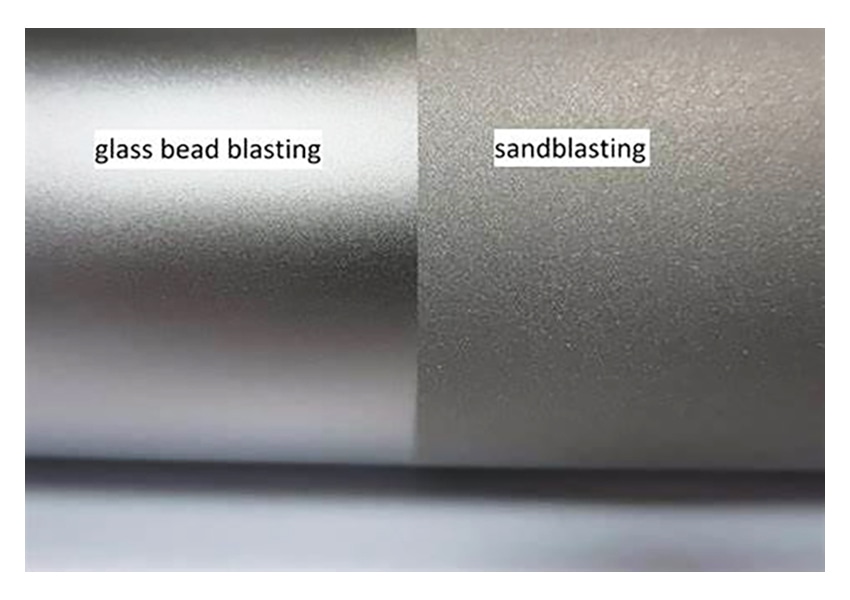
Ver traducción automática
Esta es una traducción automática. Para ver el texto original en inglés haga clic aquí
#Novedades de la industria
Comparación del chorro de arena y el granallado: ¿Cuál es la mejor opción para su aplicación?
Elección del método de chorreado óptimo para la preparación y el acabado de superficies
1. Introducción
El tratamiento de superficies es un paso crucial en la fabricación, restauración y mantenimiento en diversas industrias. Entre las técnicas abrasivas más utilizadas se encuentran el chorro de arena y el granallado. Aunque ambos métodos implican el uso de abrasivos de alta velocidad para limpiar, preparar o dar acabado a las superficies, difieren significativamente en términos de aplicación, tipo de abrasivo, impacto en los materiales y resultados finales. Comprender estas diferencias es esencial para seleccionar el método adecuado a sus necesidades específicas.
Este artículo profundiza en los principios, ventajas, limitaciones y aplicaciones ideales del chorro de arena y el granallado, y ofrece información sobre qué método se adapta mejor a sus necesidades.
2. Qué es el chorreado de arena
2.1 ¿Qué es el chorro de arena?
El arenado, también conocido como chorreado abrasivo, es un proceso de tratamiento de superficies que consiste en propulsar partículas abrasivas a gran velocidad sobre una superficie. El proceso elimina el óxido, la pintura, las incrustaciones y los contaminantes, a la vez que prepara las superficies para el revestimiento o el repintado.
2.2 Tipos de abrasivos
Tradicionalmente, la arena de sílice se utilizaba como medio principal de chorreado. Sin embargo, debido a los riesgos para la salud asociados a la inhalación de polvo de sílice, ahora se prefieren medios alternativos como el óxido de aluminio, la granalla de acero, el granate y el vidrio triturado. La elección del medio afecta a la agresividad del proceso de chorreado.
2.3 Ventajas del chorro de arena
Eliminación eficaz de materiales: Ideal para eliminar recubrimientos resistentes, corrosión y contaminantes.
Amplia gama de aplicaciones: Adecuado para metales, hormigón, madera y algunos plásticos.
Alta eficacia: Limpia rápidamente grandes superficies con una fuerte abrasión.
Perfilado de superficies: Crea patrones de anclaje que mejoran la adherencia de los revestimientos.
2.4 Limitaciones del chorro de arena
Agresividad: Puede dañar materiales más blandos y crear rugosidades en la superficie.
Polvo y riesgos para la salud: Requiere ventilación adecuada y equipo de protección.
