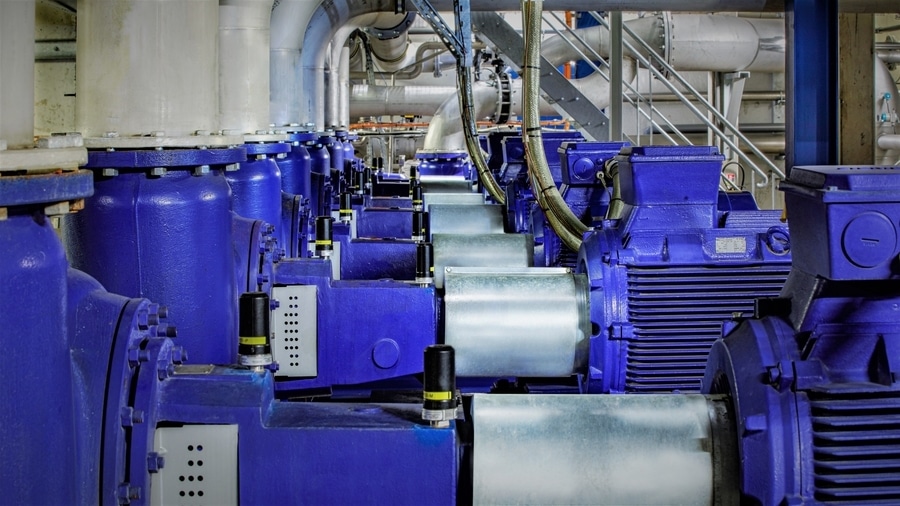
#Tendencias de productos
Los activos mecánicos aprenden a hablar
Del Mantenimiento Preventivo al Predictivo
El monitoreo continuo de la condición de la máquina puede hacer que las operaciones sean más seguras y eficientes. Especialmente para los componentes críticos, el mantenimiento basado en la condición o incluso predictivo es el método de elección hoy en día: los equipos modernos e inteligentes transmiten los parámetros de condición relevantes a los sistemas de gestión de mantenimiento de nivel superior. Pero, ¿qué pasa con los activos más antiguos sin capacidades de diagnóstico? Aquí, una combinación bien diseñada de sensores IIoT, unidades de puerta de enlace y servicios en la nube ofrece una solución de actualización ideal. En un centro de fabricación de análisis e instrumentación de procesos, este paquete demuestra ser extremadamente rentable y versátil.
Durante décadas, los equipos de mantenimiento en las plantas de proceso y fabricación se han esforzado por aumentar la productividad general de la planta. Un elemento clave de este esfuerzo es el desarrollo e implementación de estrategias de mantenimiento efectivas. Se ha demostrado durante mucho tiempo que el enfoque tradicional de hacer funcionar el equipo hasta que falle (conocido como "ejecutar hasta que falle") es ineficiente y costoso. Un paso importante en el desarrollo de estrategias de mantenimiento más eficaces ha sido la introducción del mantenimiento preventivo (PM). Esto se refiere a las actividades de inspección y mantenimiento de rutina que se realizan de acuerdo con programas definidos. Sin embargo, mientras PM ayuda a prevenir fallas inesperadas, también resulta en un mantenimiento innecesario cuando el equipo está en buenas condiciones.
El siguiente paso en el desarrollo de estrategias de mantenimiento eficientes es el mantenimiento predictivo (PdM). Esto implica recopilar y analizar datos sobre el estado del equipo para predecir cuándo se puede requerir mantenimiento. El objetivo es realizar el mantenimiento cuando sea necesario, en función de la condición real del equipo en lugar de un programa establecido. Un aspecto clave de PdM es el monitoreo basado en condiciones (CBM), el monitoreo y análisis continuos de la condición del equipo durante la operación normal. La implementación exitosa del mantenimiento basado en la condición requiere una serie de tecnologías y recursos, incluidos sensores adecuados, sistemas de transmisión y procesamiento de datos y software de análisis especializado. Sin estos recursos, es imposible realizar el mantenimiento en función de las condiciones actuales de la máquina. Ahora es posible adaptar dichas tecnologías a bajo costo para equipos rotativos o vibratorios, como lo ilustra el siguiente ejemplo.
Experiencia en la fabricación de caudalímetros
La fábrica de Siemens en Haguenau, Francia, que celebró su 50 aniversario en 2020, emplea a más de 800 personas. Especializada en la producción de transmisores de presión, caudalímetros y analizadores de gases, la planta ha sido reconocida por su enfoque innovador hacia la transformación digital: desde 2015, la instalación ha optimizado continuamente su producción a través de la automatización, la robótica y la digitalización. Los procesos de producción ahora pueden simularse en tiempo real y hacerse más eficientes.
Aquí, Robert Gerber coordina el mantenimiento, mientras que su colega David Uhrig es responsable como planificador de servicios. “En términos de mantenimiento, hemos logrado grandes avances en los últimos años”, dice Uhrig, quien ha trabajado en la planta de Haguenau desde 1995, primero como técnico de mantenimiento y luego como planificador de mantenimiento: “Nuestros equipos de mantenimiento ayudan a garantizar que la eficiencia de las plantas mejora año tras año. Supervisamos el equipo de producción las 24 horas del día y ahora nos beneficiamos de las capacidades de diagnóstico que el equipo no tenía hace algunos años. Las estrategias de mantenimiento varían de una sección de planta a otra”, como informa Gerber: “Creo que se podría decir que estamos en el área de tensión entre querer hacerlo y poder hacerlo a diario: por un lado, sabemos a partir de los análisis de criticidad qué partes de la planta tienen qué efectos en el rendimiento operativo en caso de falla, y a qué debemos prestar especial atención. Por otro lado, no podemos desarrollar estrategias de mantenimiento predictivo para todos los activos porque carecemos de los datos de condición”.
Las piezas de repuesto están disponibles para la mayoría de los equipos críticos, pero eso no es suficiente para evitar el tiempo de inactividad: “Tome como ejemplo nuestro autoclave”, explica Gerber: “Todos los caudalímetros tienen un revestimiento interior especial que se vulcaniza en el autoclave. Si falla, la producción se detiene. El motor del soplador del autoclave es fundamental, por lo que lo mantenemos en stock. El problema con una falla repentina es que la rueda del ventilador está montada en el eje del motor sin acoplamiento. Se necesitan dos días de trabajo y el uso de especialistas, a pesar de que tenemos el repuesto en stock”.
Monitoreo basado en condiciones para reequipamiento
Los dos especialistas en mantenimiento querían una opción de monitoreo basado en la condición para este motor y encontraron lo que estaban buscando internamente: Sitrans Smart Condition Monitoring IQ (SCM IQ), desarrollado por Siemens AG, es un sistema inteligente para el monitoreo y mantenimiento continuos de componentes de máquinas giratorias o vibratorias. Utiliza una combinación de sensores IIoT e inteligencia artificial para registrar y analizar continuamente datos de vibración y temperatura.