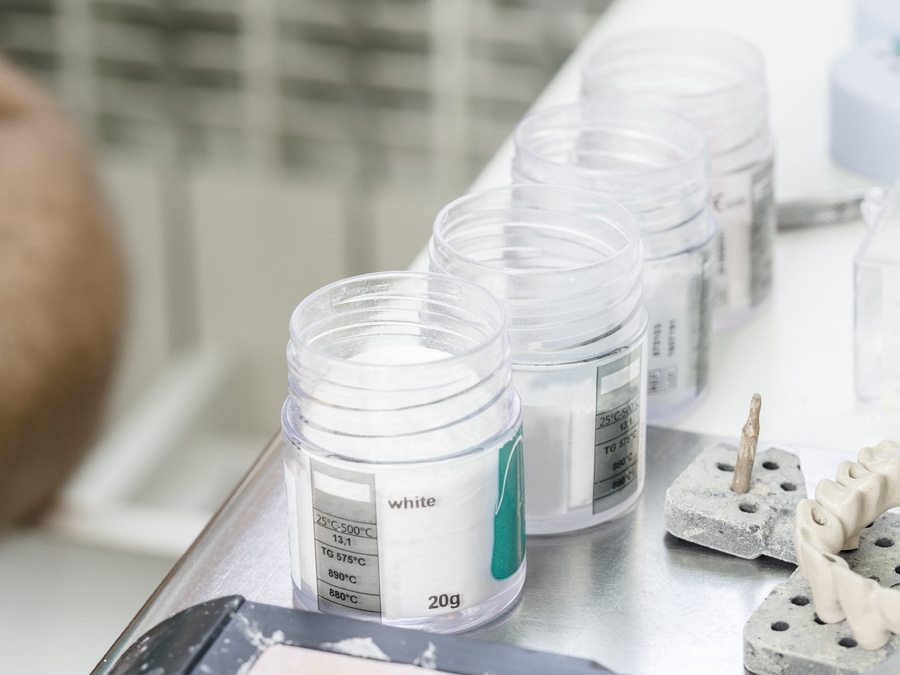
Ver traducción automática
Esta es una traducción automática. Para ver el texto original en inglés haga clic aquí
#Novedades de la industria
Las mezcladoras verticales preparan cerámicas de alto rendimiento
En la producción de cerámica técnica hay muchos paralelismos con la pulvimetalurgia. Las materias primas utilizadas son caras. Se trata de óxidos, nitruros, carburos o boruros de metales de gran pureza.
Junto con los plásticos, se considera que los materiales cerámicos tienen el mayor potencial de desarrollo por su estabilidad, resistencia a la temperatura y durabilidad únicas. La cerámica de ingeniería se utiliza como material resistente a altas temperaturas en la generación de energía, como protección contra la corrosión, el ácido y el desgaste en la ingeniería de aparatos, y como semiconductor de alta frecuencia en la ingeniería de comunicaciones.
En la producción de cerámica técnica hay muchos paralelismos con la pulvimetalurgia. Las materias primas utilizadas son caras. Se trata de óxidos, nitruros, carburos o boruros de metales de gran pureza. Algunos ejemplos son el óxido de aluminio, el titanato de aluminio, el carburo de silicio, el nitruro de silicio y el óxido de circonio. Debido a su fragilidad, los componentes cerámicos son propensos al "fallo crítico". Por ello, en la fabricación de cerámicas avanzadas debe garantizarse el máximo grado de pureza.
La cerámica tiene propiedades únicas
La cerámica tiene unas propiedades específicas únicas que ningún otro grupo de materiales puede igualar: resistencia extrema, alta resistencia al calor, resistencia a los ácidos, ductilidad, conductividad eléctrica y térmica, aislamiento eléctrico, refracción óptica, transparencia, profundidad de color, etc.
Los polvos cerámicos se preparan con sumo cuidado. En algunos casos, los componentes de partida se convierten a un estado con una superficie específica extremadamente alta. El tamaño de las partículas es inferior a 0,01 µm. Este tipo de reducción del tamaño de las partículas requiere un elevado aporte de energía.
Estas partículas tan pequeñas tienden a aglomerarse espontáneamente. Los aglomerados deben separarse (desaglomerarse) de nuevo en partículas primarias para garantizar una microestructura uniforme del material sinterizado. La cadena del proceso es larga: Extracción de la materia prima de la industria química, ampliación de la superficie definida, descomposición química, tamizado, dopaje, homogeneización, dispersión en la fase húmeda, separación sólido-líquido hasta el secado térmico, homogeneización/mezcla. La difusión del material tiene lugar a altas temperaturas de sinterización en el horno de calcinación. El enfriamiento completa el primer paso de la síntesis. A ésta le siguen fases de preparación similares o diferentes, que comienzan de nuevo con la molienda y la mezcla. Si el compuesto contiene polímeros plásticos, las reacciones de síntesis pueden tener lugar en seco, húmedo y gaseoso en el mezclador amixon®.
Muchos lotes pequeños se homogeneizan en un lote grande
La mayoría de los procesos tienen lugar en equipos de proceso de funcionamiento continuo, cuyos ajustes de parámetros deben determinarse a partir de análisis de sustancias previos. En este sentido, los pasos individuales continuos deben realizarse por secciones y los productos intermedios recogerse como lotes en contenedores, silos, mezcladoras o big bags. Para los análisis representativos, debe suponerse una masa total homogénea. Los tamaños de los lotes a homogeneizar en pulvimetalurgia varían entre 5 l y 20 000 l. Las mezcladoras amixon® se utilizan con éxito para conseguir calidades de mezcla ideales. El flujo de circulación tridimensional garantiza tiempos de mezcla cortos.
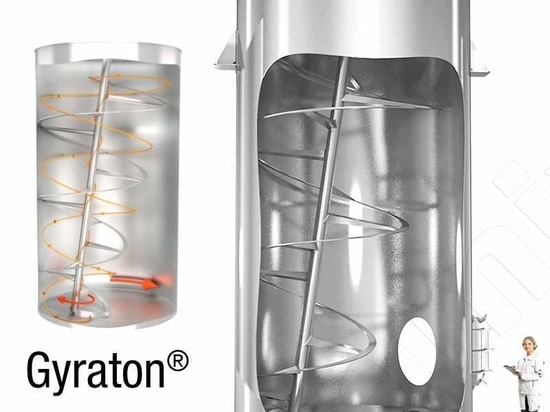