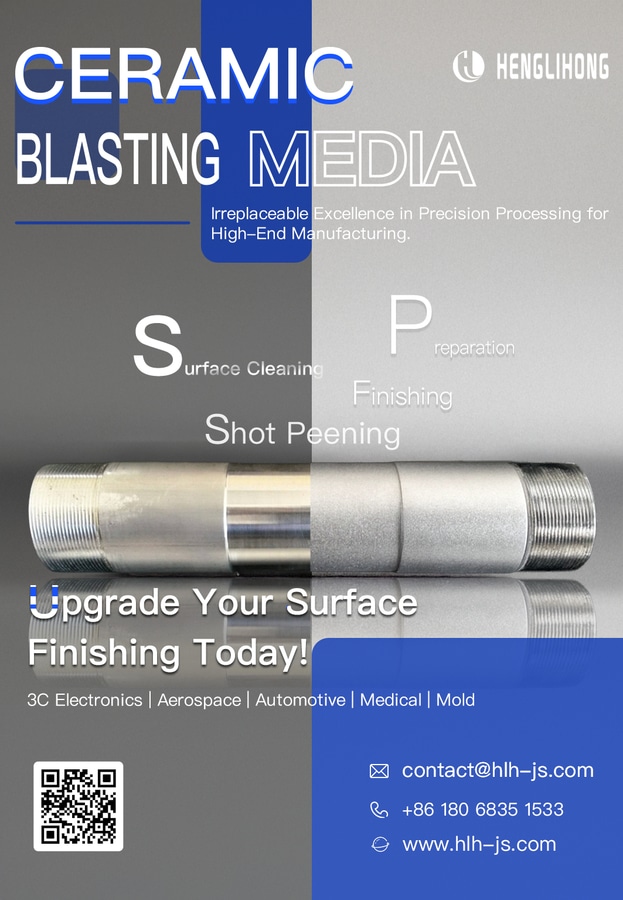
Ver traducción automática
Esta es una traducción automática. Para ver el texto original en inglés haga clic aquí
#Novedades de la industria
Aplicaciones industriales y perspectivas de la tecnología de chorreado de microesferas cerámicas
Explorando el futuro del tratamiento de precisión de superficies en la fabricación con la tecnología de chorreado de microesferas cerámicas
En el campo de la fabricación de precisión moderna, la tecnología de tratamiento de superficies desempeña un papel crucial. Con las crecientes exigencias de calidad superficial en industrias de alta tecnología como la electrónica, la aeroespacial y la de dispositivos médicos, las tecnologías tradicionales de granallado ya no pueden satisfacer los requisitos de procesamiento a nivel micrométrico. La tecnología de chorreado de microesferas cerámicas, como método emergente de tratamiento de superficies de alta precisión, se está convirtiendo gradualmente en un proceso indispensable en la fabricación de piezas de precisión. En este artículo se analizan en profundidad los principios, las aplicaciones y las tendencias de desarrollo de esta tecnología.
1. Principios técnicos
1.1 Características materiales de las microesferas cerámicas
Las microesferas cerámicas se fabrican principalmente a partir de materiales cerámicos de alta dureza, como óxido de circonio (ZrO₂), óxido de aluminio (Al₂O₃) o carburo de silicio (SiC), con diámetros que suelen oscilar entre 5 y 100 micras. Estos materiales poseen las siguientes características:
Dureza ultra alta: Dureza Mohs de 8-9,5, cercana a la del diamante
Excelente esfericidad: Esfericidad superior al 98%, lo que garantiza superficies de contacto uniformes
Estabilidad química: Resistente a ácidos y álcalis, no reactivo con la mayoría de los metales
Precisión dimensional: Distribución uniforme del tamaño de las partículas con desviación estándar controlada dentro de ±1μm
1.2 Mecanismo de trabajo
La tecnología de chorreado de microesferas cerámicas utiliza aire a alta presión o flujo de líquido como portador para proyectar microesferas cerámicas sobre la superficie de la pieza a velocidades controladas con precisión (20-120m/s) y ángulos (15°-90°). Los efectos de impacto microscópico producidos por la colisión de las microesferas cerámicas con la superficie consiguen una modificación precisa de ésta:
Microcorte: Los bordes de las microesferas cerámicas realizan microcortes en la superficie, eliminando capas superficiales de nivel nanométrico
Deformación plástica: Las fuerzas de impacto crean una deformación plástica microscópica en la superficie del material, aumentando la dureza de la superficie
Tensión nanocompresiva: Forma un campo de tensión compresiva en la capa superficial, mejorando la resistencia a la fatiga
Activación de la superficie: Aumenta los puntos activos de la superficie, lo que mejora la posterior adhesión del revestimiento
2. Equipo y parámetros del proceso
2.1 Componentes básicos del equipo
Los sistemas modernos de chorreado de microesferas cerámicas de nivel micrométrico suelen incluir los siguientes componentes:
Sistema de control de presión de alta precisión: Fluctuación de presión controlada dentro de ±0,01MPa
Dispositivo de clasificación de polvo a nivel de micras: Garantiza la consistencia del tamaño de las partículas
Sistema de control digital de la boquilla: Controla con precisión el ángulo y la distancia de proyección
Sistema óptico de control en tiempo real: Supervisa los efectos del procesamiento y ajusta los parámetros en tiempo real
Unidad de control ambiental: Temperatura controlada a 20±2℃, humedad a 45±5%
2.2 Parámetros clave del proceso y control
Parámetro, rango de control, factores de influencia
Presión de granallado: 0,1-0,8MPa, Rugosidad de la superficie, eficiencia de procesamiento
