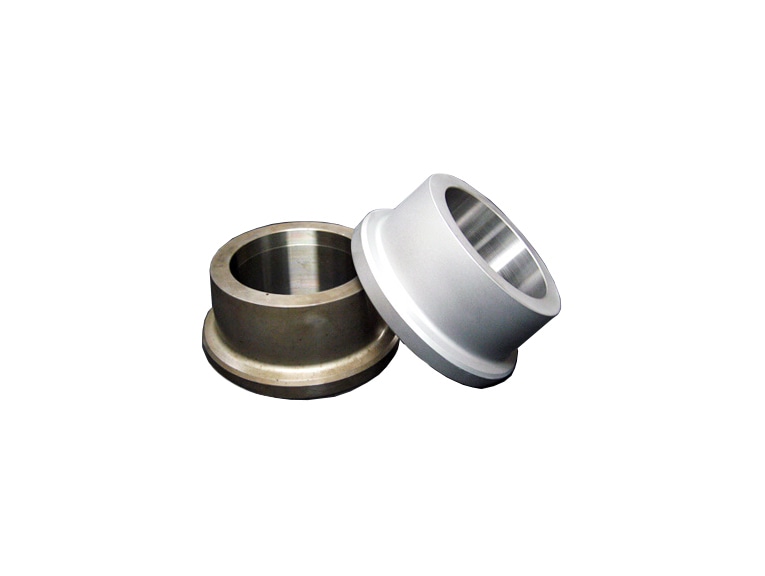
Ver traducción automática
Esta es una traducción automática. Para ver el texto original en inglés haga clic aquí
#Novedades de la industria
Cómo determinan los distintos tipos de microesferas cerámicas los parámetros industriales de rugosidad superficial
Cómo influyen los tipos de microesferas cerámicas en la calidad superficial y la precisión de las aplicaciones industriales
Prólogo
En la moderna tecnología industrial de tratamiento de superficies, el granallado con microesferas cerámicas se ha convertido en un proceso clave para conseguir unas características superficiales precisas. La rugosidad superficial, como parámetro central, afecta directamente al coeficiente de fricción de un producto, a la adherencia del recubrimiento, a las propiedades ópticas y a la vida útil. Este artículo explorará en profundidad los mecanismos de influencia de los distintos tipos de microesferas cerámicas en la rugosidad superficial de las piezas de trabajo y sus estrategias de selección de aplicaciones en la fabricación de precisión.
1. Propiedades del material de las microesferas cerámicas y su relación con la rugosidad superficial
1.1 Principales tipos de microesferas cerámicas y sus propiedades físicas
Granos cerámicos de alúmina (Al₂O₃)
Dureza: Dureza Mohs 8,5-9,0
Densidad: 3.6-3,9 g/cm³
Gama de tamaños de partículas: Normalmente 0,1-3,0 mm
Características: Alta dureza, densidad media, con propiedades de fractura relativamente agudas
Perlas de cerámica de circonio (ZrO₂)
Dureza: Dureza Mohs 8,0-8,5
Densidad: 5,4-6,0 g/cm³
Gama de tamaños de partículas: Normalmente 0,1-2,5 mm
Características: Alta densidad, excelente resistencia al desgaste, alta esfericidad después del tratamiento superficial
perlas de óxido de circonio estabilizado con itria (YZ)
Dureza: Dureza Mohs 8,5-9,0
Densidad: 6,0-6,1 g/cm³
Gama de tamaños de partículas: Normalmente 0,05-2,0 mm
Características: Densidad ultra alta, excelente tenacidad y resistencia al desgaste, máxima esfericidad
Perlas de cerámica de circón (ZrSiO₄)
Dureza: Dureza Mohs 7,5-8,0
Densidad: 4.1-4,7 g/cm³
Gama de tamaños de partículas: Normalmente 0,1-2,5 mm
Características: Dureza y densidad medias, precio más bajo
1.2 Sistema de parámetros de rugosidad superficial
La medición precisa de la rugosidad superficial se basa en el análisis multiparamétrico:
Valor Ra: Rugosidad media aritmética, el parámetro de rugosidad más utilizado
Valor Rz: Altura máxima del perfil, un indicador para evaluar la altura pico-valle de la superficie
Valor Rq: Rugosidad media cuadrática, más sensible a los valores extremos
Valor RSm: Separación media de las irregularidades del perfil, caracteriza la periodicidad de la textura superficial
Valor Rt: Altura máxima del perfil, caracteriza los rasgos extremos de la superficie
2. Mecanismos de influencia de diferentes microesferas cerámicas en la rugosidad superficial
2.1 Factor de dureza del material
La relación de dureza entre las microesferas cerámicas y el material de la pieza determina el mecanismo de microdeformación de la superficie:
Relación de dureza >1,5: Dominado por corte y raspado, produciendo valores Ra más altos y valores RSm más pequeños
Relación de dureza 1,0-1,5: Dominado por la deformación plástica, formando valores Ra más bajos y valores RSm más grandes
Relación de dureza <1,0: Predominio de la compactación superficial, que modifica principalmente los valores Rq en lugar de los valores Ra