Posible deformación: El chorreado a alta presión sobre metales finos puede causar deformaciones.
3. Entender el chorreado con microesferas
3.1 ¿Qué es el chorreado de microesferas?
El chorreado con microesferas es un proceso abrasivo más suave que utiliza medios esféricos, como microesferas de vidrio o de cerámica, para conseguir un acabado de superficie liso, pulido y uniforme. A diferencia del chorro de arena, que elimina material de forma agresiva, el chorreado con microesferas limpia y mejora principalmente el aspecto de una superficie sin un desgaste excesivo.
3.2 Tipos de Granalla
Microesferas de vidrio: Proporcionan un acabado satinado o mate, ideal para superficies delicadas.
Perlas de cerámica: Más duras y resistentes, se utilizan para aplicaciones de precisión.
Microesferas de plástico: Utilizadas para materiales más blandos como el aluminio y los compuestos.
3.3 Ventajas del granallado con microesferas
No daña las superficies: Adecuado para componentes frágiles e intrincados.
Mejora el aspecto estético: Produce un acabado limpio, uniforme y refinado.
Mejora la resistencia a la fatiga: Introduce tensión de compresión, reduciendo el riesgo de grietas.
Respetuoso con el medio ambiente: Menor producción de polvo en comparación con el chorro de arena.
3.4 Limitaciones del Granallado
Eliminación limitada de material: No es efectivo para óxido pesado o recubrimientos gruesos.
Proceso más lento: Requiere más tiempo de limpieza que el chorro de arena.
Mayor coste: Los abrasivos para granallado pueden ser más caros que los abrasivos tradicionales.
4. Elección del método adecuado para su aplicación
4.1 Consideraciones clave
Material: El arenado es adecuado para metales duros, hormigón y madera, mientras que el granallado es ideal para metales blandos, plásticos y piezas delicadas.
Impacto en la superficie: El chorro de arena crea una textura áspera con alta abrasión, mientras que el granallado da como resultado un acabado liso con mínima eliminación de material.
Preparación del revestimiento: El chorreado con arena crea eficazmente patrones de anclaje para los revestimientos, mientras que el granallado es más adecuado para el pulido final.
Eficiencia: El chorreado con arena es rápido y agresivo en la eliminación de material, mientras que el granallado es más lento pero ofrece un acabado más controlado.
Coste: El chorreado con arena tiene un menor coste de material pero requiere más limpieza, mientras que el chorreado con microesferas tiene un mayor coste de material pero produce menos polvo y residuos.
Aplicación: El chorro de arena es el mejor método para eliminar óxido, decapar pintura y texturizar superficies, mientras que el granallado es preferible para el acabado estético y la limpieza de piezas delicadas.
4.2 Mejores aplicaciones para cada método
Utilice el chorro de arena cuando:
Eliminar óxido pesado, pintura vieja o revestimientos gruesos.
Preparar superficies para revestimientos y adhesivos industriales.
Limpieza de acero estructural, hormigón o piezas de maquinaria.
Texturizar superficies para mejorar el agarre.
Utilice el granallado cuando:
Acabado de componentes de precisión con mínima pérdida de material.
Limpieza de piezas delicadas en las industrias aeroespacial, médica o electrónica.
Conseguir un acabado pulido o satinado en metales como el acero inoxidable o el aluminio.
Reducir la tensión superficial en aplicaciones sensibles a la fatiga.
5. Conclusión
Tanto el chorro de arena como el granallado son métodos de tratamiento de superficies muy eficaces, cada uno con ventajas distintas y aplicaciones ideales. El chorreado de arena destaca en la eliminación agresiva de material y la preparación de superficies, por lo que es adecuado para tareas industriales duras. Por otro lado, el granallado es la opción preferida para aplicaciones que requieren acabados suaves, un impacto mínimo sobre el material y un mayor atractivo estético.
Al conocer los puntos fuertes y las limitaciones de cada técnica, los fabricantes y profesionales pueden tomar decisiones informadas para optimizar los procesos de tratamiento de superficies, mejorar la calidad del producto y aumentar la eficacia operativa. El método de granallado adecuado depende de las necesidades específicas de su aplicación, las propiedades del material y la calidad de acabado deseada.