Diámetro del grano: 5-100μm, Morfología de la superficie, microestructura
Ángulo de proyección: 15°-90°, dirección de la fuerza de impacto, índice de eliminación de material
Distancia de proyección: 10-100mm, distribución de la energía, uniformidad del tratamiento
Tiempo de tratamiento: 5-300s, Integridad de la superficie, profundidad de tratamiento
Densidad de flujo del cordón: 2-20g/min-cm², Eficacia del tratamiento, calidad de la superficie
El control preciso de estos parámetros es crucial para lograr efectos superficiales ideales. Los sistemas modernos suelen emplear algoritmos de IA para ayudar a la optimización de parámetros, generando automáticamente combinaciones óptimas de parámetros en función de las características del material y los requisitos de procesamiento.
3. Campos de aplicación
3.1 Industria de semiconductores y microelectrónica
Procesamiento de precisión del marco de plomo: Aumenta la resistencia de la unión en un 30-50
Limpieza de sistemas microelectromecánicos (MEMS): Elimina los contaminantes microscópicos, mejorando el rendimiento hasta en un 15
Tratamiento del sustrato de embalaje de circuitos integrados: Mejora la humectabilidad de la superficie, aumentando la fiabilidad de la soldadura
3.2 Campo aeroespacial
Fortalecimiento de álabes de turbinas de gas: Aumenta la vida útil a la fatiga de los álabes hasta en un 40
Tratamiento de precisión de componentes hidráulicos: Reduce el coeficiente de fricción, prolongando la vida útil
Tratamiento superficial de tornillería aeroespacial: Mejora la resistencia a la fragilización por hidrógeno y a la corrosión
3.3 Dispositivos médicos
Modificación de la superficie del implante: Mejora la osteointegración, mejora la biocompatibilidad
Tratamiento de implantes dentales: Crea microestructuras que favorecen el crecimiento de los tejidos
Componentes de dispositivos médicos de precisión: Elimina microperforaciones y mejora la seguridad
4. Ventajas y limitaciones técnicas
4.1 Ventajas sobre las tecnologías tradicionales de voladura
Mayor precisión de procesado: Puede lograr una modificación superficial a nivel nanométrico, con valores Ra controlables dentro de 0,05-1,2μm
Integridad de la superficie: Prácticamente no produce microfisuras ni concentraciones de tensiones
Repetibilidad: Consistencia entre lotes superior al 95
Respeto del medio ambiente: Los materiales cerámicos pueden reciclarse, lo que reduce la generación de residuos
Control preciso del área: Puede lograr un tratamiento selectivo de zonas a nivel de micras
4.2 Limitaciones y desafíos técnicos
Coste de inversión en equipos: Los equipos profesionales suelen requerir una inversión de entre 500.000 y 2.000.000 de yuanes
Ventana de proceso estrecha: Altos requisitos de control de parámetros, operación difícil
Problemas de adaptabilidad para materiales específicos: Como materiales ultrablandos o determinados compuestos
Eficacia de la producción: Menor superficie tratada por unidad de tiempo en comparación con los métodos tradicionales
5. Últimas tendencias de desarrollo tecnológico
5.1 Inteligencia y gemelos digitales
Optimización de parámetros asistida por IA: Reduce el tiempo de prueba y error hasta en un 85%
Tecnología de gemelos digitales: Simulación en tiempo real del proceso de granallado, prediciendo la calidad de la superficie
Sistemas de control adaptativos: Ajuste automático de los parámetros del proceso en función de la información recibida en tiempo real
5.2 Nuevos materiales cerámicos
Microesferas cerámicas estructuradas con núcleo: Combinación de alta dureza y tenacidad
Cerámica nanocompuesta: mejora de la resistencia al desgaste y la estabilidad química
Microesferas cerámicas funcionalizadas: Modificación de la superficie con grupos funcionales específicos, logrando la activación química
5.3 Integración de procesos compuestos