Los datos experimentales muestran que cuando las perlas de alúmina tratan aleaciones de aluminio, los valores Ra pueden alcanzar 1,8-2,5μm; mientras que utilizando perlas de circonio estabilizadas con itria con los mismos parámetros de proceso para tratar el mismo material, los valores Ra suelen ser de 1,2-1,8μm.
2.2 Densidad y transferencia de energía de impacto
La densidad de las microesferas cerámicas afecta directamente a la eficacia de la transferencia de energía de impacto:
Las microesferas cerámicas de alta densidad (como las de óxido de circonio estabilizado con itria) pueden transferir mayor energía cinética a la misma velocidad
Las diferencias en la energía cinética dan lugar a diferentes profundidades de microdeformación, lo que afecta a los valores de Rz
Las investigaciones demuestran que por cada aumento de 1 g/cm³ en la densidad, en las mismas condiciones de presión y velocidad, los valores Rz aumentan una media del 15-20%.
2.3 Distribución y uniformidad del tamaño de los granos
La distribución del tamaño de las microesferas afecta directamente a la uniformidad de la microtopografía superficial:
Los tamaños de microesferas de distribución estrecha producen texturas superficiales más uniformes, con pequeñas fluctuaciones de RSm
Las microesferas de distribución ancha producen mayores fluctuaciones de RSm tras el tratamiento, pero contribuyen a aumentar la densidad de las micropisuras superficiales
Las microesferas de tamaño único son más adecuadas para el tratamiento óptico de precisión de superficies, con fluctuaciones del valor Ra controlables dentro de un rango de ±0,05μm
2.4 Morfología de las microesferas y topografía de la superficie
La esfericidad de las microesferas influye decisivamente en la microtopografía de la superficie:
Una esfericidad elevada (como las perlas de circonio estabilizado con itria, esfericidad >0,95) produce texturas de picaduras uniformes en forma de puntos
Una esfericidad baja (como algunas perlas de alúmina, esfericidad <0,90) tiende a producir arañazos irregulares y texturas direccionales
Las diferencias de esfericidad provocan cambios en las relaciones Ra/Rz, lo que afecta a la posterior adherencia del revestimiento
3. Estrategias de selección de microesferas cerámicas en diferentes aplicaciones industriales
3.1 Componentes de precisión aeroespaciales
El sector aeroespacial requiere un control estricto de la rugosidad superficial para garantizar la resistencia a la fatiga y el rendimiento del revestimiento:
Material preferido: Perlas de circonio estabilizado con itria
Tamaño de partícula requerido: 0.1-0,3 mm, distribución estrecha
Valor Ra objetivo: 0,8-1,5μm
Estrategia de tratamiento: Tratamiento en varias etapas, primero partículas grandes y después partículas pequeñas para el acabado fino
Caso práctico: Un álabe de turbina de cierto motor tratado con microesferas de circonio estabilizado con itria de 0,2 mm mostró un aumento del 28% en la resistencia a la fatiga y una prolongación del 35% en la vida útil del revestimiento
3.2 Implantes médicos
Los implantes médicos requieren una rugosidad superficial específica para favorecer la integración ósea o inhibir el crecimiento bacteriano:
Material preferido: Perlas de alúmina o circonio de gran pureza
Tamaño de partícula requerido: 0.05-0,15 mm
Valor Ra objetivo: Normalmente 1,2-2,0μm para implantes de titanio
Requisitos especiales: Los medios de tratamiento deben cumplir las normas de biocompatibilidad USP Clase VI o ISO 10993
Estudio de caso: Los implantes de cadera tratados con perlas de alúmina de 0,1 mm mostraron una integración ósea un 42% más rápida en comparación con las superficies mecanizadas mecánicamente
