los dispensadores izquierdo y central, y de 0,099 g en el dispensador derecho. El lubricante se dispensó por cantidad, y a una velocidad definida de 3,750 g/min, correspondiente a un tiempo de dispensación de 1,6 segundos. La pausa entre disparos fue de 0,4 segundos.
Resultados prometedores
Tras 230.000 disparos, a pesar de las propiedades abrasivas de la sustancia de ensayo, los diámetros internos de los dosificadores apenas variaron de forma apreciable, como muestra la figura 1. El dispensador izquierdo toma ahora 0,107 g de material en lugar de 0,100 g; el dispensador central 0,103 g en lugar de 0,100 g; y el dispensador derecho 0,108 g en lugar de 0,099 g iniciales. De estas pequeñas diferencias se deduce que el medio abrasivo sólo tiene una influencia insignificante en la calidad del material, incluso con un número muy elevado de disparos únicos.
La prueba continuó con fines de investigación tras alcanzar el objetivo del cliente (230.000 disparos de dispensación). El equipo de preeflow esperaba que esto proporcionara datos concretos sobre la duración de la serie de pruebas hasta el fallo total del sistema. ¿Cuándo se producen las fugas? ¿Cuándo cae la presión de dispensación? Preguntas como éstas quedaron sin respuesta, incluso después de 1.000.0000 disparos de dispensación, ya que no se pudieron medir cambios significativos (figura 2). Incluso el desgaste visible causado por el lubricante abrasivo de alta presión se mantuvo dentro de los límites (izquierda ahora 0,106; centro 0,114; derecha 0,106). La inspección visual final también mostró que todos los rotores estaban en excelentes condiciones. Los estatores mostraban únicamente el desgaste esperado, que en cualquier caso no se desviaba significativamente del original, con una media del 3% (diámetro exterior) y el 8%, respectivamente.
Conclusión
Estos valores demuestran que los 230.000 disparos de dosificación exigidos por el cliente pueden superarse muchas veces, y aun así, no se aprecian signos de avería en condiciones de laboratorio.
De este modo, el cambio de las bombas de émbolo a la eco-PEN600 garantiza al cliente un ahorro demostrable, ya que gracias al largo tiempo de dosificación ya no es necesario sustituir las válvulas cada 4 semanas. Además, los costes de mantenimiento de la eco-PEN600 se reducen aún más, incluso en el uso a largo plazo, ya que se ha demostrado que los rotores con revestimiento de CC no se desgastan, y las variaciones de la cantidad de dispensación en una sola toma son insignificantes en vista de su bajo valor (máx. más → 18,9 mg / máx. menos → 7,3 mg). Todo el equipo -empezando por el dispensador- presentaba cero fugas. No se pudo detectar ninguna sustancia que contuviera aceite ni allí ni en las tuberías y accesorios. Tampoco se detectaron defectos de calidad debidos a diferencias de viscosidad. Cabe suponer que la recalibración puede aumentar los 1.000.000 de disparos de dispensación alcanzados con una calidad comparable y sin fatiga del material.