Microvoladura asistida por electroquímica: Combinación de efectos electroquímicos para mejorar la eficiencia de eliminación de material
Granallado cerámico mejorado con láser: Utilización del pretratamiento láser para mejorar la precisión del procesado
Tecnología asistida por ultrasonidos: Potenciación de los efectos de impacto de las microperlas y reducción de la presión de proyección
6. Caso práctico: Tratamiento de palas Aero-Engine
Un fabricante de motores aeronáuticos adoptó microesferas cerámicas (ZrO₂, 20±2μm) para tratar álabes de turbina de aleación de alta temperatura, consiguiendo los siguientes resultados significativos:
Rugosidad superficial optimizada de Ra 1,8μm a Ra 0,4μm
La dureza superficial aumentó un 42%, de HV320 a HV455
La profundidad de la capa de tensión compresiva superficial alcanzó los 25μm, mejorando la vida a fatiga en un 35%
La adherencia del revestimiento de barrera térmica mejoró en un 50%, prolongando la vida útil en 2.000 horas
Aumento de la eficiencia de producción en un 20%, con una reducción del 75% en la tasa de reprocesamiento
Este caso valida plenamente el rendimiento superior de la tecnología de granallado cerámico micrométrico en el tratamiento superficial de piezas de precisión de gama alta.
7. Guía de implementación del proceso y control de calidad
7.1 Flujo de trabajo de implantación de procesos
Pretratamiento: Limpieza por ultrasonidos para eliminar el aceite y las partículas
Diseño de parámetros: Establecimiento de parámetros iniciales basados en las características y requisitos del material
Validación de muestras: Pruebas de lotes pequeños y análisis de superficies
Procesamiento formal: Control de las condiciones ambientales, ejecución de las operaciones de granallado
Inspección de calidad: Rugosidad superficial, morfología y pruebas de rendimiento
Tratamiento posterior: Neutralización de la superficie, eliminación de partículas cerámicas residuales
7.2 Control de calidad y métodos de ensayo
Elemento de ensayo, equipo de ensayo, norma de control
Rugosidad de la superficie: Confocal láser / Microscopio, Ra ±0.05μm
Morfología de la superficie: SEM de emisión de campo, sin microfisuras, distribución uniforme de partículas
Capa de tensión de compresión: Analizador de tensión de rayos X, valor de tensión -300±30MPa
Dureza de la superficie: Probador de nanoindentación, desviación de la dureza <5%
Actividad superficial: Medidor del ángulo de contacto, Reducción del ángulo de contacto >40%
Conclusión
Como proceso de vanguardia para el tratamiento superficial de piezas de precisión, la tecnología de granallado cerámico a nivel micrométrico sigue rompiendo las limitaciones del procesamiento tradicional, proporcionando un potente apoyo técnico a las industrias de fabricación de alta tecnología. Sus aplicaciones en el sector aeroespacial, los dispositivos médicos, los semiconductores y otros campos han impulsado fuertemente el progreso tecnológico en estas industrias. Con el desarrollo de la fabricación inteligente y las nuevas tecnologías de materiales, la tecnología de microgranallado cerámico seguirá integrando conceptos avanzados como la inteligencia artificial y los gemelos digitales para lograr una mayor precisión y un tratamiento más eficaz de las superficies, lo que brindará nuevas oportunidades de desarrollo para la fabricación de precisión.
A la hora de introducir esta tecnología, las empresas deben considerar exhaustivamente los costes de inversión, los requisitos técnicos y los escenarios de aplicación para formular estrategias de implementación razonables que permitan aprovechar plenamente su potencial en la mejora de la calidad del producto y la optimización de costes.
Palabras clave: #MicronCeramicBeads #BlastingTechnology #SurfaceTreatment #PrecisionManufacturing #Aerospace #MedicalDevices