3.3 Componentes ópticos de precisión
Los componentes ópticos requieren propiedades de dispersión y rugosidad superficial controladas con precisión:
Material preferido: Perlas de circonio estabilizado con itria de esfericidad ultra alta
Tamaño de partícula requerido: 0.03-0,1 mm, distribución extremadamente estrecha
Valor Ra objetivo: 0,05-0,5μm
Estrategia de procesamiento: Baja presión, control de alta precisión, normalmente se lleva a cabo en entornos sin polvo
Ejemplo de aplicación: Los espejos de reflexión láser tratados con perlas de circonio estabilizadas con itria de 0,05 mm mostraron una reducción del 65% en la pérdida por dispersión, manteniendo la precisión de la forma de la superficie
3.4 Componentes de motores de automoción
Las piezas de automoción requieren una retención de aceite y una resistencia al desgaste equilibradas:
Material preferido: Perlas de alúmina o perlas de circón
Tamaño de partícula requerido: 0.3-0,7 mm
Relación Ra/Rz deseada: 0,12-0,15 (esta relación optimiza la retención de la película de aceite)
Caso de aplicación: Los bloques de cilindros de automóviles tratados con perlas de alúmina de 0,5 mm mostraron una reducción del 2,8% en el consumo de aceite y un período de rodaje un 40% más corto
4. Optimización de los parámetros del proceso para un control preciso de la rugosidad superficial
4.1 Parámetros clave del proceso
Los siguientes parámetros afectan directamente a la rugosidad superficial:
Presión de chorreado: Típicamente en el rango de 0.2-0.8MPa, cada incremento de 0.1MPa en la presión resulta en un incremento promedio de 8-12% en el valor Ra
Distancia de chorreado: Típicamente en el rango de 50-200mm, cada incremento de 10mm en la distancia resulta en una disminución media del 3-5% en el valor Ra
Ángulo de chorreado: Afecta a la direccionalidad de la topografía de la superficie, un ángulo de 90° consigue la superficie más uniforme, un ángulo de 45° consigue una textura direccional
Tiempo de tratamiento: La rugosidad superficial crece de forma no lineal con el tiempo de tratamiento, normalmente hay un punto crítico de saturación
Densidad de flujo de microesferas: Número de impactos por centímetro cuadrado por segundo, afecta directamente a la cobertura y uniformidad de la superficie
4.2 Comparación de la ventana de proceso para diferentes microesferas cerámicas
Los tipos de microesferas cerámicas incluyen microesferas de alúmina, microesferas de óxido de circonio, microesferas de óxido de circonio estabilizado con itria y microesferas de óxido de circonio y sílice.
En el caso de las perlas de alúmina, el intervalo óptimo de presión es de 0,3 a 0,7 MPa, con un valor Ra de 1,5 a 3,0 μm. Tienen una uniformidad superficial moderada y se suelen utilizar en aplicaciones industriales generales y en piezas de automoción.
Las microesferas de circonio tienen un rango de presión óptimo de 0,2 a 0,6 MPa y un rango de valor Ra de 0,8 a 2,0 μm. Ofrecen una buena uniformidad superficial y suelen aplicarse en maquinaria de precisión y componentes aeroespaciales.
Las microesferas de circonio estabilizado con itria presentan un rango de presión óptimo de 0,1 a 0,5 MPa y un rango de valor Ra de 0,3 a 1,5 μm. Proporcionan una excelente uniformidad superficial y se utilizan en implantes médicos y componentes ópticos.
Las microesferas de zirconia-sílice tienen un rango de presión óptimo de 0,3 a 0,7 MPa y un rango de valor Ra de 1,2 a 2,5 μm. También tienen una uniformidad superficial moderada y son adecuadas para aplicaciones sensibles a los costes.
5. Medición precisa y caracterización de la rugosidad superficial
5.1 Técnicas avanzadas de medición
La caracterización precisa de las superficies tras el tratamiento con microesferas cerámicas requiere múltiples técnicas complementarias:
Perfilómetros de contacto: Miden parámetros unidimensionales como Ra, Rz
Interferómetros de luz blanca: Obtienen topografía superficial tridimensional y parámetros Sa
Microscopía de fuerza atómica (AFM): Análisis topográfico de superficies con resolución nanométrica
Microscopía electrónica de barrido (SEM): Evaluar la microtopografía superficial y los defectos
5.2 Evaluación de la funcionalidad de la superficie
Las diferencias funcionales de las superficies tratadas con diferentes microesferas cerámicas pueden evaluarse mediante las siguientes pruebas:
Medición del ángulo de contacto: Evaluación de la humectabilidad de la superficie, relacionada con la energía libre superficial
Prueba de adherencia del revestimiento: Evaluar la fuerza de adhesión del revestimiento mediante métodos de corte transversal o pull-off
Determinación del coeficiente de fricción: Evaluación de las propiedades tribológicas de la superficie
Ensayo de resistencia a la fatiga: Evaluar el impacto del tratamiento superficial en el rendimiento a fatiga de los componentes
6. Casos prácticos de aplicación
6.1 Optimización de superficies de componentes aeroespaciales de precisión
Un determinado álabe de compresor de motor de avión requiere un control estricto de la rugosidad superficial para mejorar la resistencia a la fatiga:
Reto: Conseguir una superficie uniforme con Ra=1,0±0,2μm a la vez que se mejora la resistencia a la fatiga
Solución:
Utilizar perlas de circonio estabilizadas con itria de 0,2 mm
Presión de procesamiento 0.3MPa
Distancia de procesamiento 120mm
ángulo de granallado perpendicular de 90
Tiempo de procesado 30 segundos
Resultados:
Obtención de una superficie uniforme con Ra=1,05μm
Aumento de la dureza de la superficie en un 22
Mejora de la resistencia a la fatiga en un 31
Prolongación de la vida útil de los componentes en un 45
6.2 Tratamiento de superficies de implantes médicos de aleación de titanio
Los implantes ortopédicos requieren una rugosidad específica para favorecer la integración ósea:
Reto: Crear una superficie uniforme con Ra=1,8±0,3μm evitando la contaminación
Solución:
Utilizar perlas de alúmina de 0,15mm de alta pureza
Presión de procesamiento 0.4MPa
Distancia de procesamiento 100mm
Tiempo de procesado segmentado 3 veces a 10 segundos cada una, con enfriamiento intermedio
Limpieza ultrasónica después del tratamiento
Resultados:
Conseguida una superficie uniforme con Ra=1,75μm
Los experimentos celulares in vitro mostraron un aumento del 62% en la tasa de fijación de células óseas
Tiempo de integración ósea reducido en 3 semanas en aplicaciones clínicas
La tasa de éxito de los implantes mejoró en un 5,8
Conclusión y perspectivas
La influencia de diferentes tipos de microesferas cerámicas en la rugosidad superficial es un campo científico complejo y preciso. Mediante un conocimiento profundo de las propiedades de los materiales, los mecanismos físicos y los parámetros de proceso de las distintas microesferas cerámicas, se puede lograr un diseño y un control precisos de la rugosidad superficial. Esto no sólo mejora el rendimiento y la vida útil del producto, sino que también abre nuevas posibilidades para las tecnologías de tratamiento de superficies personalizadas.
Con el desarrollo de la ciencia de los materiales y la ingeniería de superficies, surgirán materiales de microesferas cerámicas más especializados para satisfacer los requisitos precisos de diversas industrias en cuanto a microtopografía de superficies. Especialmente en los campos médico, aeroespacial y microelectrónico, el control preciso de la rugosidad superficial seguirá siendo una barrera tecnológica clave y un foco de investigación.
#Granallado de microesferas cerámicas Rugosidad superficial Tratamiento de superficies Circonia estabilizada con itria Microesferas de alúmina Fabricación de precisión Implantes médicos Materiales aeroespaciales